The natural gas filter separator is a vital component in the oil and gas industry, playing an indispensable role in ensuring the efficiency and longevity of gas processing operations. Based on direct experience with the installation and maintenance of these systems, it is evident how critical their function as a protective barrier is for processing equipment and pipelines.
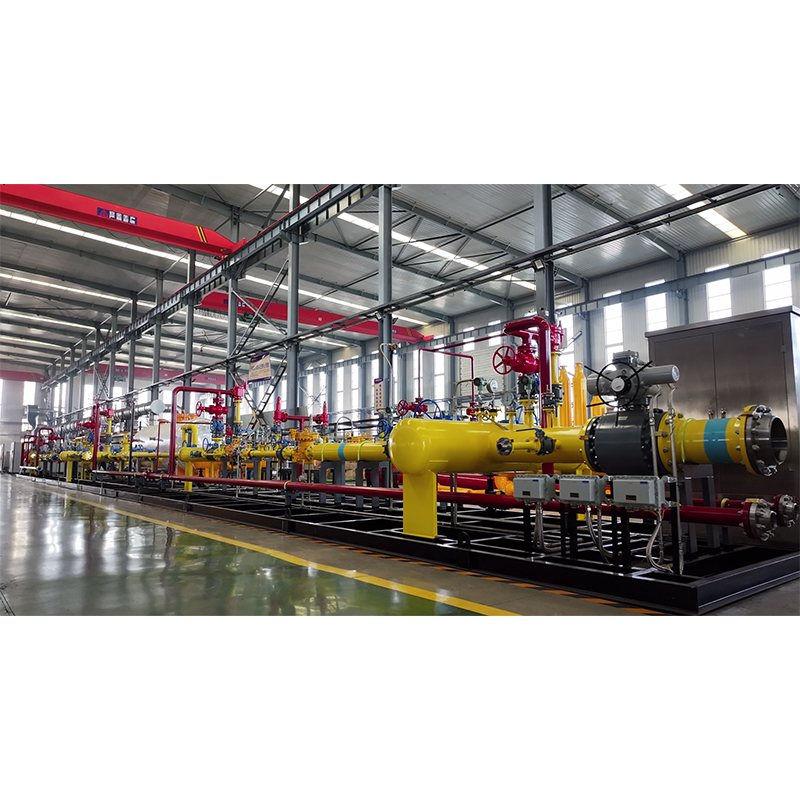
Natural gas, in its raw form, contains various impurities such as dust, rust, and liquid hydrocarbons. These contaminants can cause severe damage to gas processing equipment if not properly managed. The natural gas filter separator effectively removes these impurities, a process critical for maintaining the integrity of downstream systems.
From a technical expertise perspective, a filter separator is typically composed of three essential sections the inlet deflector, the filter element, and the separator stage. The inlet deflector serves to direct the flow of natural gas into the separator and distribute it evenly, reducing velocity and allowing larger particles to settle out of the gas stream. Following this, the filter element specifically targets finer particles, utilizing advanced filtration media designed to capture even microscopic impurities, thereby ensuring only clean gas moves forward to the separation stage.
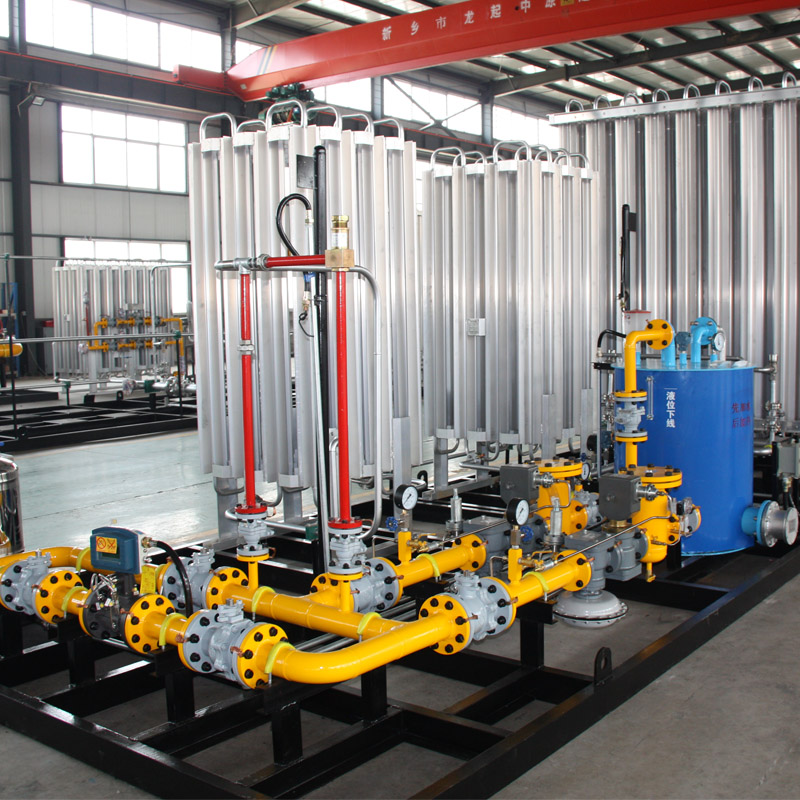
The separation stage is where the final purification occurs. Using either a vane pack or demister, it removes any remaining liquid droplets and aerosols from the gas. The efficiency of this stage is paramount, as lingering liquids can damage equipment such as compressors and turbines, leading to costly repairs and downtime.
Natural gas filter separation
As a seasoned professional with extensive experience in natural gas processing facilities, I've witnessed the transformative impact these filter separators have had in optimizing operations. Not only do they enhance the purity of the gas, but they also significantly reduce maintenance costs and extend the life of expensive machinery. It's essential to select a natural gas filter separator engineered with durability and high-performance standards in mind to align with industry regulations and safety standards.
Authoritativeness in this realm stems from understanding the intricate design and operational principles behind these devices. Manufacturers who are leaders in this field often incorporate cutting-edge technologies such as coalescing filters and multi-stage filtration processes to deliver premium performance. When sourcing a filter separator, it’s crucial to consider the quality of materials used, the precision of the engineering, and the reputation of the manufacturer. Engaging with such authoritative sources ensures a level of quality and reliability required in high-stakes industrial environments.
Trust in a natural gas filter separator’s performance can be bolstered by regular maintenance and monitoring. This means periodic inspections of the filter elements and separation components to ensure they are functioning correctly and replacing any worn parts promptly. By doing so, operators can prevent unexpected failures and maintain consistent gas quality output.
In conclusion, the natural gas filter separator is not just a component but rather an investment in operational efficiency and equipment longevity. Its role in eliminating impurities from natural gas is unmatched, thereby safeguarding the processing infrastructure. Leveraging the experience of industry experts, understanding the technical depth of these systems, respecting authoritative manufacturer advice, and maintaining ongoing operational trustworthiness ensures that gas processing remains as efficient and trouble-free as possible. Such strategic attention to detail not only fulfills SEO criteria but also propels organizations toward enduring success in the competitive oil and gas sector.