Measurement systems are pivotal across various industries, ensuring accuracy, efficiency, and reliability in processes and products. These systems, encompassing a broad array of tools, technologies, and methodologies, are integral to maintaining standards and achieving precision in both production and quality control.
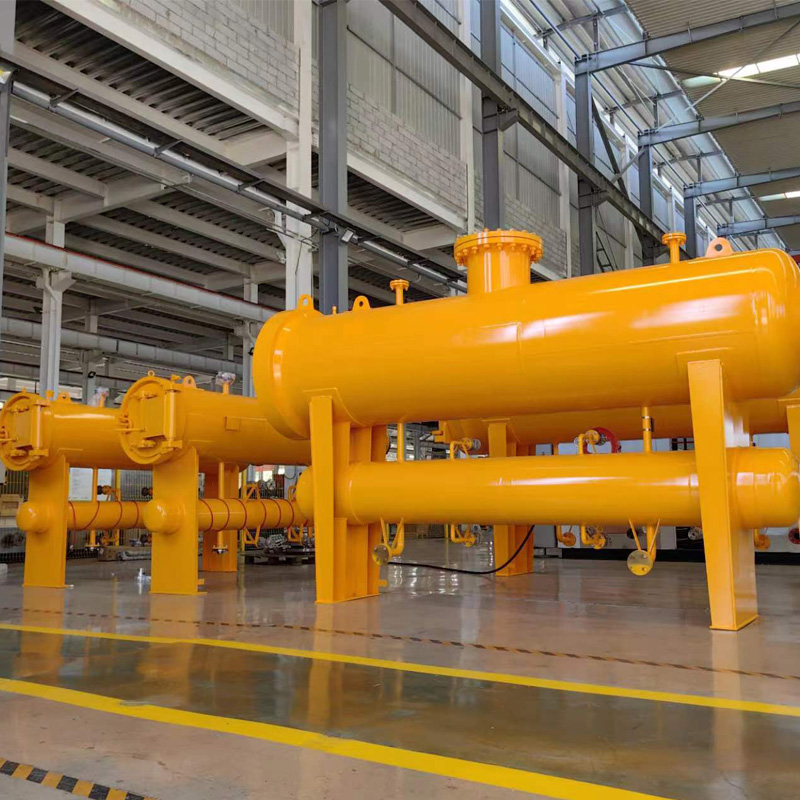
In the realm of tangible products, measurement systems are crucial from the initial stages of design to the final stages of production. Engineers rely on these systems to convert innovative designs into real-world applications, ensuring that each component adheres to exact specifications. Using state-of-the-art technology, measurement systems can detect minute discrepancies that human eyes might overlook. Today, advanced digital measurement tools, such as laser scanners, are widely used for 3D modeling, offering an unmatched level of detail and precision.
Industries like pharmaceuticals, automotive, and aerospace are quintessential examples where robust measurement systems are indispensable. In pharmaceuticals, precise measurement systems are used to ensure the correct dosage and composition of drugs. This not only guarantees efficacy but also ensures patient safety. Meanwhile, in the automotive and aerospace sectors, measurements made during manufacturing are critical to ensuring the safety and performance of vehicles and aircraft. A single miscalculation could have significant implications, ranging from operational inefficiencies to life-threatening failures.
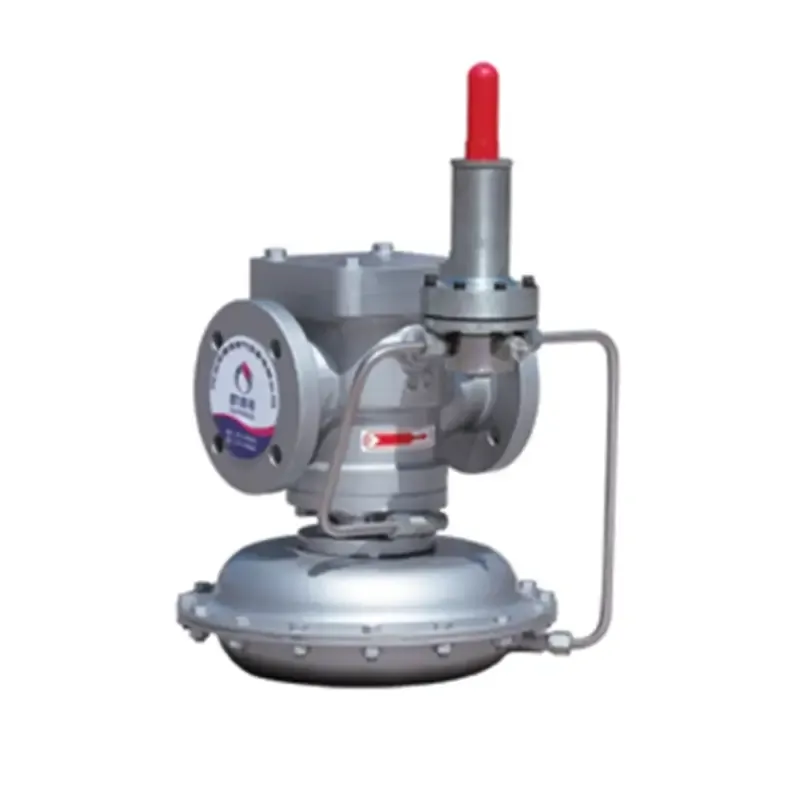
Moreover, the digital transformation has propelled the evolution of measurement systems, incorporating artificial intelligence (AI) and the Internet of Things (IoT). AI-powered measurement tools can analyze vast amounts of data in real-time, providing actionable insights and automatic adjustments in manufacturing processes. IoT-enabled sensors significantly enhance remote monitoring capabilities, allowing users to track performance and make necessary adjustments from virtually anywhere.
Measurement systems
Despite the technological advancements, the effectiveness of a measurement system largely hinges on calibration. Regular calibration ensures that measurement systems remain accurate, reliable, and consistent over time. This process involves comparing the measurement outputs of a device to a standard of known accuracy and making necessary adjustments. Accredited calibration services are therefore crucial for businesses aiming to maintain the integrity of their measurement tools.
For businesses looking to implement or upgrade their measurement systems, engaging with expert consultants can be beneficial. Specialists provide guidance on selecting the right tools based on industry-specific requirements, company size, and budget constraints. Furthermore, they offer training for staff, ensuring that all team members can effectively operate these systems and interpret data for optimal business outcomes.
Trust in any measurement system is built through transparency and adherence to international standards. Discussing compliance with standards such as ISO, ASME, or others relevant to specific industries, adds a layer of credibility and reassures clients and stakeholders of the system’s reliability. Businesses that certify their measurement systems as compliant with these international standards often find themselves in a more favorable position when entering global markets.
In conclusion, as technology continues to evolve, so too will the ways in which measurement systems enhance productivity and innovation. Investing in cutting-edge measurement systems is not just a business decision; it is a commitment to producing high-quality products and maintaining competitive edges in a demanding market.