Pressure tubes play a pivotal role in various industrial applications, encompassing the fields of energy, engineering, and fluid dynamics. Their critical function in maintaining and controlling pressure in systems requires thorough understanding and expertise to ensure optimal performance and safety. This article delves into the nuanced experiences and expert insights about pressure tubes that make them indispensable in the world of technology and industry.
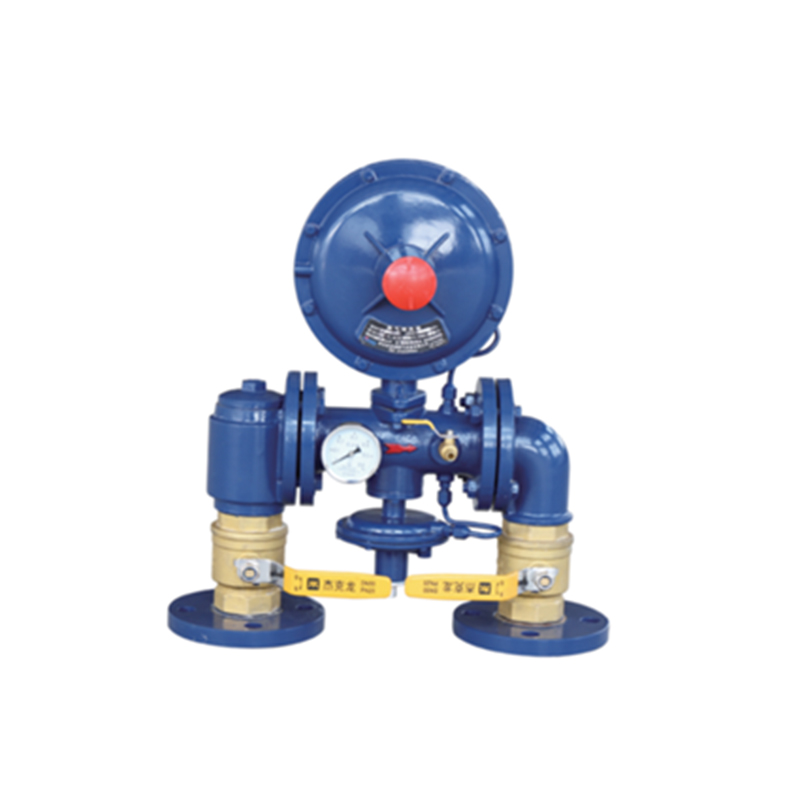
Pressure tubes are commonly utilized in systems where fluid, gas, or steam needs to be transmitted under high pressure. For instance, in nuclear reactors, pressure tubes are essential for the reactor's cooling system, where they safely transport pressurized coolant. The materials used in these tubes, typically stainless steel or zirconium alloys, are chosen for their ability to withstand extreme temperatures and pressures, ensuring the integrity of the system.
One of the significant experiences shared by professionals in the field involves the meticulous process of selecting the right pressure tube. This involves considering factors such as the tube's tensile strength, corrosion resistance, and thermal conductivity. For applications involving corrosive fluids, tubes may require additional protective coatings or linings to extend their lifespan and maintain functionality.
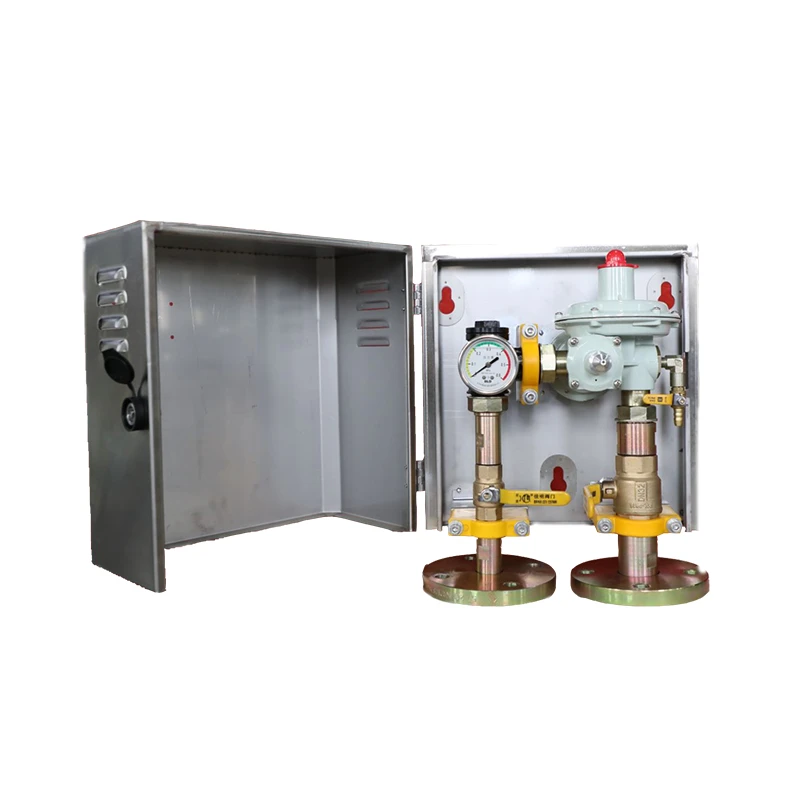
Professionals stress the importance of regular maintenance and inspection to avoid potential failures. Non-destructive testing methods like ultrasonic testing and radiographic examinations are commonly employed to spot any imperfections or signs of wear. These techniques are critical, as undetected issues can lead to catastrophic failures, making consistent monitoring a non-negotiable aspect of pressure tube management.
Pressure tube
Expertise in the field also extends to the design and engineering of pressure tubes. Engineers must account for variables such as pressure fluctuations, temperature variations, and environmental conditions. Utilizing advanced simulation software allows engineers to predict the behavior of pressure tubes under different scenarios, enabling the design of more resilient and efficient systems.
Authoritative voices in the industry often provide best practice guidelines and standards that manufacturers and engineers must adhere to. Organizations like the American Society of Mechanical Engineers (ASME) set forth stringent codes and standards that govern the design, fabrication, and testing of pressure tubes. These regulations ensure that every pressure tube in operation meets the highest safety and performance standards, instilling trust within industries that heavily rely on this technology.
Trustworthiness in the context of pressure tubes not only lies in the product's reliability but also in the transparency of the manufacturing process. Leading manufacturers often offer detailed reports and traceability records for each batch of tubes produced, providing customers with assurance regarding the quality and origins of their products. This transparency is crucial for building long-lasting relationships with clients who depend heavily on the performance and safety of these components.
In conclusion, the journey of understanding, selecting, and maintaining pressure tubes is vast and requires a blend of practical experience, technical expertise, and adherence to authoritative guidelines. With industries constantly evolving, the development of new materials and technologies continues to push the boundaries of what pressure tubes can achieve. As professionals in this field continue to share their insights and innovations, the role of pressure tubes as fundamental components in high-pressure systems remains indisputable.