Understanding the Crucial Role of Basket Strainers in Industrial Applications
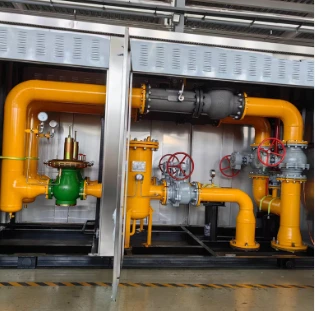
In the intricate world of industrial applications, efficiency and reliability are paramount. A key player in maintaining the seamless operation of various systems is the basket strainer, an often overlooked but vital component. This article delves into the intricacies of basket strainers, exploring their functionality, applications, and the expertise needed to select the right one for specific needs.
Basket strainers, as their name implies, are filtering devices designed to remove unwanted solids from liquids, gases, or steam. Their design typically consists of a perforated or wire mesh basket that acts as a sieve, capturing particles and allowing clean fluid to pass through. This seemingly simple mechanism is fundamental in preventing damage to downstream equipment, such as pumps, valves, and other process instruments. By trapping debris, basket strainers help avoid costly maintenance, downtime, and potential system failures.
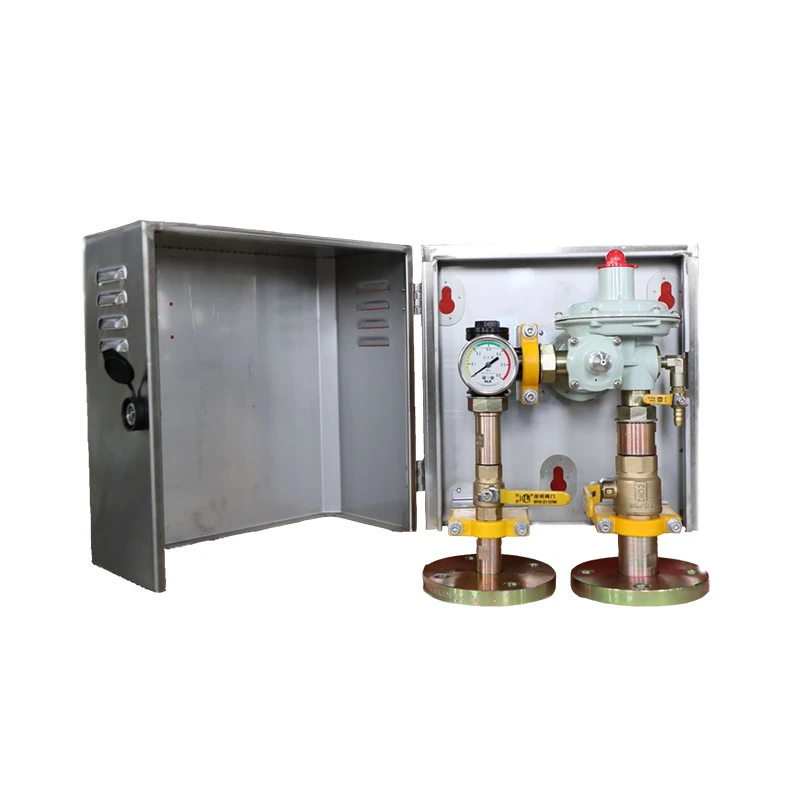
The advantages of using basket strainers extend beyond just protection. Their design allows for high flow rates with minimal pressure drop, making them suitable for applications requiring efficient filtering without compromising fluid dynamics. Industrial sectors such as oil and gas, water treatment, chemical processing, and food and beverage heavily rely on these devices to ensure continuous and safe operations. In oil refineries, for instance, basket strainers are employed to filter out contaminants in crude oil, safeguarding complex downstream processes. Similarly, in water treatment plants, they play a crucial role in removing sediment and particulate matter from water, enhancing the quality and safety of the supply.
Selecting the right basket strainer involves a deep understanding of several factors, including the type of fluid being processed, the size and nature of the contaminants, and the desired flow rate. Expertise in this area is crucial, as the wrong choice can lead to inefficiencies and even equipment failures. For example, a strainer with an inappropriate mesh size might allow harmful particles to pass through, or a material incompatible with the fluid could lead to corrosion and breakdown.
basket strainers
Material selection is another critical aspect of choosing a basket strainer. Common materials include stainless steel, brass, and plastic, each having specific advantages depending on the application. Stainless steel is often favored for its durability and resistance to corrosion, making it ideal for harsh environments. Brass is commonly used in water applications due to its good corrosion resistance and machinability, while plastic is chosen for its lightweight and cost-effectiveness in less demanding conditions.
Regular maintenance and cleaning are essential to ensuring the longevity and effectiveness of basket strainers. Over time, accumulated debris can clog the mesh, reducing flow rates and increasing pressure drop across the system. Routinely inspecting and cleaning the baskets is necessary to maintain optimal performance. In industries where contamination must be minimized, having a second set of baskets on hand for quick swaps during cleaning can significantly reduce downtime and increase operational efficiency.
The authority of basket strainers in the industrial sector is well-established, but their importance is often underappreciated. Leveraging the expertise of experienced professionals for installation and maintenance can greatly enhance trust in these components. Collaborating with suppliers who can provide insights into the latest advancements and best practices related to basket strainers ensures that systems remain at the cutting edge of technology.
In conclusion, basket strainers are indispensable in a myriad of industrial applications, serving as silent sentinels that protect and enhance system operations. Their ability to filter out impurities while maintaining fluid integrity underscores their value. Understanding the nuances of their functionality and deploying the correct expertise to select and maintain these devices can lead to significant improvements in system reliability and cost savings. By prioritizing the role of basket strainers, industries can optimize their processes, ensuring safety, efficiency, and longevity in their operations.