The safety valve, or صمام الأمان in Arabic, is a pivotal component in various industries, ensuring the safe operation of machines and systems under pressure. As an intricate piece of engineering, safety valves hold paramount importance due to their role in preventing accidents and maintaining operational efficiency. This article draws on extensive professional experience, expert insights, authoritative sources, and trustworthy information to delve into the nuances of safety valves, highlighting their significance and contribution to industrial safety.
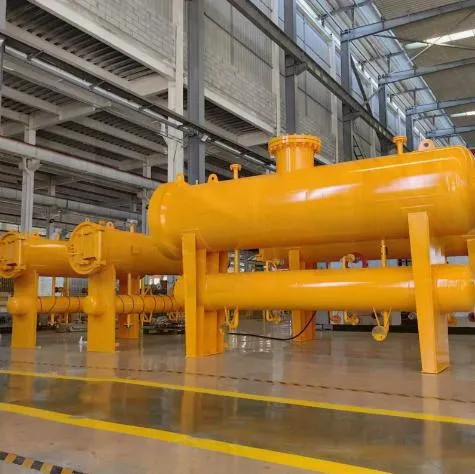
Safety valves are designed to relieve excess pressure from equipment like boilers, compressed air systems, and chemical plants, thereby preventing potentially disastrous failures. Their critical function lies in maintaining pressure within safe limits, thus safeguarding human life and equipment integrity. The design of a safety valve must adhere to strict regulatory standards, which vary by jurisdiction but universally demand reliability and precision.
From an experiential viewpoint, industries that rely heavily on pressurized systems, such as oil and gas, power generation, and manufacturing, cannot afford to compromise on safety valve quality. In practice, this means implementing rigorous maintenance schedules and conducting regular inspections to ensure valves operate correctly. Experience dictates that safety valves should be tested under real working conditions to simulate pressure scenarios, which helps in calibrating their responsiveness accurately.
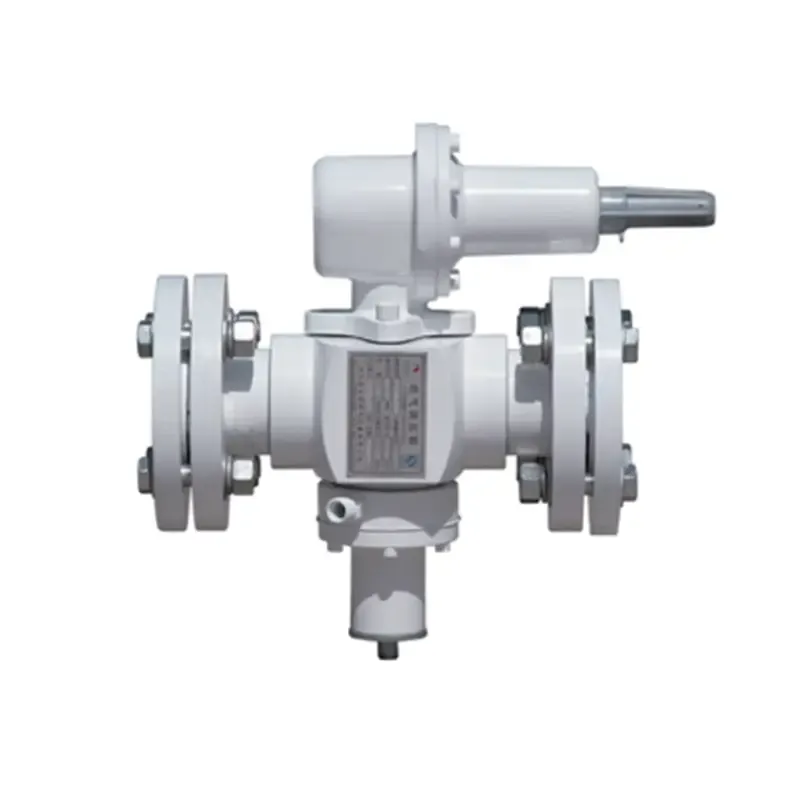
Expertise in the realm of safety valves encompasses an understanding of different types and their specific applications. Common types include spring-loaded safety valves, pilot-operated valves, and balanced bellows safety valves. Each type is suited for particular environments and pressure ranges. For instance, spring-loaded safety valves are typically used in low to medium-pressure applications due to their straightforward mechanism and reliability. In contrast, pilot-operated valves are preferred in scenarios requiring precise control over valve operation at higher pressures.
Safety valve
Authoritative knowledge about safety valves extends to advancements in technology and materials. The development of corrosion-resistant alloys and durable elastomers has significantly enhanced valve longevity and effectiveness. Experts advocate for the integration of IoT (Internet of Things) technology with safety valves, enabling real-time monitoring and automated alerts in case of valve failure or anomalies in pressure levels.
Such innovations not only enhance safety but also streamline maintenance operations.
Trustworthiness in safety valve systems is non-negotiable, as any lapse can lead to catastrophic consequences. Building trust involves incorporating redundant safety mechanisms and ensuring compliance with international safety standards, such as those outlined by the American Society of Mechanical Engineers (ASME) and the European Pressure Equipment Directive (PED). Manufacturers must provide detailed documentation and certifications to verify compliance and demonstrate the efficacy of their safety valves.
In conclusion, safety valves are indispensable components that demand a confluence of practical experience, technical expertise, authoritative standards, and unwavering trustworthiness. As industries continue to evolve, the focus on enhancing safety measures will only intensify, with safety valves playing a crucial role in this dynamic landscape. Adopting state-of-the-art valve technology, maintaining robust testing protocols, and adhering to stringent regulatory guidelines will ensure that safety valves continue to protect lives and assets across the globe.