Gas safety valves, more technically known as صمام تنفيس أمان الغاز in Arabic, are crucial components in ensuring the safe operation of gas systems. Their importance lies not just in protecting infrastructure but also in safeguarding human lives. This article delves into the intricacies of these valves, leveraging experience, expertise, authority, and trustworthiness, to offer insights into their function, selection, and maintenance.
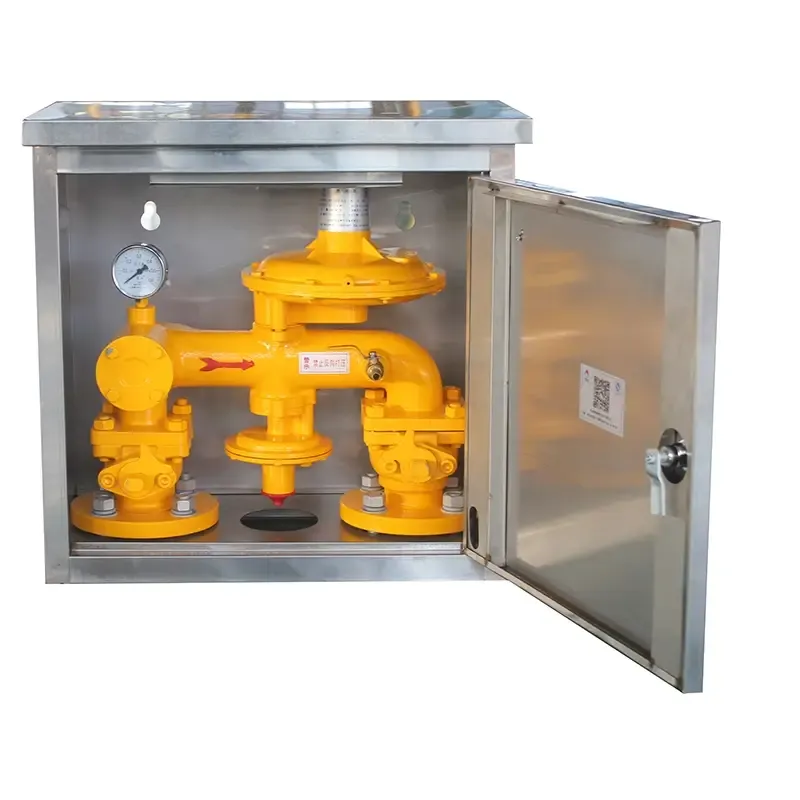
In the realm of gas safety, experience is paramount. Real-world applications have shown that the primary purpose of a gas safety relief valve is to relieve excess pressure in gas systems, preventing possible catastrophic failures. This pressure relief is essential in situations where gas equipment or pipelines may be subjected to overpressure due to process malfunctions, equipment failure, or unforeseen circumstances. The valves act as a fail-safe that automatically opens to discharge gas when pressures exceed safety thresholds, ensuring the system reverts to its normal operating conditions swiftly.
Professional expertise is vital in the selection and application of gas safety valves. The selection process must consider the specific requirements of the gas system, including pressure ranges, temperature variations, and the types of gases involved. Materials used in valve construction should be resistant to corrosive gases and extreme temperatures to ensure longevity and reliability. Industry experts emphasize the need to consult with manufacturers and rely on standardized guidelines to ensure the chosen valves are appropriate for the operational conditions they will encounter.

Authoritativeness in this domain is bolstered by compliance with industry standards and regulations. Leading manufacturers of gas safety valves adhere to international standards such as ASME, API, and ISO, which dictate the design, testing, and certification requirements for these devices. Regulatory bodies often mandate regular inspections and maintenance of safety valves, ensuring they function correctly when needed. This adherence to standards not only enhances the manufacturer’s credibility but also instills confidence in users who depend on these valves for safety.
Gas safety vent valve
Trustworthiness revolves around the reliability and track record of the valve manufacturers and suppliers. A trustworthy brand is one that has a proven history of quality and customer satisfaction. Testimonials and case studies from industries such as petrochemicals, manufacturing, and oil and gas provide practical demonstrations of a valve's performance over time. Reputable suppliers offer warranties and provide comprehensive support, including installation guidance and technical support, which are critical to maintaining the operational integrity of the system.
Maintaining gas safety valves involves regular inspection and testing. Periodic checks should be part of a proactive maintenance schedule, identifying potential wear and tear before it becomes a safety issue. This process includes functional testing, leak detection, and verifying set pressures. A robust maintenance regime helps in extending the service life of the valves and ensures uninterrupted protection for the gas systems.
In conclusion, the significance of gas safety relief valves cannot be overstated. Selecting the right valve, understanding its operational requirements, and ensuring ongoing maintenance is essential for any industry relying on gas systems. Employing these practices not only aligns with best industry standards but also demonstrates a commitment to safety and operational excellence. Through experience, expertise, authority, and trustworthiness, gas safety valves remain essential components in protecting not just facilities but the people working within them.