Meta Explore the advantages and applications of condensing units in various industries. A comprehensive guide to selecting the best system for your needs.
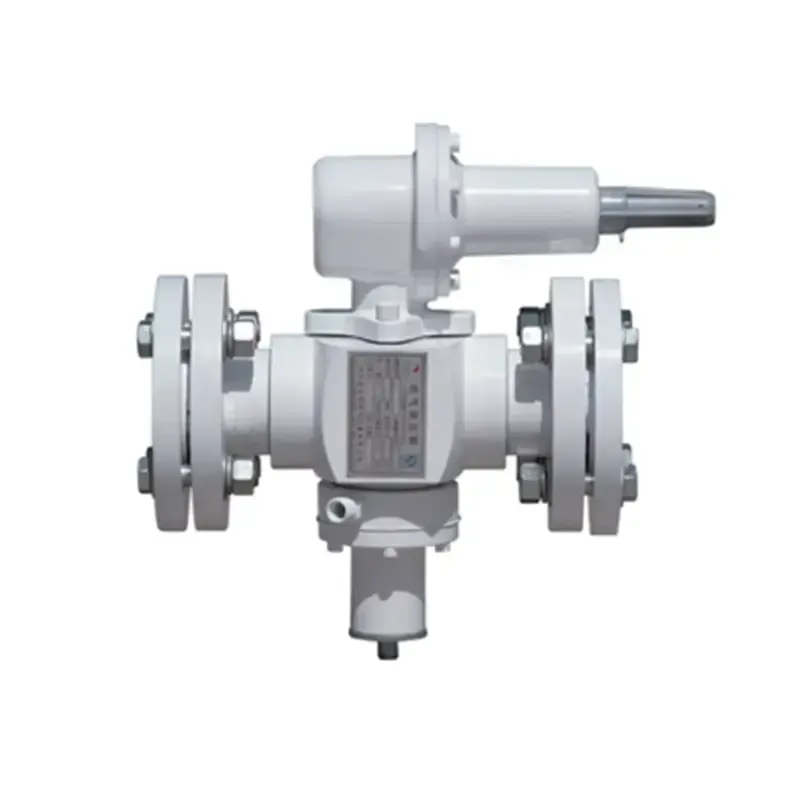
Condensing units, or مرشح التكثيف in Arabic, serve as the backbone of multiple industrial and commercial operations worldwide. They play a crucial role in refrigeration, air conditioning, and other HVAC systems, directly impacting energy efficiency and operational costs. This article explores their significance, offers insights for optimal selection, and highlights their applications across different sectors, focusing on their reliability, efficiency, and advancement.
Condensing units work as integral parts of a larger system aimed at heat rejection, a critical process ensuring that various facilities maintain optimal environments. Their ability to convert refrigerant gas back to liquid form by cooling it through atmospheric or forced-air systems epitomizes their primary function in HVAC frameworks. The diversity in their design caters to both high-end commercial refrigeration units and robust air conditioning systems.
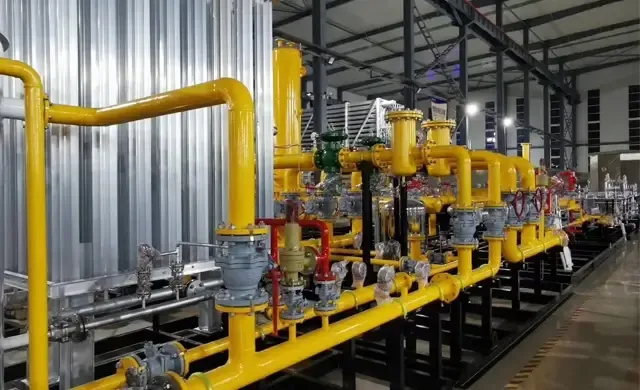
Experience speaks volumes when it comes to recognizing the impact of condensing units on overall system efficiency. In sectors such as food processing and storage, pharmaceutical manufacturing, and even retail businesses, these units ensure product integrity by maintaining necessary temperatures. For example, cold storage facilities rely heavily on condensing units to keep perishable items fresh, thereby extending shelf life and reducing waste.
From an expertise perspective, understanding the technical specs of condensing units is crucial. Two major factors dictate the best choice cooling capacity and energy efficiency. Cooling capacity ensures that the chosen model can handle the temperature demands of your establishment. Meanwhile, energy efficiency, often measured through coefficients like Energy Efficiency Ratio (EER) or Seasonal Energy Efficiency Ratio (SEER), highlights how effectively a system converts power into cooling output.
Selecting the right condensing unit involves weighing critical criteria, such as compressor type, coil material, and fan design.
Each component contributes to the overall performance and durability of the system. A screw compressor might be ideal for industrial applications requiring robust operational capacities, whereas a scroll compressor suits commercial entities due to its compact design and quieter operation. Coil materials like copper offer excellent thermal conductivity, while aluminum is cost-effective and contributes to lighter design structures.
Condensation filter
Authoritativeness in the industry often comes from manufacturers who have honed their expertise over decades, offering products that boast innovation and reliability. Brands that integrate smart technology into their systems allow users to remotely monitor and adjust system performance, aligning with energy-saving goals and predictive maintenance needs. Such technological integration not only enhances operational ease but also prolongs the lifespan of the unit through proactive management.
Trustworthiness is paramount, especially when condensing units are tasked with critical functions like cooling server rooms or medical facilities where environmental control is non-negotiable. The assurance of reliability often stems from rigorous testing protocols that products undergo before market launch. It's imperative that these units are certified by recognized international standards, such as ISO or AHRI, ensuring that performance matches the demands of real-world applications.
Innovation continues to shape the future of condensing units. Modern models are increasingly aligned with environmental laws and sustainability goals. The shift towards low Global Warming Potential (GWP) refrigerants signifies the industry's commitment to reducing ecological impact. Furthermore, developments in variable speed technology enable units to modulate performance based on extraction needs, leading to lower energy consumption and reduced operational expenses.
Choosing the ideal condensing unit is not merely about finding a product that fits spatial constraints or budget. It involves a comprehensive analysis of the application's needs, the system's performance metrics, and future scalability options. Ensuring a match between unit capabilities and facility requirements will not only enhance operational efficiency but also deliver a substantial return on investment.
In summary, the importance of condensing units in numerous industries cannot be overstated. Their reliability, backed by ongoing technological advancements and adherence to regulatory standards, underscores their indispensable role in maintaining processes that depend heavily on precise temperature control. Professionals seeking optimal solutions must stay informed about industry trends, integrating cutting-edge technology with practical experience to leverage these systems for maximum benefit.