A heat exchanger, often nestled in the core of modern industrial applications, is pivotal for the energy efficiency and operational efficacy of many systems. Whether found in power plants, refineries, or HVAC systems, this equipment promotes thermal exchange between two or more fluids, playing a crucial role in maintaining optimal process conditions. With an impressive array of designs tailored for diverse needs, understanding the nuances of heat exchangers can significantly enhance system performance and reduce operational costs.
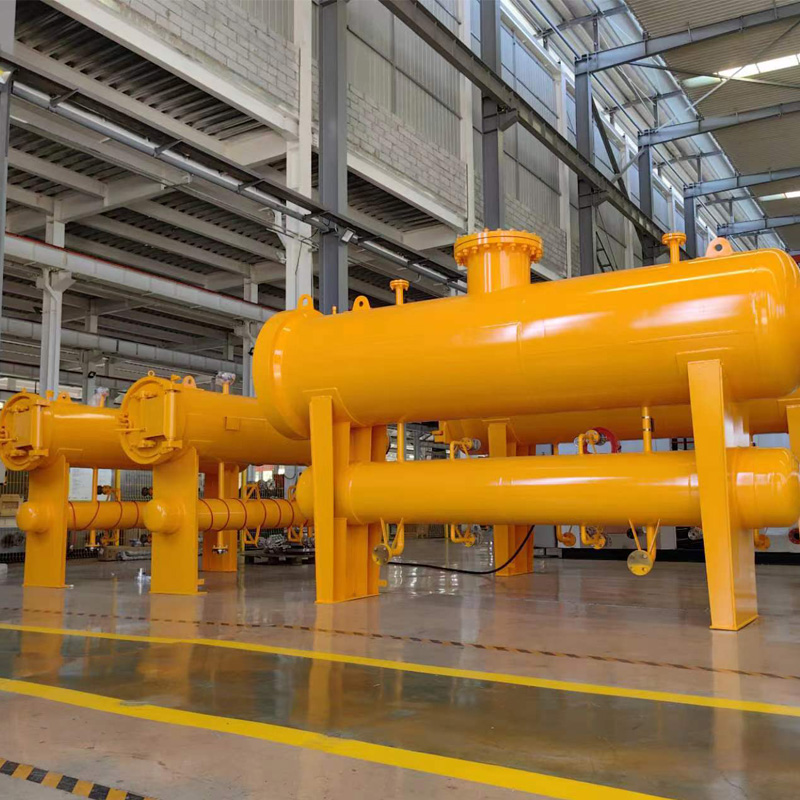
In the realm of product expertise, it is essential to delineate the major types of heat exchangers, each bringing its unique advantages to specific applications.
Shell-and-tube heat exchangers are revered for their robustness and versatility. Their design allows for effective temperature handling and pressure drop management, suitable for industries dealing with high-pressure fluids. Plate heat exchangers, on the other hand, shine in scenarios demanding compact designs with efficient heat transfer capabilities, attributed to their large surface area to volume ratio.
From an engineering standpoint, the expertise surrounding heat exchanger selection and maintenance cannot be understated. The material choice for these devices, which often include stainless steel, titanium, or even exotic alloys, is critical in curbing corrosion, a common challenge that can compromise the exchanger’s longevity and efficiency. Furthermore, regular maintenance schedules involving cleaning and inspection ensure the removal of fouling deposits, which could otherwise degrade the thermal performance over time.
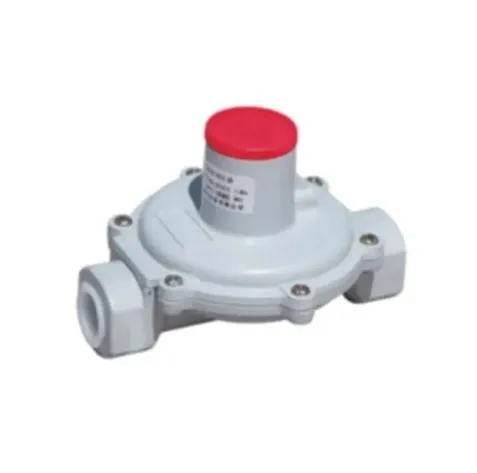
To delve deeper into the authoritativeness of heat exchanger applications, it's pivotal to explore how industries capitalize on these devices to adhere to stringent environmental regulations and sustainability goals. In the oil and gas industry, for example, heat exchangers contribute significantly towards energy optimization. By recovering heat from waste streams, they minimize energy consumption, thereby lowering greenhouse gas emissions.
Heat exchanger
Moreover, in the food and beverage industry, the role of heat exchangers is increasingly recognized for preserving product quality while ensuring compliance with hygiene standards. Their ability to maintain temperatures at desired levels, without compromising safety or taste, underscores their irreplaceable value in pasteurization and other critical processes.
From a trustworthiness perspective, the impact of innovative technologies on heat exchanger efficiency warrants attention. Modern advancements such as augmented reality (AR) and the Internet of Things (IoT) are being integrated into predictive maintenance programs. This fusion of technology accelerates the detection of potential issues, facilitates real-time monitoring, and ensures that maintenance interventions are performed proactively, thus safeguarding the equipment's integrity.
Furthermore, computational fluid dynamics (CFD) simulations provide a reliable methodology for equipment customization and process optimization. By simulating various operational scenarios, CFD helps in validating the heat exchanger designs and optimizing the fluid flow paths, testament to the empirical reliability that supports investment decisions in this technology.
In summary, the incorporation of heat exchangers in industrial applications is not merely a matter of preference but a strategic imperative that combines experience, expertise, authoritativeness, and trustworthiness. As industries continue to grapple with the demands of efficiency and sustainability, the evolving landscape of heat exchanger technology presents unparalleled opportunities. By understanding their multifaceted applications and maintenance intricacies, businesses can optimize thermal performance, enhance productivity, and contribute to a greener planet.