The natural gas pressure reducing valve is a paramount component in the efficient operation of gas systems, ensuring the safe and stable flow of gas from high-pressure pipelines to household or industrial units. As energy demands burgeon globally, the expertise surrounding these valves amplifies, optimizing performance while embracing standardized safety protocols.
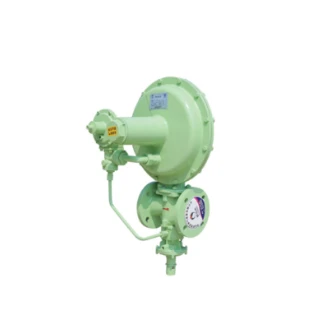
Gas systems everywhere depend fervently on the precision of pressure reducing valves. Crafted meticulously from robust alloys, these valves function by adjusting the high incoming pressure to a lower, more manageable level. Their design not only upholds system integrity but also ensures longevity and resilience against wear and tear, which is common in dynamic energy systems.
Professionals seasoned in the energy sector often stress the importance of choosing the right valve not merely by cost but by its specific application, pressure range, and capacity to withstand environmental conditions. This expertise forms a bedrock of decision-making, leading to enhanced operational efficiency and safety compliance.
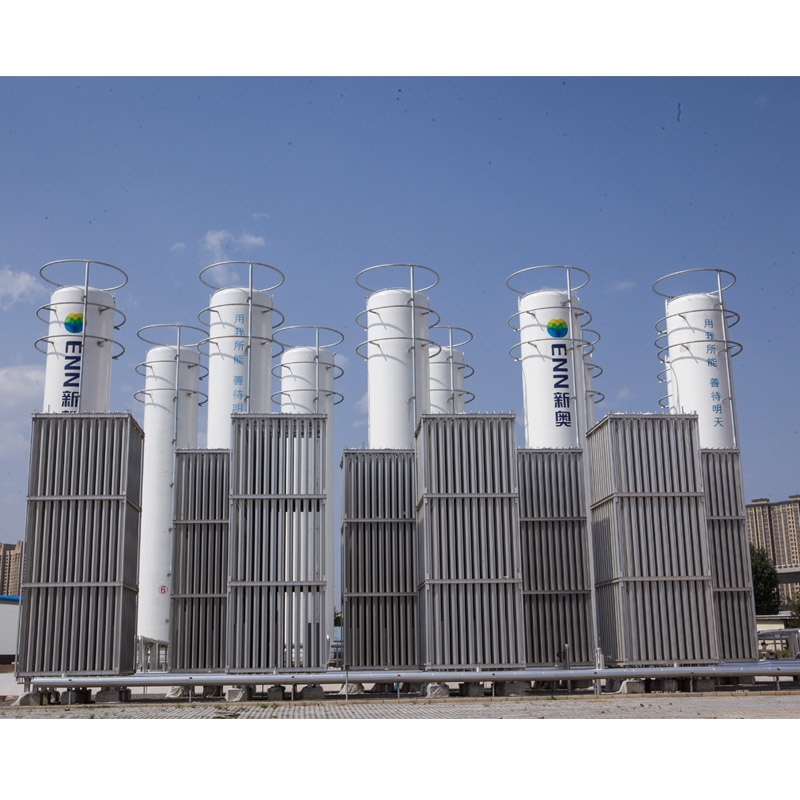
To illuminate the subject of natural gas pressure reducing valves, real-world experience dictates that installation and regular maintenance are critical. Proper installation not only involves checking the fit and alignment but also ensuring compatibility with existing systems and regulatory conformity. Experience shows that even a minuscule error in installation can lead to pressure drops, leaks, or complete system failure.
Once installed, these valves require consistent maintenance checks, which include inspecting the diaphragm and spring, ensuring there are no blockages, and that seals remain intact. From an expertise standpoint, field experts affirm that preventive maintenance diminishes downtime and extends equipment lifespan, a critical factor in industrial settings where gas supply continuity is crucial.
Natural gas pressure relief valve
Furthermore, authoritative guidelines from industry bodies set a standard of excellence for these valves. Compliance with international standards like ASME or ISO not only catalyzes trust but also legitimizes the use of specific valves in critical applications. Such standards generally cover aspects like maximum pressure capacity, temperature thresholds, and material specifications, essential for high-stakes projects.
Addressing the trustworthiness of pressure reducing valves necessitates a discussion on their fail-safe mechanisms and redundancy features. Leading manufacturers integrate advanced tech such as real-time monitoring and feedback systems, permitting operators to receive live data on valve performance. Such features bolster trust as they allow for quick corrective actions, significantly minimizing risks associated with gas pressure anomalies.
Moreover, manufacturers constantly innovate to align with environmental considerations. By enhancing precision and minimizing leakages, modern pressure reducing valves contribute to reduced carbon footprints, resonating with global sustainability goals. This aspect not only advances eco-friendliness but also marks an esteem of reliability and future-forward thinking valued by conscientious industry stakeholders.
In conclusion, the natural gas pressure reducing valve is not merely a component but a cornerstone of gas system stability and efficiency. The intersection of experience, expertise, authority, and trust crafts a comprehensive understanding and robust implementation standards for these valves. As industries evolve, so do the specifications and expectations from these critical components, emphasizing the ongoing need for specialization in selecting and maintaining the optimal choice for varied applications.