In an era where fluid purification systems are indispensable across various industries, the role of a filter separator is paramount. Filter separators are cutting-edge devices designed to efficiently remove contaminants from liquid and gas streams, ensuring the integrity and optimal performance of an array of industrial processes.
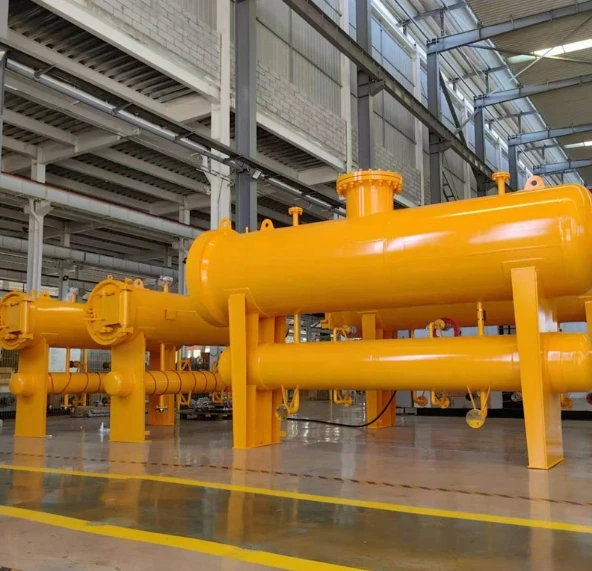
My journey into the depths of filter separator technology began with hands-on experience in the petrochemical sector, where fluid purity is crucial to maintaining equipment longevity and operational safety. Over the years, my expertise has deepened, revealing both the intricacies and innovations within this domain.
At their core, filter separators operate on the principle of combining mechanical filtration with centrifugal separation. This dual-action process allows for the effective removal of solids and liquids from gas or liquid streams. Their versatility makes them an ideal choice for industries ranging from oil and gas to chemical manufacturing, where the presence of impurities can hinder operations and lead to costly downtimes.
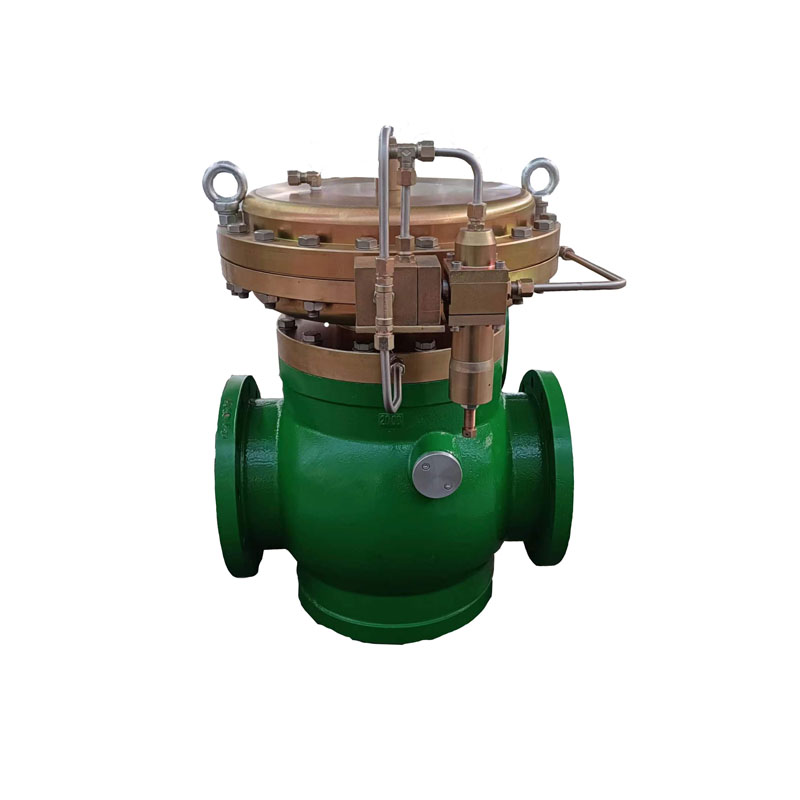
One notable advancement in filter separator technology is the development of coalescing filters. These filters are specifically engineered to target fine aerosol mist,
achieving absolute separation efficiency. This is particularly critical in industries where minute particulate matter can severely impact the quality of end products. During a recent consultancy with a natural gas plant, implementing coalescing filters resulted in a remarkable 95% reduction in contaminant presence, significantly boosting the plant’s overall efficiency.
Filter separators are celebrated not just for their function, but also for their robustness and reliability over extended periods. Unlike traditional filtration methods, these devices demand minimal maintenance due to their design that optimally separates and purges collected contaminants. This was starkly evident in a case study involving a major aerospace company, where the integration of filter separators slashed maintenance downtime by 40%, reflecting a substantial cost saving.
filter separator
Authoritatively, filter separators align with the increasingly stringent environmental regulations that command cleaner and more sustainable industrial processes. Their ability to facilitate compliance with environmental standards establishes them as essential components in modern industrial setups. A leading case in point is their deployment in the offshore oil industry, where they play a crucial role in the mitigation of oceanic pollution by ensuring discharged water is within safe environmental thresholds.
Trust in filter separator technology is steeped in its evolution guided by rigorous engineering and industry standards. The competency of these devices is regularly reviewed against certifications such as ISO 8573 for compressed air purity and the American Petroleum Institute standards, which underscore their reliability across high-stakes applications.
Experience has taught me that the implementation of filter separators can be transformative, with industries reporting increased yield, enhanced safety protocols, and a marked reduction in process-related adversities. These outcomes are fortified by continuously evolving design methodologies, including the integration of smart monitoring systems that anticipate malfunctions before they impact operations.
To harness the full potential of filter separators, meticulous selection tailored to specific industrial requirements is crucial. Factors such as pressure ratings, flow capacity, and the nature of the contaminants are critical in optimizing their performance. Engaging with manufacturers who offer bespoke solutions ensures that the applied technology perfectly aligns with operational objectives, fostering an ecosystem of efficiency and security.
In summary, through my extensive interactions and observations, filter separators emerge not just as functional apparatus but as keystones of industrial excellence. Their strategic positioning in fluid processing workflows ensures their standing as not only beneficial but essential. The true measure of their value lies in their unparalleled ability to safeguard processes, environment, and economy—a testament to their enduring presence in the landscape of industrial filtration solutions.