Heat exchangers are critical components in numerous industrial applications, ensuring efficient thermal energy transfer between different fluids. With various designs and materials, understanding the intricacies of heat exchangers can significantly enhance both operational efficiency and lifespan, making them indispensable in sectors like chemical processing, power generation, and HVAC systems. Based on the fundamental principles of thermodynamics, heat exchangers improve energy efficiency and sustainability across various industries.
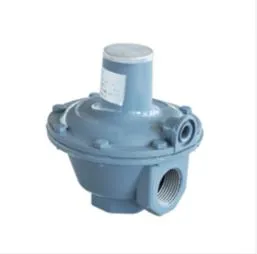
In a typical heat exchanger, fluids are separated by a solid wall to prevent mixing while allowing thermal energy transfer. The choice of materials is crucial, with metals such as copper, aluminum, or stainless steel commonly used due to their excellent thermal conductivity and corrosion resistance. Selecting the right material impacts both the performance and the durability of the equipment, aligning with industry standards and regulatory requirements.
There are several types of heat exchangers, each tailored for specific applications
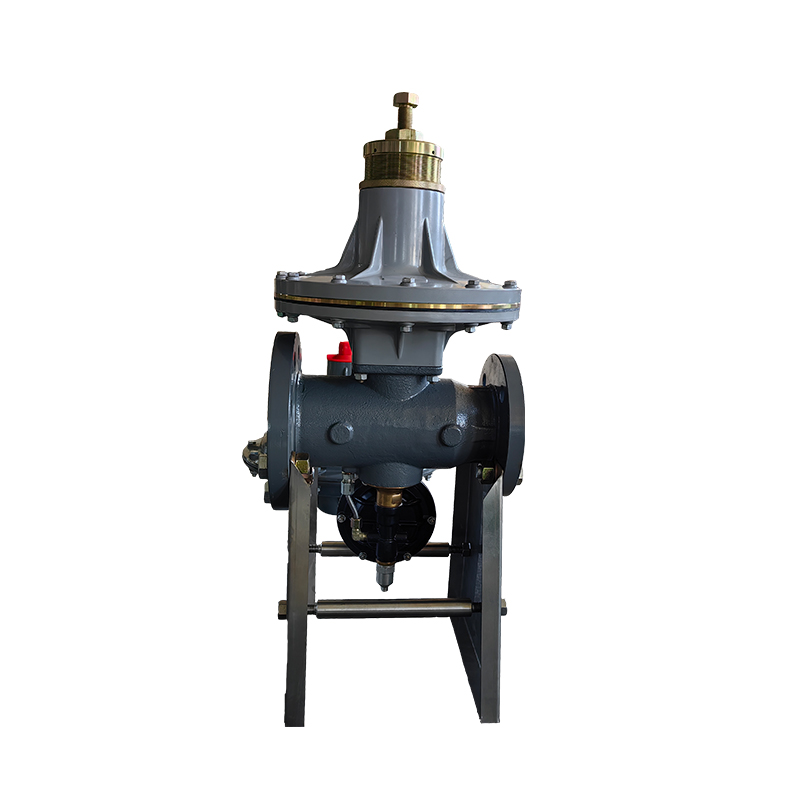
1. Shell and Tube Heat Exchangers Among the most common, they consist of a series of tubes packed within a shell. One fluid runs through the tubes, while another flows over the tubes in the shell. This design is highly adaptable, offering high-pressure and temperature handling capabilities, making it ideal for chemical and petrochemical industries.
2. Plate Heat Exchangers Comprising several thin, slightly separated plates that allow fluid flow, plate heat exchangers offer a compact design with a high heat transfer rate. Their modular structure ensures easy maintenance and cleaning, commonly used in food processing and small-scale HVAC applications.
3. Air Cooled Heat Exchangers Utilizing the ambient air to cool process fluids, these exchangers eliminate the need for water-cooling, thus reducing operational costs and environmental impact. They are extensively used in energy sectors, especially in remote or arid locations.
Heat exchanger
4. Finned Tube Heat Exchangers Equipped with fins attached to tubes, they enhance the heat transfer area, improving efficiency in applications like air conditioning and refrigeration systems. The finned design maximizes heat exchange between air and fluids, ensuring robust performance even in compact spaces.
Optimizing the performance of a heat exchanger necessitates a comprehensive understanding of flow dynamics, pressure drops, and temperature gradients. Computational fluid dynamics (CFD) simulations have become pivotal, allowing engineers to visualize and predict fluid flow patterns, enhance heat transfer efficacy, and identify potential operational bottlenecks. Such simulations enable precision in design, ensuring systems meet specific operational criteria while maximizing energy savings.
Regular maintenance is paramount to ensuring the longevity and efficiency of heat exchangers. Fouling, a common issue where deposits form on heat exchange surfaces, can impede performance, leading to increased pressure drops and reduced thermal efficiency. Implementing a routine cleaning schedule and employing anti-fouling techniques such as chemical cleaning or backwashing are essential to maintaining operational integrity.
Emerging technologies and materials are continuously transforming heat exchanger design and application. Advances like smart sensors and IoT integration provide real-time monitoring and analytics, enhancing predictive maintenance capabilities and operational optimization. Innovations in material science, including the development of advanced composites and alloys, present opportunities for improved heat resistance and reduced maintenance requirements, driving industry-wide efficiency gains.
Selecting the right heat exchanger involves considering factors like fluid properties, operating temperatures, pressure levels, and spatial constraints. Engineers and decision-makers must balance these factors with economic considerations such as initial investment, maintenance costs, and energy efficiency. The continued evolution of heat exchanger technology promises to address these complex demands, shaping the future of energy transfer solutions.
Understanding and leveraging the capabilities of heat exchangers can lead to significant benefits, including reduced operational costs, enhanced system reliability, and improved environmental outcomes. As industries seek to optimize energy use and reduce carbon footprints, heat exchangers will remain at the forefront of sustainable industrial practices.