Filter separators are an integral component in various industrial applications, contributing not just to operational efficiency but also to the durability and safety of the machinery involved. These devices are primarily employed to remove solid or liquid contaminants from gas streams, making them indispensable across different sectors, including oil and gas, chemical manufacturing, and power generation.
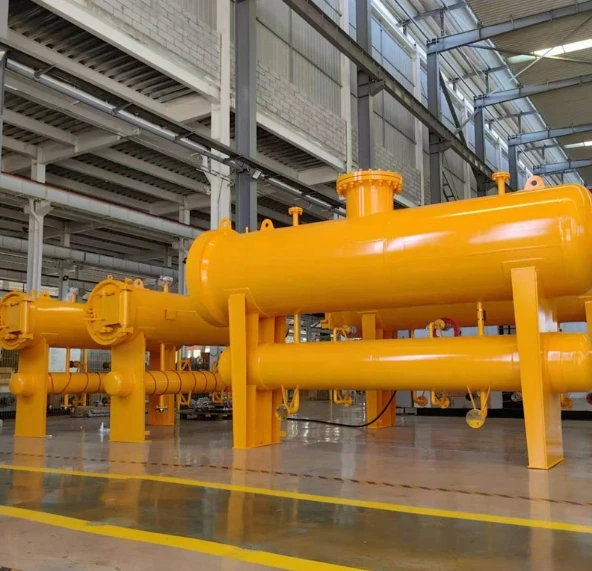
A crucial aspect of filter separators is their design, which usually involves a two-stage process. The first stage often consists of a centrifugal element or an impingement device that removes larger particulates through mechanical means. This step is vital for protecting the delicate filtering mediums in the subsequent stage, which is typically composed of a coalescing filter element that captures finer particles. This dual-action mechanism ensures that the output is impeccably clean, safeguarding downstream equipment from potential damage and ensuring it operates at peak efficiency.
In industries such as oil and gas, the stakes are exceptionally high; even a minor contamination can result in substantial economic losses and safety hazards. Filter separators excel here by ensuring that the natural gas reaching the final stages of processing is free from any particulate matter or liquid aerosols. This not only enhances combustion efficiency but also reduces the wear and tear on compressors and turbines. Ultimately, using a filter separator extensively curtails maintenance costs and minimizes the risk of unexpected downtime.
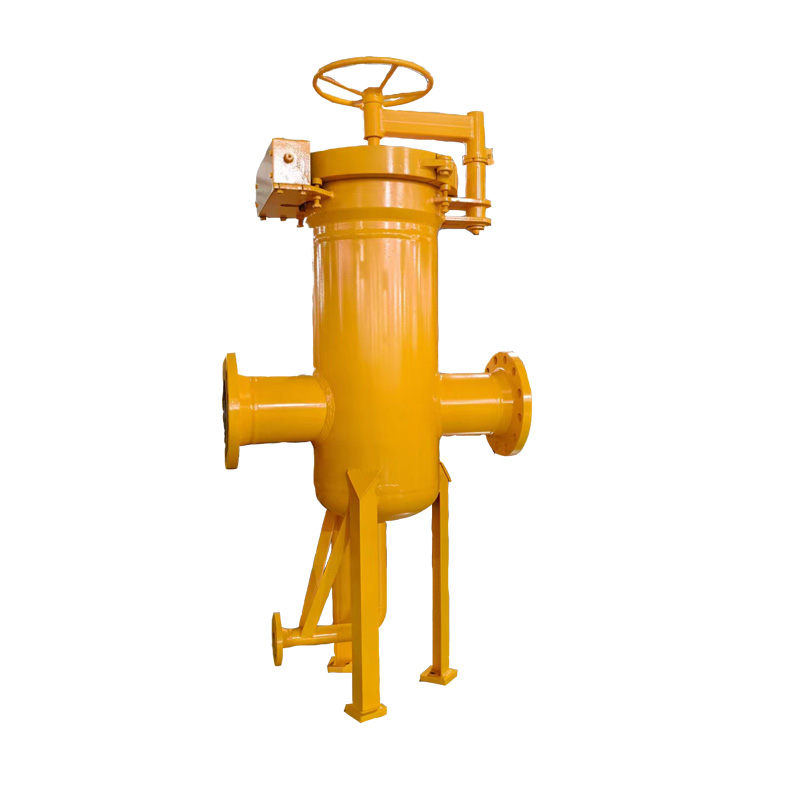
The efficacy of filter separators is further highlighted in the realm of chemical processing, where purity is paramount. In these scenarios, the quality of the final product can be significantly compromised by the slightest contamination. By incorporating high-performance filter separators, companies alleviate such risks, ensuring processes run smoothly and outcomes are consistent with stringent quality standards. The advanced materials and technology employed in modern filter separators make them exceptionally reliable, capable of functioning under high-pressure environments and handling a variety of chemicals without degrading.
filter separator
Trustworthiness and reliability are attributes that companies seek when investing in filter separators. Leading manufacturers often provide extensive data on the performance metrics of their products, including filtration efficiency, pressure drop, and capacity ratings, which are verified by industry-recognized standards. This transparency builds trust with industrial clients, ensuring that their investments are backed by reliable and authoritative information.
An additional consideration when choosing filter separators is their adaptability to different operational environments. Customizable options such as varying the materials of construction and the type of filter media can tailor a separator to specific needs, whether it’s dealing with high temperatures, corrosive environments, or varying pressure conditions.
The versatility of these separators makes them a staple investment for businesses aiming to maximize operational reliability and output quality.
Moreover, advancements in technology have led to the development of smart filter separators, which integrate diagnostic tools and sensors. These innovations allow for real-time monitoring of performance, providing valuable insights into pressure changes, contamination levels, and filter condition. This cutting-edge feature enables proactive maintenance strategies, reducing the risk of costly operational interruptions and extending the lifespan of both the separator and downstream equipment.
In conclusion, filter separators are not just an accessory but a linchpin in various industrial applications. The blend of their high efficiency, cost-saving potential, and reliability makes them an indispensable choice for industries focused on enhancing productivity and minimizing risks. Companies that prioritize these attributes can ensure successful long-term operations by integrating filter separators into their system design. Their role in protecting expensive machinery and ensuring the purity of processed materials underscores their value as a critical component in any industry’s operational strategy. As industries evolve, so too must the technologies that support them, and filter separators are a shining example of how innovation continues to drive performance and reliability forward.