Shut-off valves represent a critical component in numerous industrial, commercial, and residential systems across the globe. Their primary function is to completely stop or allow the flow of a substance, typically liquid or gas, through a pipe or passage. Given the fundamental role these valves play, understanding their capabilities, variations, and appropriate applications becomes paramount.
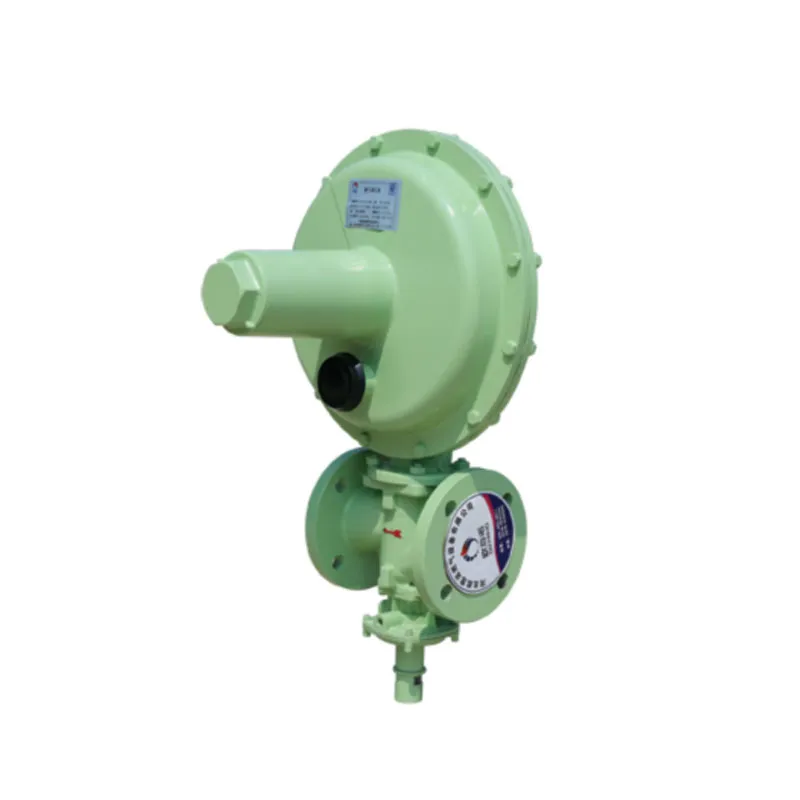
Experience demonstrates that shut-off valves are indispensable in industries such as oil and gas, water treatment, chemical processing, and HVAC systems. Their reliability in preventing leaks and facilitating maintenance work highlights their critical importance. For instance, in an industrial scenario where a pipeline needs repairs, a shut-off valve ensures that the flow of potentially hazardous materials can be completely stopped, guaranteeing the safety of maintenance personnel and reducing the risk of environmental contamination.
Expertise within the field indicates that shut-off valves come in various designs, each suited for specific applications. The most commonly employed types include gate valves, ball valves,
and globe valves. Each has unique characteristics that determine their suitability for different tasks. Gate valves are typically used where a straight unobstructed flow is crucial. They are on/off valves that, when fully open, have no obstruction in the flow path, resulting in minimal pressure drop.
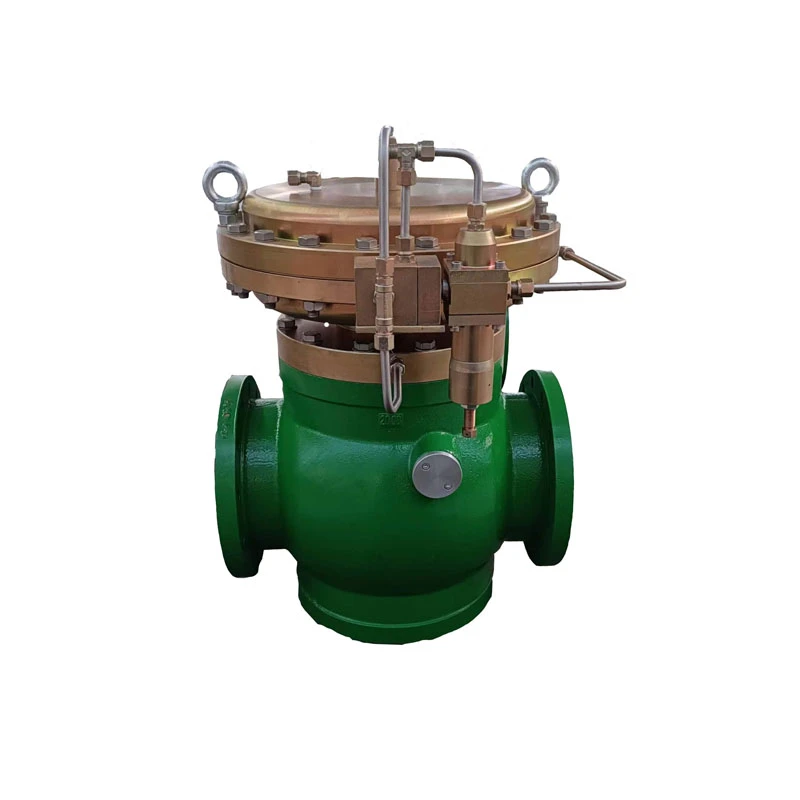
Ball valves, on the other hand, are recognized for their durability and reliability in harsh conditions. They offer a tight seal and quick rotation, making them ideal for applications that require frequent operation. In contrast, globe valves are preferred for regulating flow rather than on/off control. Their design allows for precise throttling, which makes them suitable in applications where the flow needs to be varied.
Close the valve
The authoritativeness of shut-off valves is underscored by the rigorous standards to which they are manufactured and tested. Organizations such as the American National Standards Institute (ANSI) and the International Organization for Standardization (ISO) provide strict guidelines that manufacturers must adhere to, ensuring that the valves operate safely under designated pressure and temperature conditions. This authoritative endorsement gives users confidence in their performance and reliability.
Trustworthiness in shut-off valves is achieved through the use of high-quality materials and meticulous manufacturing processes. Most valves are made of corrosion-resistant materials like stainless steel, brass, or PVC, ensuring longevity even in corrosive environments. The manufacturers' commitment to quality is reflected in the precision engineering that guarantees each valve can perform its function effectively over a long lifespan, thus maintaining system integrity and reducing downtime.
Furthermore, the choice of a suitable shut-off valve profoundly impacts the efficiency and safety of the overall system. Selecting the correct valve type and material can result in reduced maintenance costs and prolonged equipment life. It's also essential to consider the operating environment, as factors such as temperature, pressure, and the nature of the fluid or gas being controlled can significantly influence valve performance.
In conclusion, shut-off valves are a cornerstone in numerous applications, offering control and safety in fluid management systems. Their diverse designs meet a broad spectrum of operational needs, supported by authoritative standards and reliable manufacturing processes. The right choice and implementation of a shut-off valve ensure not only functionality and safety but also enhance system efficiency and cost-effectiveness. When selecting a valve, consulting with experts and referring to reliable resources is highly recommended to ensure optimal performance and adherence to industry standards.