Valve shut-off technology serves as a pivotal component in various industrial applications, offering precise control over fluid and gas flow in systems ranging from simple plumbing to complex oil and gas pipelines. This indispensable tool has evolved significantly over the years, being central to enhancing operational safety, reliability, and efficiency.
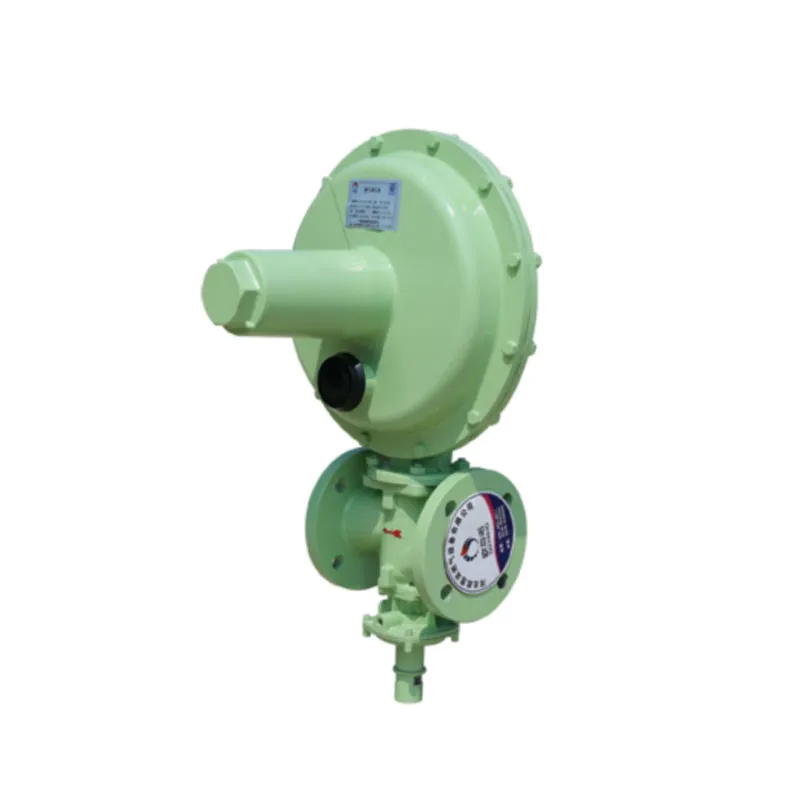
High-quality shut-off valves come in various forms, including gate valves, ball valves, and butterfly valves, each bringing unique advantages tailored to specific industrial needs. Gate valves, for instance, are renowned for their ability to provide an unobstructed path, making them ideal for situations where pressure loss is a concern. Meanwhile, ball valves are celebrated for their durability and excellent shut-off capabilities, making them a top choice in situations requiring minimal leakage. Butterfly valves, compact and lightweight, offer quick shut-off times, making them favorable in large-scale applications where speed is essential.
Incorporating shut-off valves into a system begins with an appreciation of their construction and function. The design typically involves a lever, knob, or wheel handle that, when engaged, manipulates an internal mechanism capable of halting the passage of material within the piping system. Material choice in valve construction ranges from metals like stainless steel and brass to robust plastics, a selection determined by the fluid type and operational temperatures expected.
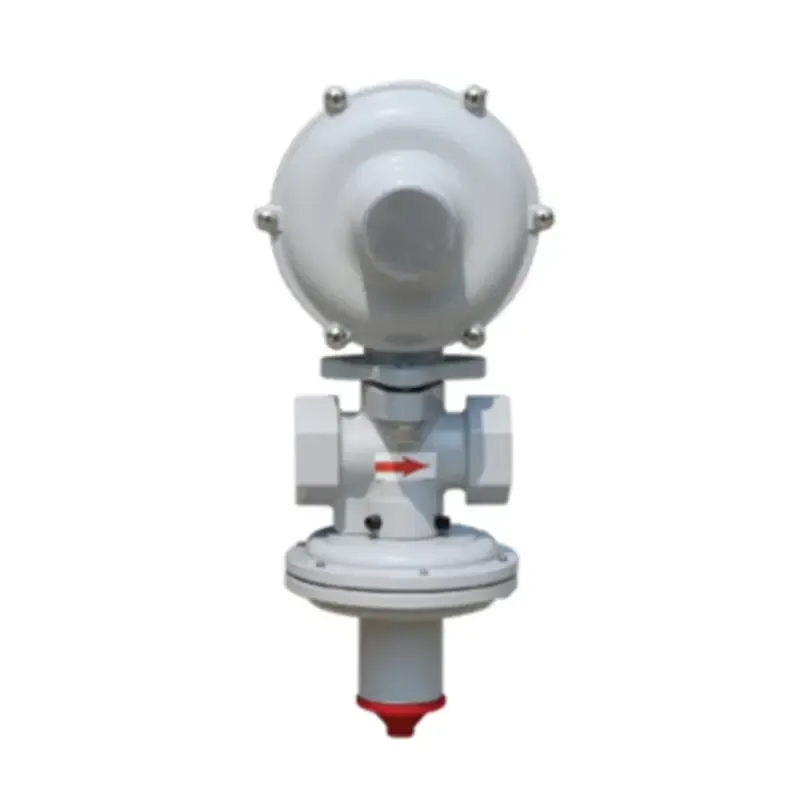
Authentic expertise in valve technology fundamentally revolves around understanding application-specific requirements. Engineers and technicians must possess a deep knowledge of the fluid characteristics — viscosity, temperature, and potential for corrosiveness — to select an appropriate valve. Such expertise is backed not just by theoretical knowledge, but also by practical exposure to field installations where real-world challenges such as thermal expansion or mechanical vibrations can impact valve performance.
Authoritativeness in valve shut-off technology is exemplified by adhering to globally recognized standards set by bodies such as the American Petroleum Institute (API) and the International Organization for Standardization (ISO). Certification from these entities not only enhances a manufacturer’s credibility but also assures end-users of the product's quality and reliability under stringent operational conditions.
Shut-off valve
A proactively maintained history of successful installations and collaborations with leading industry players significantly boosts a manufacturer's reputation. Case studies highlighting problem-solving instances, where innovative valve solutions have drastically reduced operational downtimes, offer substantial evidence of a brand’s authority in the market.
Building trustworthiness is pivotal to the sustained success of a valve manufacturer. Transparency in manufacturing processes, a robust quality assurance framework, and a commitment to continuous improvement through research and development speak volumes about a company's dedication to quality. Providing comprehensive customer support, from system design consultation to post-installation service, further reinforces customer confidence.
A successful example of integrating reliable shut-off valves includes the recent upgrade in a Southeast Asian oil refinery. The facility, grappling with frequent maintenance shutdowns due to outdated valve technology, saw a transformative decrease in unplanned downtimes post the adoption of cutting-edge ball valves engineered for high pressure and temperature resilience. This strategic move was underscored by rigorous field testing and real-time monitoring, which established the new system's dependability.
Promising advancements in materials science and smart technology herald the future of valve shut-offs. Self-diagnostic valves capable of live data transmission concerning system health and performance are revolutionizing maintenance approaches. These intelligent systems promise predictive maintenance, wherein potential issues are identified before causing significant disruptions, thereby safeguarding production continuity and cost-effectiveness.
In conclusion, valve shut-off technology stands at the forefront of innovation in fluid control systems. Those aiming to lead the market must prioritize not just cutting-edge product development, but also reliability, standard compliance, and robust service architectures. By cultivating trust and expertise, they build a reputation that not only attracts but retains discerning clientele seeking uncompromising quality and performance in their operational infrastructures.