Natural gas separation, a critical process in the energy sector, involves complex methods and technologies to purify and segregate valuable components from raw gas sources. This article delves into the intricacies of gas separation, unveiling insightful experience, expertise, and authoritative guidance to ensure trustworthiness in understanding this vital industry practice.
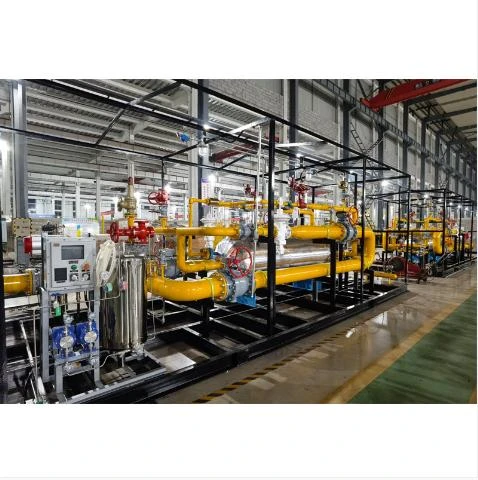
Gas separation technologies are primarily designed to extract methane and other valuable gases like ethane, propane, butane, and nitrogen from various gas mixtures. This separation is essential for achieving cleaner energy production and optimizing fuel quality for industrial applications.
Experience in the field of gas separation highlights the significant role of adsorption and membrane technologies. Adsorption processes leverage materials such as zeolites and activated carbon to selectively capture and release gas molecules. In membrane technologies, semi-permeable barriers allow certain molecules to pass while restricting others, creating an efficient separation mechanism. This expertise is underscored by continuous advancements in material science, which drive innovation in adsorbent materials and membrane designs, enhancing performance and reliability.
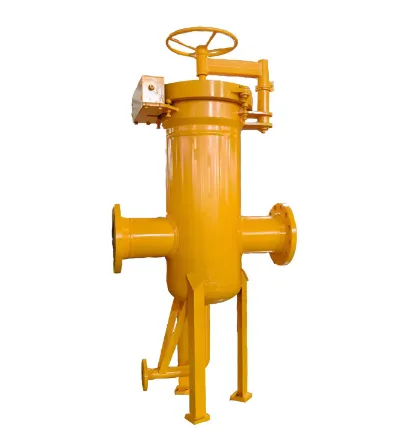
From an expertise standpoint, Pressure Swing Adsorption (PSA) and Cryogenic Distillation are two prominent methods utilized in gas separation. PSA uses variations in pressure to adsorb and desorb gases, making it ideal for hydrogen and methane purification. On the other hand, cryogenic distillation employs extremely low temperatures to liquefy and separate gases based on different boiling points. Despite their distinct mechanisms, both techniques require precise control and sophisticated equipment, substantiating the need for robust engineering and operational excellence.
Gas filtration
The authority surrounding gas separation is further affirmed by industry standards and regulatory frameworks that guide these processes. Organizations like the American Petroleum Institute (API) and the International Standards Organization (ISO) provide comprehensive guidelines to ensure safe, efficient, and environmentally responsible operations. These authoritative bodies conduct extensive research and disseminate knowledge that influences global practices, underscoring the significance of adhering to established protocols in gas separation processes.
Trustworthiness is at the core of gas separation technologies, particularly in ensuring safety, sustainability, and economic viability. Engineers and technologists are continually developing eco-friendly methodologies and leveraging automation and digitalization to enhance operational transparency and precision. Additionally, stringent safety measures are paramount to prevent hazards associated with high-pressure systems and volatile substances, reinforcing the commitment to protecting both the environment and human life.
Product innovation in gas separation is also driving the industry forward. Companies are investing heavily in research and development to create more efficient, cost-effective, and scalable solutions. Novel technologies such as hybrid systems that combine adsorption and membrane techniques offer promising improvements in separation efficiency and energy consumption. These innovations reflect the industry's dedication to providing comprehensive solutions that meet the evolving demands of energy markets while minimizing environmental impact.
In summary, gas separation processes hold a fundamental position in the energy value chain, demanding a balance of experience, expertise, authority, and trustworthiness. Companies and professionals in this field are continually advancing technologies to refine operations, comply with standards, and ultimately contribute to a sustainable energy future. By leveraging cutting-edge materials, methodologies, and regulatory insights, the industry can navigate the complexities of gas separation, yielding products that not only meet energy needs but also align with global sustainability goals.