Cyclone separators, often essential in industrial processes, play a crucial role in separating particles from fluids, typically air or gas streams, using vortex separation technology. As an expert in industrial equipment and air filtration technologies, understanding the fundamental principles, advantages, and recent innovations of cyclone separators can greatly benefit any related operation.
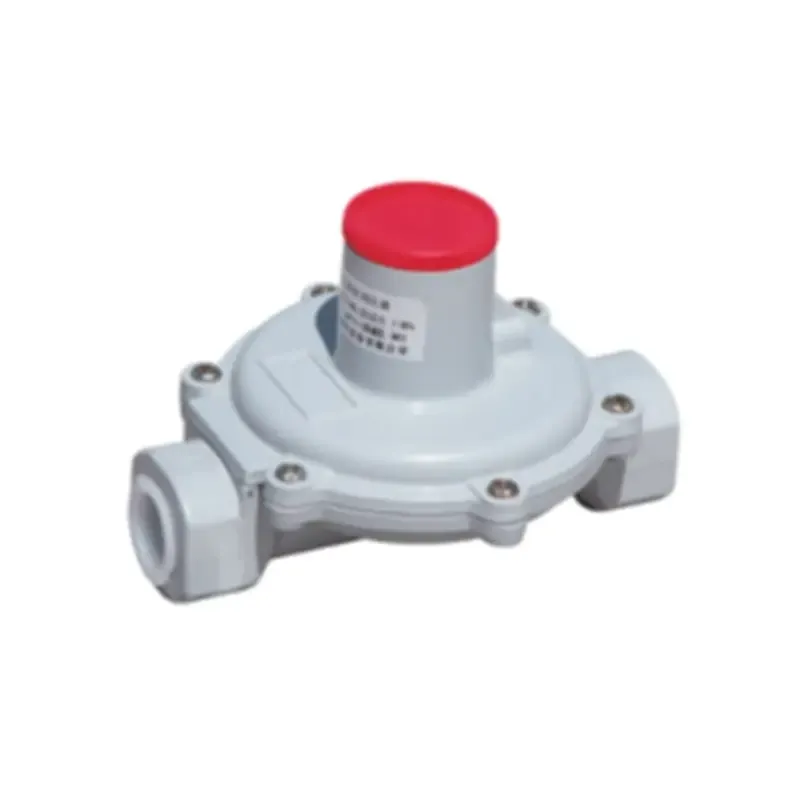
Cyclone separators leverage the principles of inertia and centrifugal force to effectuate particle separation from a gas stream. The fluid enters the cyclone separator tangentially at a high velocity, generating a spinning vortex. Heavier particles within the stream, due to their inertia, cannot follow the tight curve of the gas and are thrown to the cyclone's walls, where they lose their momentum and slide downwards into a collection chamber. Meanwhile, the clean air spirals upwards and exits through the top of the unit. This simple yet effective method enables industries to remove particulates from airstreams with high efficiency.
Industries, such as woodworking, metal processing, and manufacturing, rely heavily on cyclone separators because they offer a relatively low-cost, low-maintenance, and reliable method of air filtration. Products like dust and oil mist can be filtered effectively, safeguarding sensitive equipment and protecting worker health by ensuring air quality. Cyclone separators are especially valuable in processes where large volumes of gas and high loads of particulates are involved as they remain operational without requiring frequent maintenance shutdowns.
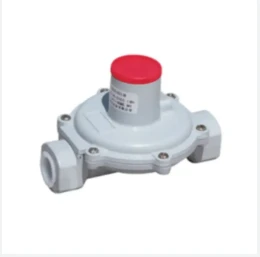
Advancements in cyclone separator technology focus on enhancing separation efficiency and reducing energy consumption. Efficiency is typically influenced by factors such as cyclone geometry, inlet velocity, and dust load. Innovative designs now incorporate elements like spiral inlet ducts and extended cone sections to improve particle removal efficacy. Furthermore, computational fluid dynamics (CFD) modeling is extensively used to optimize designs, ensuring the turbines are tailored for specific industrial applications and particle types.
cyclone separator
Material selection also plays a critical role in a cyclone separator's performance and durability. High-abrasion environments demand the use of wear-resistant materials, such as ceramics or hardened steel, to extend the lifespan of the separators significantly. Additionally, corrosion-prone processes require materials resistant to chemicals and moisture. By understanding these factors, industries can select cyclone separators that not only meet their performance needs but also offer longevity, thereby reducing long-term costs.
Trustworthiness and reliability in product selection are paramount. Manufacturers committed to quality often provide testing data, including particle size distribution analyses and flow rate charts, to aid consumers in making informed decisions. It's essential to collaborate with reputable suppliers who have a proven track record in delivering exceptional products and who can customize solutions based on specific industrial requirements.
In conclusion, cyclone separators represent a cornerstone technology in air and gas filtration for a diverse range of industries. Their ability to efficiently separate out particulates without the need for filtration elements makes them a robust choice. Continuous improvements in technology, focusing on enhancing performance and reducing energy demands, position cyclone separators as a forward-thinking solution in maintaining industrial plant efficiency. Engaging with trusted suppliers to access high-quality equipment further solidifies their reliability as a cleaning solution in the dynamic industrial landscape. As industries continue to evolve, so too will the cyclone separator, adapting to new challenges and remaining a vital component in industrial air purification systems.