The demand for electric valves has rapidly increased across diverse industries due to their precision, reliability, and advanced functionalities. As businesses and manufacturers shift towards more sustainable, efficient systems, understanding the depth of electric valves becomes essential for optimizing industrial processes.
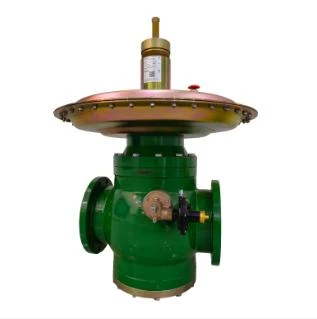
Electric valves are pivotal in controlling the flow of fluids in modern engineering systems, offering automated solutions that enhance operational efficiency. Unlike their manual counterparts, electric valves provide uncompromised automation in controlling liquids and gases, which is essential for complex infrastructure and high-precision requirements in industries such as oil and gas, water treatment, chemical plants, and HVAC systems.
One significant advantage of electric valves is their ability to integrate seamlessly with various control systems. They can connect with PLCs (Programmable Logic Controllers), BMS (Building Management Systems), and other advanced platforms, offering unprecedented control over operational processes. This integration not only streamlines operations but also facilitates real-time data monitoring, providing operators with critical insights into system performance and helping preemptively address issues before they escalate.
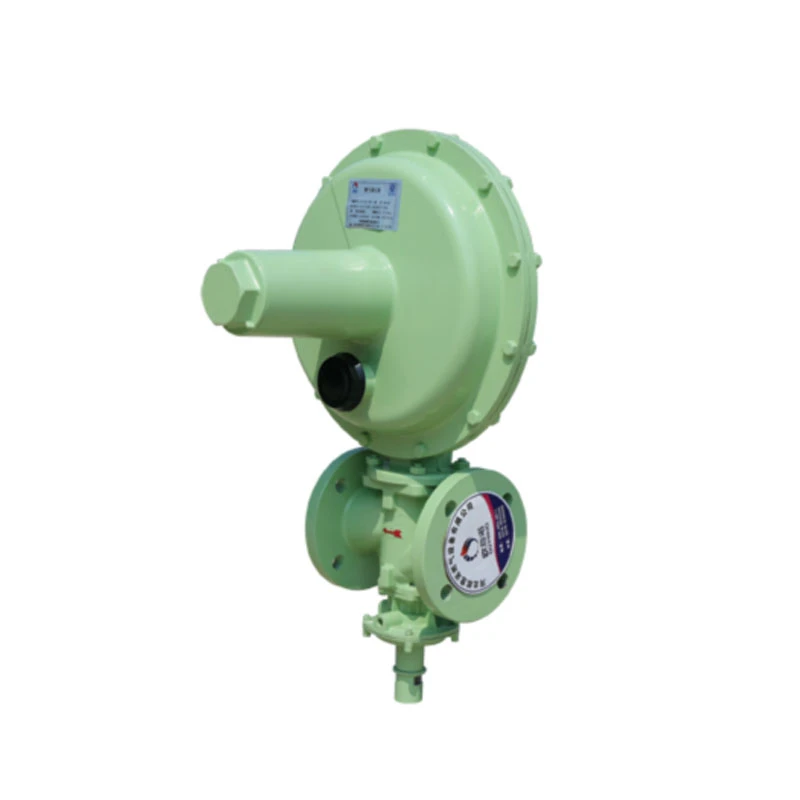
In terms of expertise, electric valve selection involves careful consideration of several factors fluid type, flow control needs, pressure and temperature conditions, and the specific application environment. For example, industries dealing with corrosive substances require valves made from durable materials like stainless steel or Teflon to withstand harsh conditions.
Expertise in material science becomes crucial here to determine the optimal choice for longevity and performance.
Further demonstrating their authority in engineering, electric valves come equipped with smart control features such as remote operation capabilities and diagnostic functions. This is particularly beneficial in hazardous or hard-to-reach environments where manual operation poses risks. By minimizing human intervention, electric valves not only enhance safety but also reduce potential downtimes and maintenance costs, a factor often highlighted by industry experts.
electric valve
Trustworthiness in electric valves is cemented by rigorous quality standards adhered to by reputable manufacturers. These standards ensure that every valve meets strict performance and reliability benchmarks, crucial for sectors where safety and precision are non-negotiable. ISO certifications and compliance with industry-specific regulations such as API and ANSI underscore a manufacturer’s commitment to quality and safety.
The true experience of utilizing electric valves is best reflected in case studies where industries have achieved remarkable improvements in efficiency and reduction in wastage. For instance, a water treatment facility implementing electric valves may see a substantial decrease in water loss due to precise control capabilities, leading to overall operational overhead reduction and better resource management.
Innovation in electric valve technology continues to evolve, with leading manufacturers investing in IoT-enabled solutions. These smart electric valves bring a new dimension of connectivity and adaptability, allowing for predictive maintenance, real-time analytics, and enhanced customization according to specific operational demands. This progression not only emphasizes the valve’s role in modern industrial IoT landscapes but also highlights the ongoing commitment to meeting tomorrow’s challenges today.
Ultimately, the decision to incorporate electric valves in any system architecture should be based on holistic assessment by knowledgeable professionals who understand both the technical and strategic objectives of the operation. Whether through enhancement of existing systems or the integration into new projects, electric valves represent a critical component in the pursuit of efficiency, safety, and modernity in industrial applications.