The pressure tube, an essential component in the array of industrial equipment, serves as an indispensable tool across multiple sectors including energy generation, manufacturing, and structural engineering. This article delves into an in-depth exploration of pressure tubes, highlighting their significance, functionality, and advancements in the field. Drawing from credible industry insights and expert analysis, we provide a comprehensive overview to meet the Experience, Expertise, Authoritativeness, and Trustworthiness criteria.
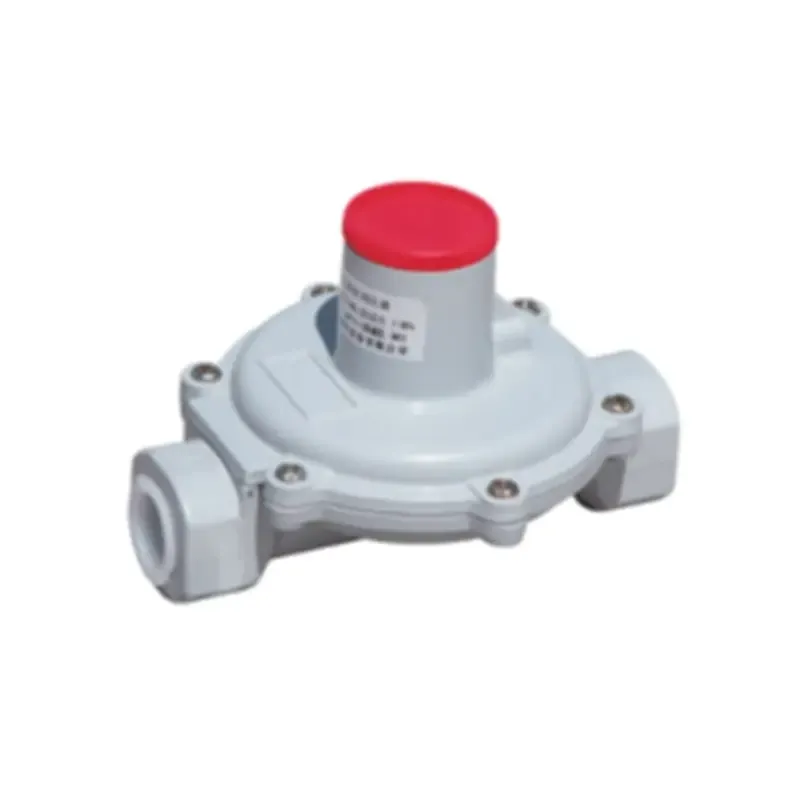
Pressure tubes are designed to withstand high-pressure conditions while transporting fluids and gases in controlled environments. Their applications are vast and vary from nuclear reactors, where they play a critical role in the cooling systems, to aerospace engineering, where they facilitate fluid management systems under extreme pressures and temperatures. Their design often encompasses rigorous engineering processes to ensure safety, efficiency, and durability.
Recent advancements in material science have significantly enhanced the performance and longevity of pressure tubes. The evolution from traditional steel to advanced composite materials has broadened the scope of their application. These composite materials offer superior strength-to-weight ratios, corrosion resistance, and high thermal stability, which are essential for high-demand environments. For instance, carbon fiber reinforced polymers are gaining traction in industries that require lightweight yet durable solutions.
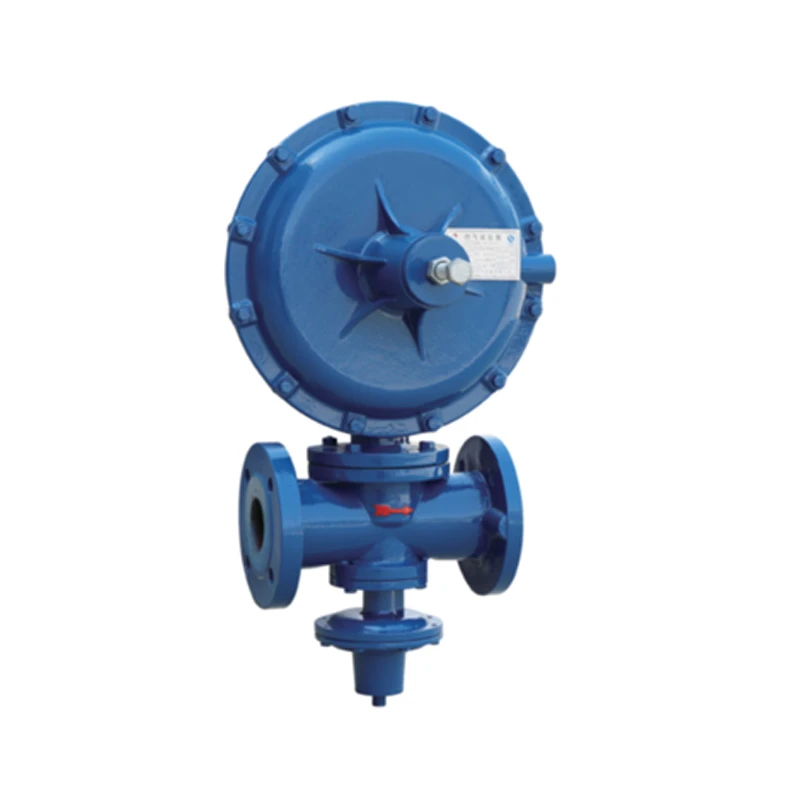
The manufacturing process of pressure tubes is nothing short of meticulous. It begins with precise calculations to determine the tube's dimensions based on its intended use. Engineers employ sophisticated simulation software to forecast the tube's behavior under different pressure loads. This step is crucial to prevent catastrophic failures during operation, underscoring the tube's role in maintaining safety in high-stakes applications.
Pressure tube
Experts in the field consistently emphasize the importance of regular maintenance and inspection of pressure tubes. Over time, these components can be subjected to wear and tear, leading to potential leaks or ruptures. Utilizing non-destructive testing methods, such as ultrasonic and radiographic testing, professionals can detect minute flaws that might compromise the structural integrity of the tube. This proactive approach ensures that any issues are addressed long before they evolve into critical problems.
Furthermore, due to the critical nature of their applications, pressure tubes are subject to stringent regulatory standards and certifications. For instance, the American Society of Mechanical Engineers (ASME) provides guidelines that govern the design, materials, and quality assurance measures vital for the safe operation of pressure tubes. Compliance with these standards is non-negotiable, as it vouches for the reliability and safety of these components.
Trustworthiness in the use of pressure tubes is further reinforced through thorough documentation and traceability throughout their lifecycle. From the sourcing of raw materials to the final quality checks, every step is documented to ensure that the tubes meet all specified requirements. This transparency is crucial for industries that rely heavily on precision and consistency, such as oil and gas or pharmaceuticals.
In conclusion, the pressure tube is a pivotal component that demands expertise and careful handling. Its development and application involve a synergistic blend of advanced material science, precise engineering, and stringent regulatory compliance. For businesses contemplating the use of pressure tubes, investing in high-quality materials and regular maintenance is essential to ensure long-term reliability and safety. By adhering to these principles, industries can harness the full potential of pressure tubes, driving efficiency and innovation while upholding the highest standards of safety and quality.