Cyclone separators, often heralded as the unsung heroes of industrial air filtration, have gained significant attention for their efficiency and practicality in a vast array of applications. Their innovative design capitalizes on centrifugal forces to separate particulate matter from the air or fluid, effectively streamlining processes and improving air quality within industrial and manufacturing settings. This article delves into the experience and expertise surrounding cyclone separators, providing authoritative insight into their functionality and trustworthy performance.
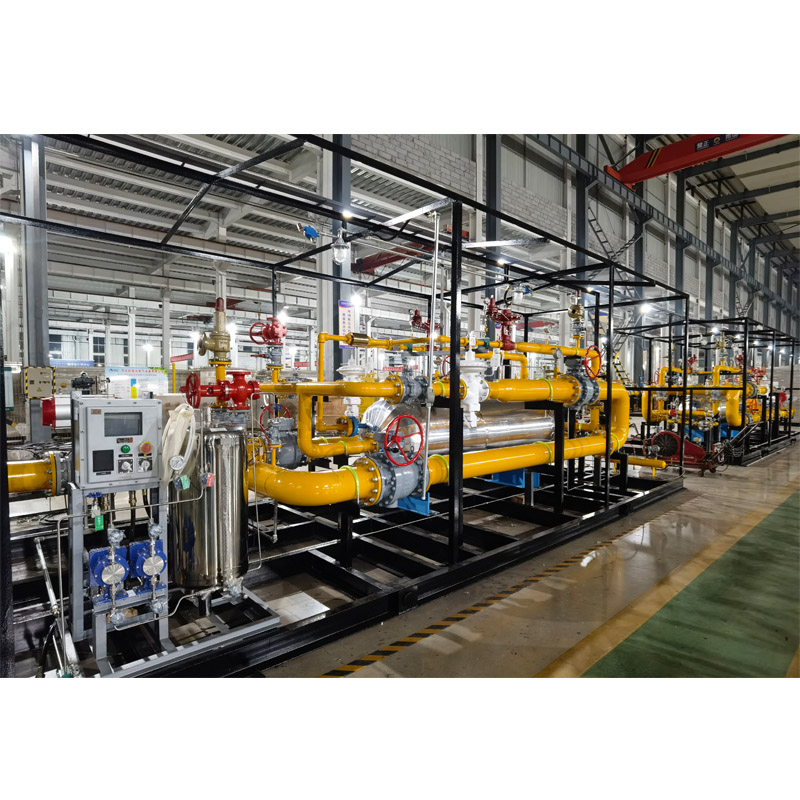
Cyclone separators utilize a sophisticated yet straightforward mechanism to perform their task. They consist of a chamber that induces a spiraling motion in the incoming air stream. As the air rotates, denser particles are flung toward the walls of the chamber due to centrifugal forces. These heavier contaminants then slide down into a collection area, while the cleaned air exits through a central outlet positioned at the top. This method does not require any filter media, making cyclone separators both low-maintenance and cost-effective.
From an expert perspective, the efficiency of a cyclone separator largely hinges on its design. Several factors—such as the shape and size of the cyclone, the velocity of the incoming air, and the characteristics of the particles being filtered—play pivotal roles. Engineers have continued to refine these designs, leading to variations like high-efficiency cyclones, which are adept at capturing smaller particulate matter, thus broadening their application scope. Additionally, modular designs are now emerging, allowing for customization based on specific industry needs, further underscoring their adaptability.
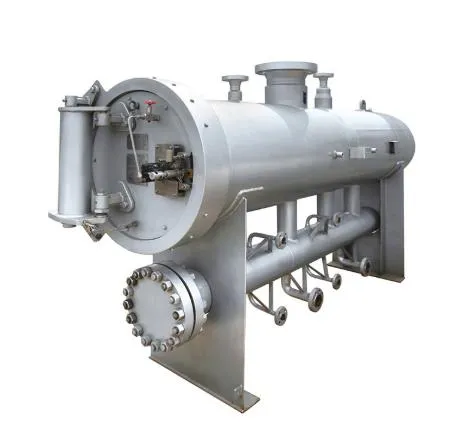
In real-world applications, cyclone separators shine in industries like cement, steel, and lumber, where dust and particulates are prolific. In cement manufacturing, for example, the ability of cyclone separators to handle large volumes of dust makes them indispensable. Professionals navigating these environments rely on cyclone separators not only for their dependable performance but also for compliance with stringent emission regulations. Their robustness in harsh industrial environments affirms their trustworthiness and solidifies their reputation as a reliable component of pollution control systems.
cyclone separator
The marketplace for cyclone separators is fiercely competitive, with manufacturers striving to embody trustworthiness by adhering to high-quality standards and providing comprehensive post-installation support. Companies that install cyclone separators typically offer extensive warranties and readily available support technicians, which reinforces customer confidence in their investment. Moreover, ongoing collaborations with research institutions have led to innovations that enhance separator capabilities, such as improved resistance to abrasion, which directly correlates with an extended operational lifespan.
To ensure authenticity in discussions about cyclone separators, it's vital to recognize their limitations. While exceedingly efficient at collecting larger particles, they may not be the optimal choice for environments where capturing ultrafine particles is crucial. Thus, they are often used in tandem with other filtration technologies, ensuring complete particulate control. This balanced approach showcases the integrity of their design while acknowledging their role as part of a more comprehensive filtration solution.
Cyclone separators continue to evolve, with sustainable development at the forefront. Modern iterations incorporate eco-friendly materials and energy-efficient designs, aligning with global trends towards sustainable industrial practices. The robust nature of cyclone separators, coupled with their simplicity and effectiveness, reinforces their enduring presence in the industrial landscape, embodying a synthesis of expertise, authority, and reliability.