Gas pressure vessels play a crucial role in various industrial sectors, ensuring safe and efficient storage and transportation of gases. These vessels are designed to withstand high pressure and provide a safe environment to store gases ranging from natural gas to industrial ones like oxygen, hydrogen, and nitrogen. Understanding the intricacies of gas pressure vessels can help industries make informed decisions, enhancing both safety and productivity.
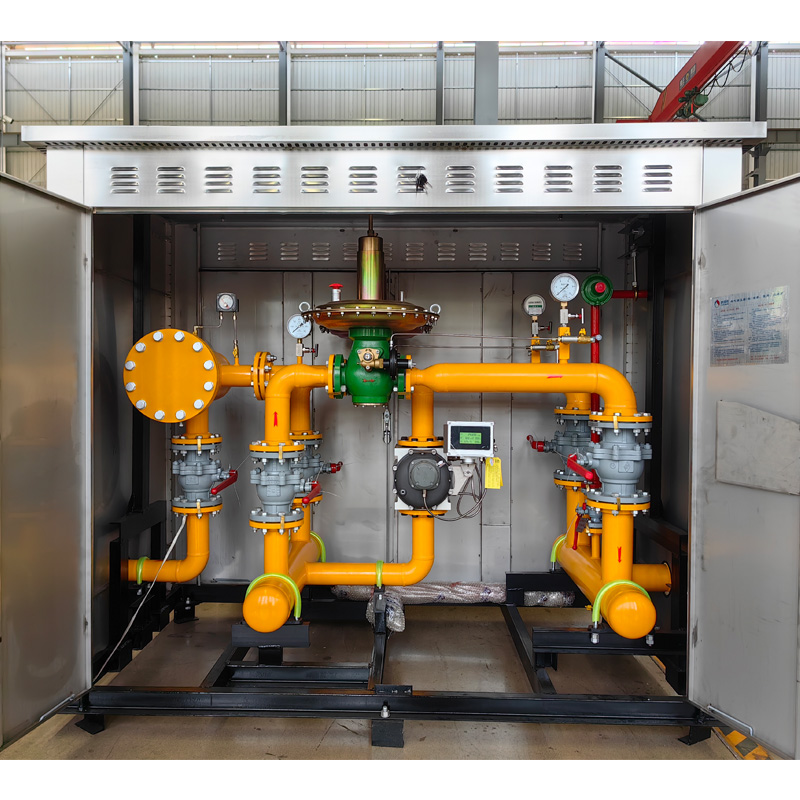
Experience in managing and utilizing gas pressure vessels provides valuable insights into their efficiency and safety. Industries such as energy, healthcare, and manufacturing rely heavily on these vessels. For instance, in the energy sector, gas pressure vessels are used to store compressed natural gas (CNG), facilitating easy transportation and reducing the reliance on pipeline infrastructure. In healthcare, oxygen cylinders, a type of pressure vessel, are critical for patient care, providing life-saving support in medical facilities. Having first-hand experience in handling these vessels ensures that they are used to their full potential, reducing risks associated with pressure-related incidents.
Expertise in gas pressure vessels encompasses understanding their design, materials, and functionality. Engineers and manufacturers must consider factors such as the type of gas stored, temperature fluctuations, and external environmental conditions when designing these vessels. Typically made from high-strength steel or composites, gas pressure vessels must adhere to strict industry standards and regulations, such as ASME (American Society of Mechanical Engineers) standards, to ensure they can withstand the rigorous demands of industrial applications. Manufacturers with deep expertise in material science and mechanical engineering are vital to producing reliable and durable pressure vessels.
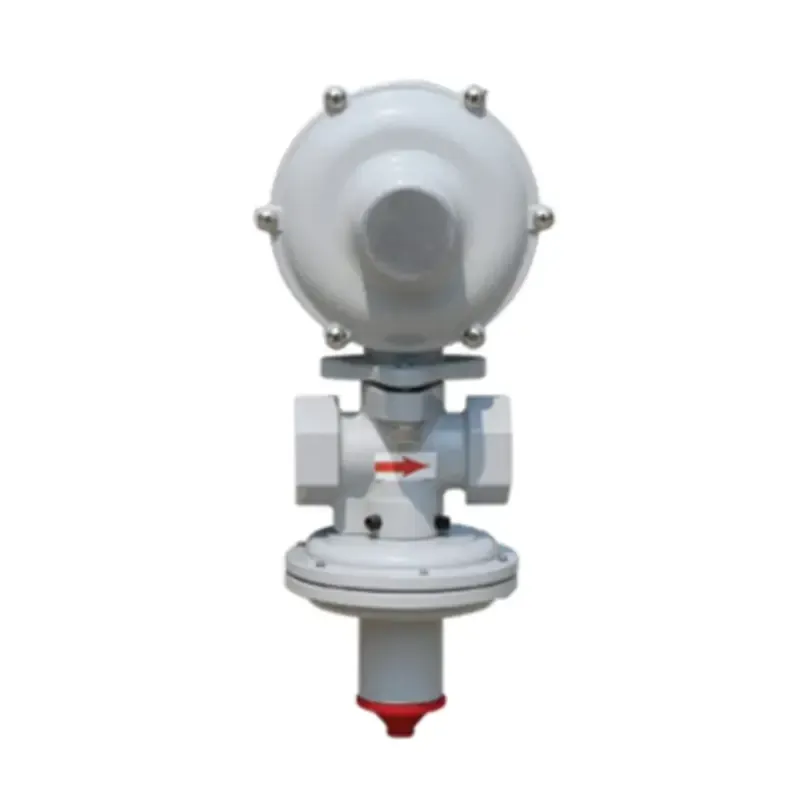
Gas pressure vessel
Authority in the domain of gas pressure vessels is established through continuous research and development, innovation, and adherence to safety standards. Leading companies in this field invest heavily in R&D to develop advanced materials and innovative designs that can handle higher pressures and offer greater resilience to environmental stresses. By pioneering new technologies, these companies provide solutions that improve the safety and efficiency of gas storage, positioning themselves as authorities in the industry. Collaboration with regulatory bodies and participation in industry forums further solidifies their standing, allowing them to influence the development of standards that govern pressure vessel manufacturing.
Trustworthiness is paramount when it comes to gas pressure vessels, given the potential risks involved in their use. Ensuring trust requires a commitment to quality throughout the manufacturing process, from design and material selection to testing and certification. Thorough testing of pressure vessels, including hydrostatic testing and ultrasonic examination, is essential to verify their integrity and durability. Companies that prioritize transparency and maintain open communications with clients about testing methods, certification processes, and safety records establish a foundation of trust. Providing warranties and after-sales support further enhances reliability, offering clients assurance that they are investing in safe and quality equipment.
In conclusion, the importance of gas pressure vessels in various industrial applications cannot be overstated. Their role in ensuring safe storage and transportation of gases is vital to the operations of many sectors. Understanding the experience, expertise, authority, and trustworthiness associated with these vessels allows businesses to make informed purchasing decisions. By choosing manufacturers that excel in these areas, industries can enhance their operational safety, efficiency, and sustainability, leveraging the full potential of gas pressure vessels while minimizing risks and costs.