Navigating the technical landscape of filtration systems often leads professionals to encounter the pivotal role of coalescing filters, a crucial component engineered to remove liquid aerosols and particles from gas flows. With their integration into numerous industrial settings, understanding their intricacies lends a competitive edge, underpinned by the four cardinal principles Experience, Expertise, Authoritativeness, and Trustworthiness.
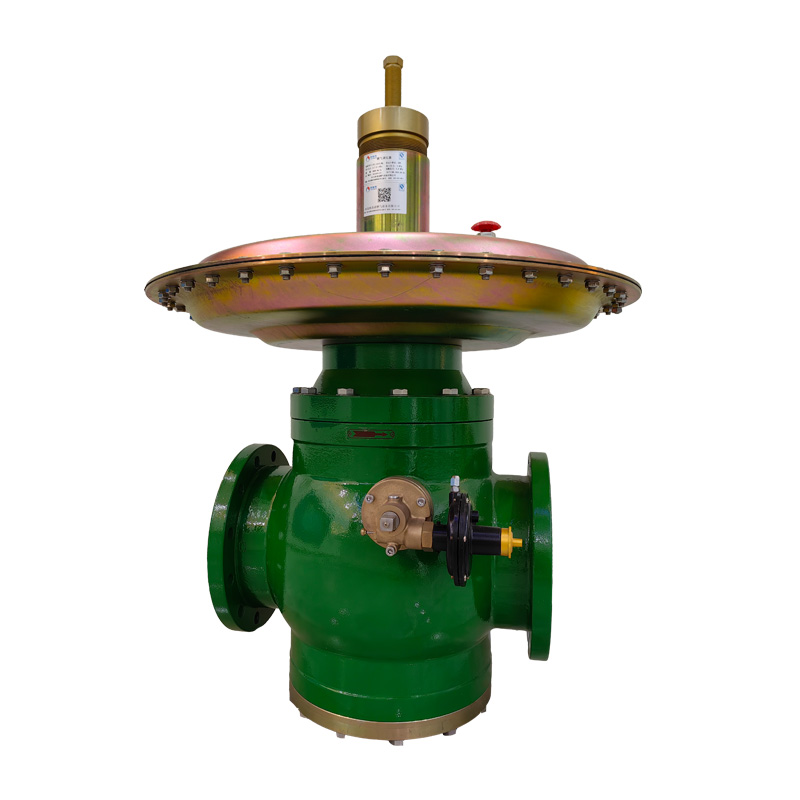
The burgeoning demand for highly efficient filtration systems has positioned coalescing filters at the forefront of innovation in sectors such as petrochemical industries, gas processing plants, and even the pharmaceutical realm.
With years of firsthand experience, industry veterans highlight the blend of simplicity and sophistication these filters embody. The process primarily involves two phases the initial interception where particles are trapped, followed by the coalescence phase, where tiny aerosol droplets merge into larger globules, subsequently drained away due to gravitational forces. This mechanism ensures a high degree of purity, fulfilling the stringent requirements of critical processes.
Expertise comes into play prominently when considering the materials and design variations that define coalescing filters. Engineers and product specialists note the significance of filter media selection, where factors such as fiber diameter, layer thickness, and porosity are meticulously calibrated. Glass fiber materials, alongside innovative synthetic alternatives, are renowned for their superior coalescing efficiency, offering low resistance and high dirt-holding capacity. Furthermore, there are ongoing advancements in nanotechnology, opening new frontiers in particle filtration and liquid aerosol management.
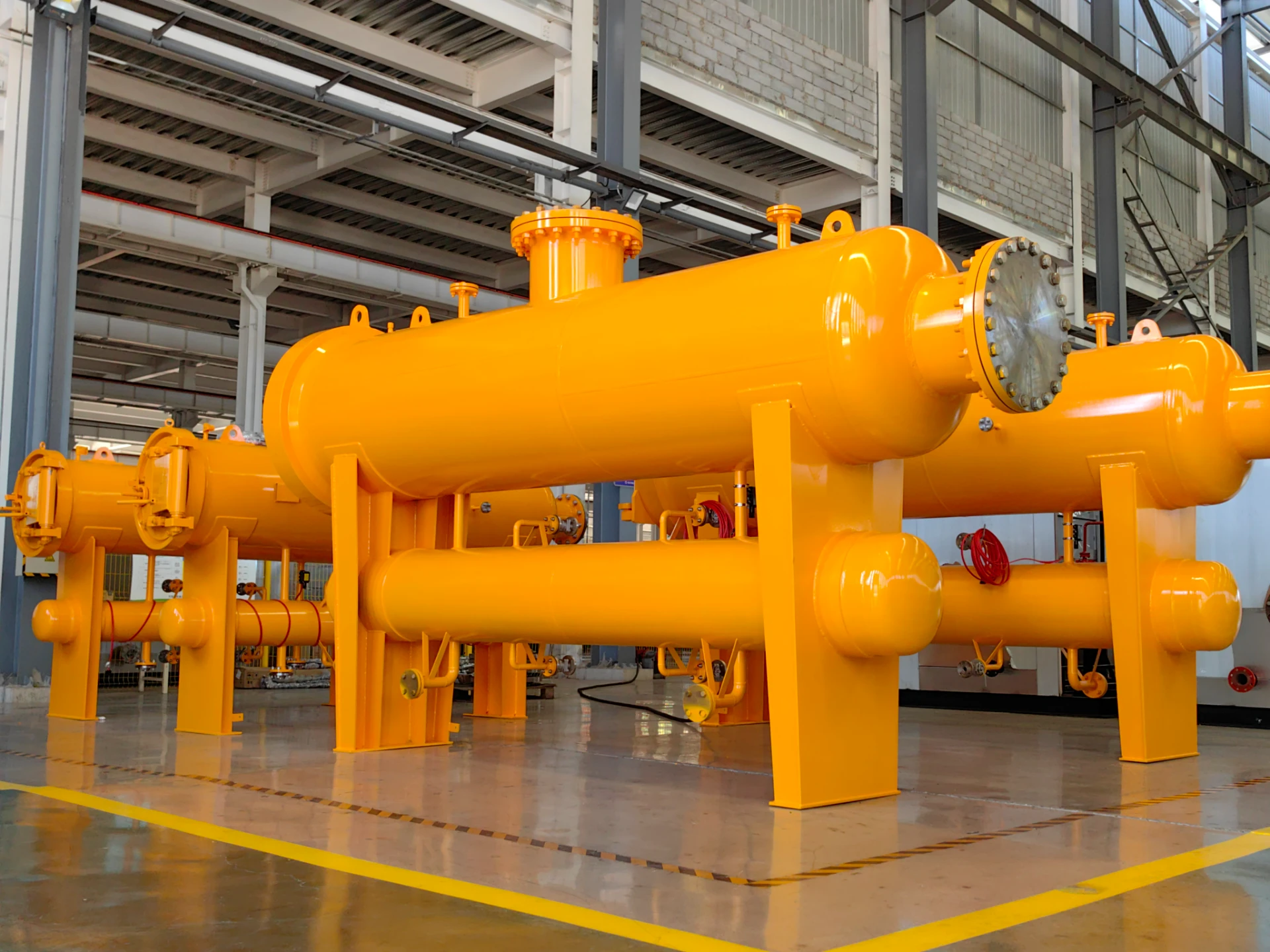
coalescing filter
Authoritativeness is underscored by the adoption of coalescing filters in compliance with global standards. Accredited bodies, such as the American Society of Mechanical Engineers (ASME) and the International Organization for Standardization (ISO), have recognized these filters' transformative impact. Such endorsements reassure stakeholders of their reliability and robustness across challenging conditions, including high temperature, pressure variances, and corrosive environments. These filters are pivotal in safeguarding equipment, minimizing the risk of contamination, and ensuring the continuity of seamless operations.
Trustworthiness is undeniably cemented through empirical insights and documented success stories from leading organizations. A substantial portfolio of field applications provides a solid foundation for the perceived reliability of coalescing filters. From enhancing the life span of compressors and turbines to ensuring consistent purity levels in gas distribution networks, the testimonials of improved operational efficiency and reduced maintenance costs speak volumes. Furthermore, customer feedback often emphasizes the marked reduction in downtime and enhanced productivity, reinforcing confidence in their use.
In conclusion, embracing coalescing filters goes beyond mere technical implementation; it involves a strategic foresight that aligns operational excellence with the latest filtration technologies. For businesses poised to innovate and optimize, these filters offer a credible solution underscored by comprehensive professional expertise and recognized authority models, with a proven track record ensuring not just compliance, but genuine advancement in filtration accuracy and reliability. As the industrial landscape evolves, the resonance of coalescing filters' effectiveness magnifies, carving pathways for more refined, economical, and environmentally sustainable practices.