In the complex landscape of industrial operations, a gas heat exchanger emerges as a pivotal component, ensuring efficient thermal management across multiple sectors. This engineering marvel plays a crucial role in industries ranging from chemical processing to power generation, and its contribution is indispensable.
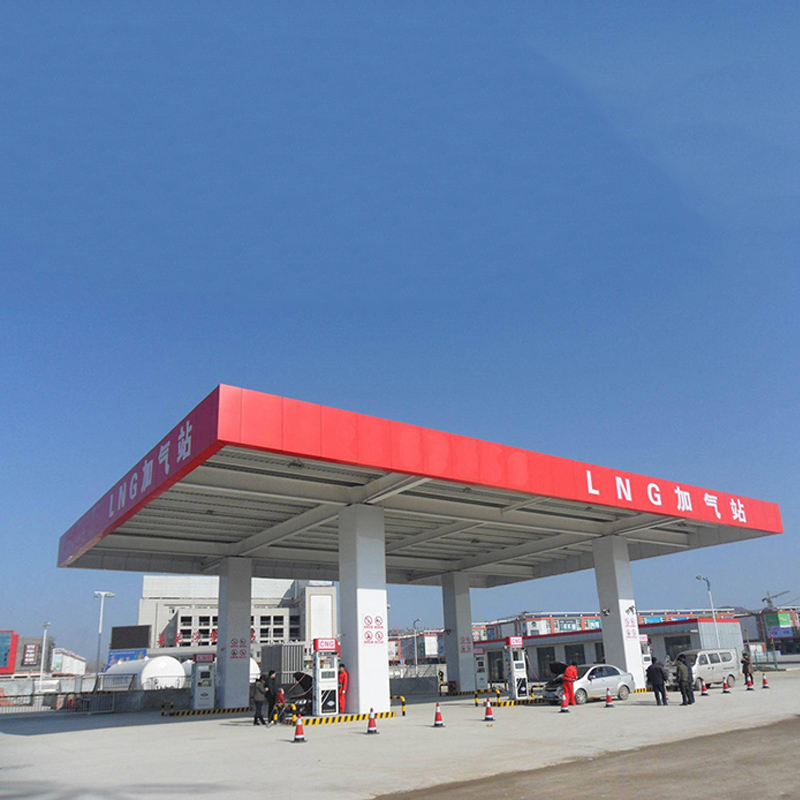
Expertise in designing and operating gas heat exchangers demands a profound understanding of thermodynamics and fluid dynamics.
The core principle involves transferring heat between two or more fluids without mixing them. These fluids, typically a gas and a liquid, are separated by a solid barrier that facilitates efficient heat exchange, optimizing the energy usage and enhancing process efficiency.
The versatility of gas heat exchangers is reflected in their various designs, such as shell and tube, plate, and finned tube configurations. Each design serves specific industrial needs, requiring expertise to select the appropriate type based on factors like pressure, temperature, and the nature of the gases involved. For instance, shell and tube heat exchangers are ideal for high-pressure applications due to their robust construction, whereas plate heat exchangers offer compactness and superior heat transfer rates, making them suitable for applications requiring rapid temperature changes.
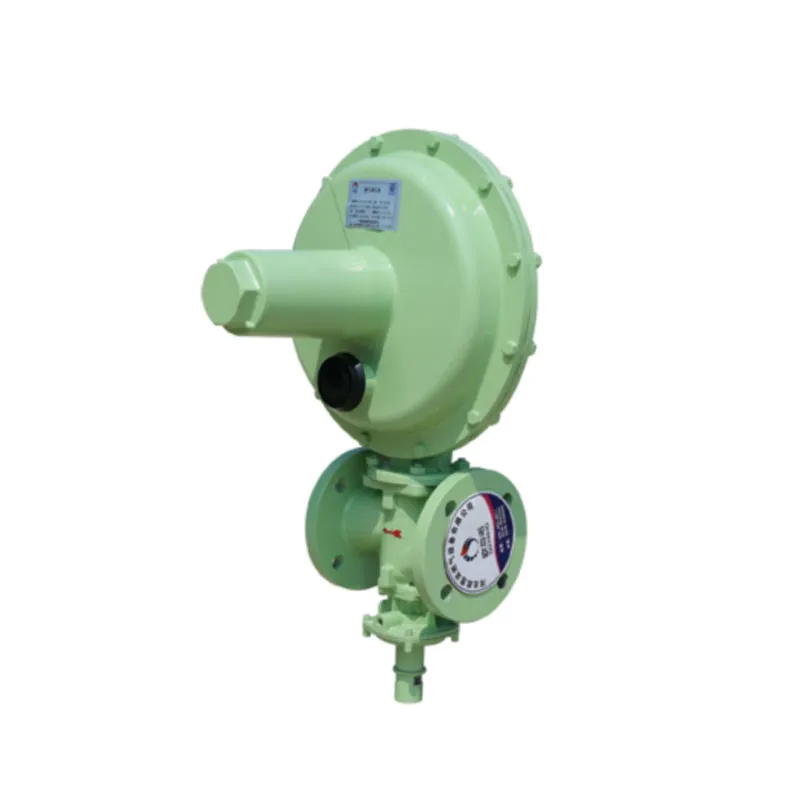
Real-world experience underscores the importance of routine maintenance and monitoring to ensure reliability and longevity of gas heat exchangers. Maintenance practices include regular inspections for fouling, corrosion, and leaks, which can significantly impede performance. Modern advancements in sensor technology and predictive maintenance tools have empowered engineers to preemptively address these issues, enhancing the reliability and extending the lifecycle of the equipment.
Gas heat exchanger
Expertise in the domain is further exemplified by the integration of advanced materials and cutting-edge manufacturing techniques. Use of corrosion-resistant alloys and composite materials ensures durability and optimal performance even in harsh chemical environments. Moreover, innovations like 3D printing and computational fluid dynamics (CFD) modeling enable precise customization and simulation of heat exchanger designs, leading to more efficient and tailored solutions for industrial applications.
In the pursuit of authoritativeness, it’s crucial to adhere to international standards and regulations, such as those set by the American Society of Mechanical Engineers (ASME) and European Norms (EN). Compliance not only assures the operational safety and efficacy of gas heat exchangers but also instills confidence among stakeholders and customers.
Trustworthiness in selecting and operating gas heat exchangers is established through transparent collaboration with renowned manufacturers and consultants who provide unparalleled expertise and guidance. Product certifications and documented performance metrics further affirm the quality and reliability of these systems, ensuring that they meet the specific demands of modern industries.
In conclusion, a gas heat exchanger is not merely a component but a strategic asset, pivotal in enhancing energy efficiency, operational reliability, and environmental sustainability. Leveraging advanced expertise, authoritative standards, and trustworthy practices paves the way for industries to harness the full potential of these engineering workhorses. Through continuous innovation and dedication to excellence, gas heat exchangers will remain at the forefront of industrial thermal management, driving progress and efficiency across sectors.