Filter separators are pivotal components in industries where purity and smooth operational flow are critical. The intricate design of a filter separator allows it to efficiently separate solids and liquids from gases, which is indispensable in various fields like petrochemical processing, natural gas treatment, and industrial manufacturing. Understanding their operation and benefits can significantly enhance the performance and longevity of industrial operations.
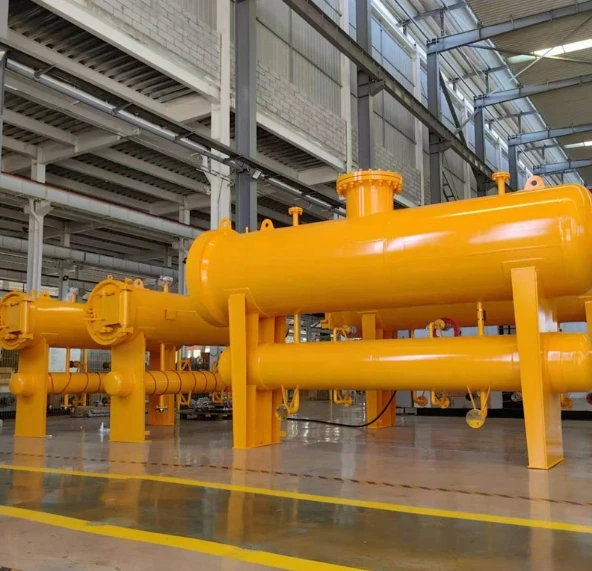
The expertise involved in designing a filter separator is considerable, given the complexity of the tasks they perform. These devices operate on the principle of mechanical separation, using different methods such as gravity separation, coalescing filters, and centrifugal force to remove contaminants. The effectiveness of a filter separator lies in its ability to leverage these principles to achieve high levels of purity in processed materials.
Filter separators usually consist of multiple elements that each play a key role in the separation process. At the initial stage, larger solid particles are removed from the gas flow through a series of baffles or vane packs that use inertia to separate them from the liquid or gas. In subsequent stages, finer particles are coalesced into larger droplets or particles that can be more easily removed by additional filtration media. This multi-stage approach not only enhances the separation process but also ensures that the system can handle different types of contaminants efficiently, providing a versatile solution for many industries.
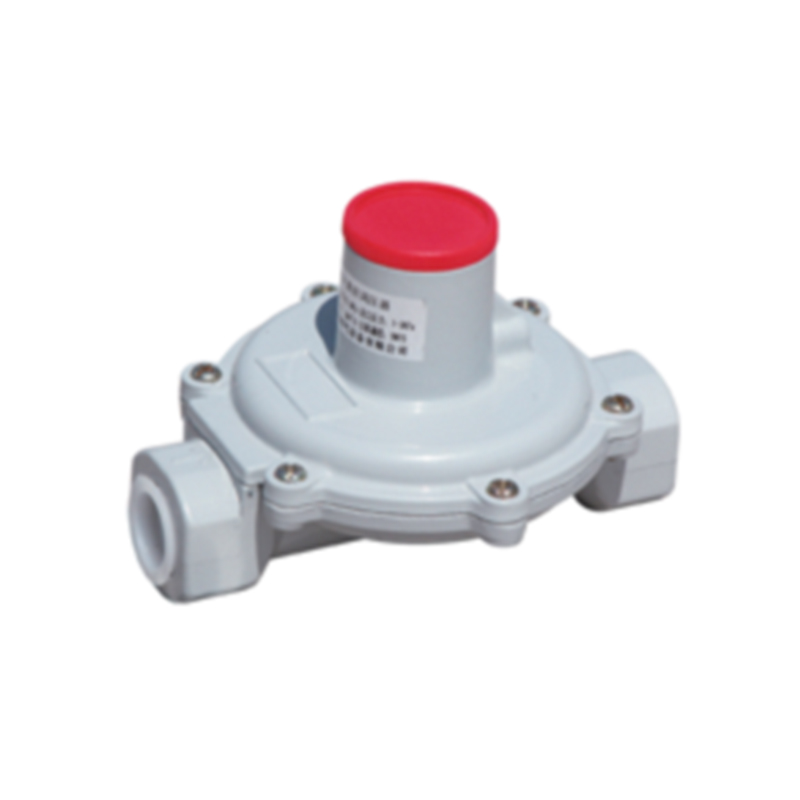
In terms of experience, operators and engineers have noted the tangible benefits of filter separators in improving operational efficiency. For instance, in the natural gas industry, where the purity of gas is paramount, the use of filter separators prevents compressor fouling and ensures that delivery specifications are consistently met. This reliability translates into significant cost savings by reducing downtime and maintenance expenses.
filter separator
Authoritativeness in the design and implementation of filter separators is evidenced by extensive research and development efforts. Leading manufacturers conduct rigorous testing and quality assurance to optimize their products for a variety of operational conditions. The materials used in constructing filter separators, such as stainless steel and corrosion-resistant alloys, are selected for their durability and ability to withstand aggressive environments. This authority in design not only guarantees long service life but also enhances trust among users, knowing that they are investing in a proven, reliable technology.
Moreover, the trustworthiness of a filter separator is also reflected in its compliance with industry standards and regulations. Adhering to standards such as ASME (American Society of Mechanical Engineers) and API (American Petroleum Institute) underscores a commitment to safety and performance, which reassures operators regarding the integrity and reliability of their separation processes.
Advancements in technology continue to push the boundaries of what filter separators can achieve. Recent developments have focused on improving the efficiency of filtration media and developing more sophisticated automated monitoring systems that allow for real-time tracking of separator performance. These innovations enable quicker responses to operational changes, further reinforcing the role of filter separators as essential tools in modern industrial operations.
In conclusion, filter separators embody a delicate balance of engineering ingenuity and practical application, serving as vital components in maintaining the purity and efficiency of industrial processes. Their robust design, coupled with the ability to adapt to various operational demands, underscores their importance. With continuous improvements and adherence to high standards and regulatory compliance, filter separators are indispensable in ensuring operational excellence across diverse industries.