Filter separators are essential components in various industrial applications, ensuring the removal of contaminants and impurities from fluids and gases. A filter separator offers efficacy in safeguarding equipment, optimizing processes, and enhancing safety within operations. Drawing from years of direct industry involvement, this guide delves into the intricacies of filter separators, unraveling their significance, functionality, and selection criteria.
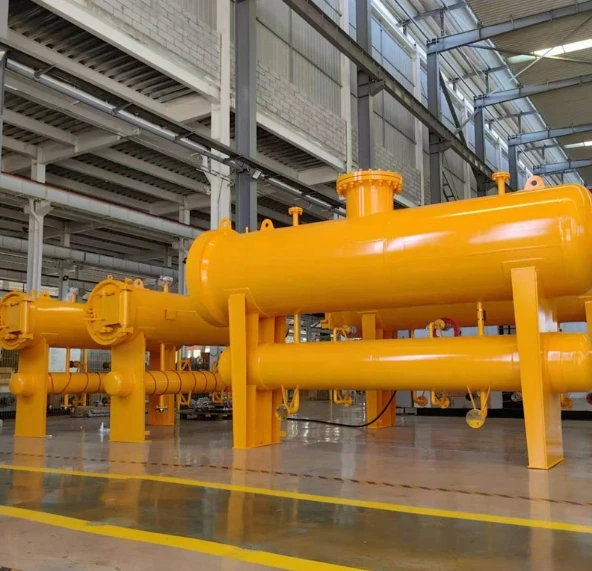
Understanding the Fundamental Role of Filter Separators
Filter separators serve as critical installations in industries such as oil & gas, chemical processing, and power generation. These devices are engineered to handle the demanding task of separating solid and liquid contaminants from gas flows, preventing damage and wear to expensive machinery. Their robust design, coupled with their versatility, makes them indispensable in maintaining the integrity and efficiency of processing systems.
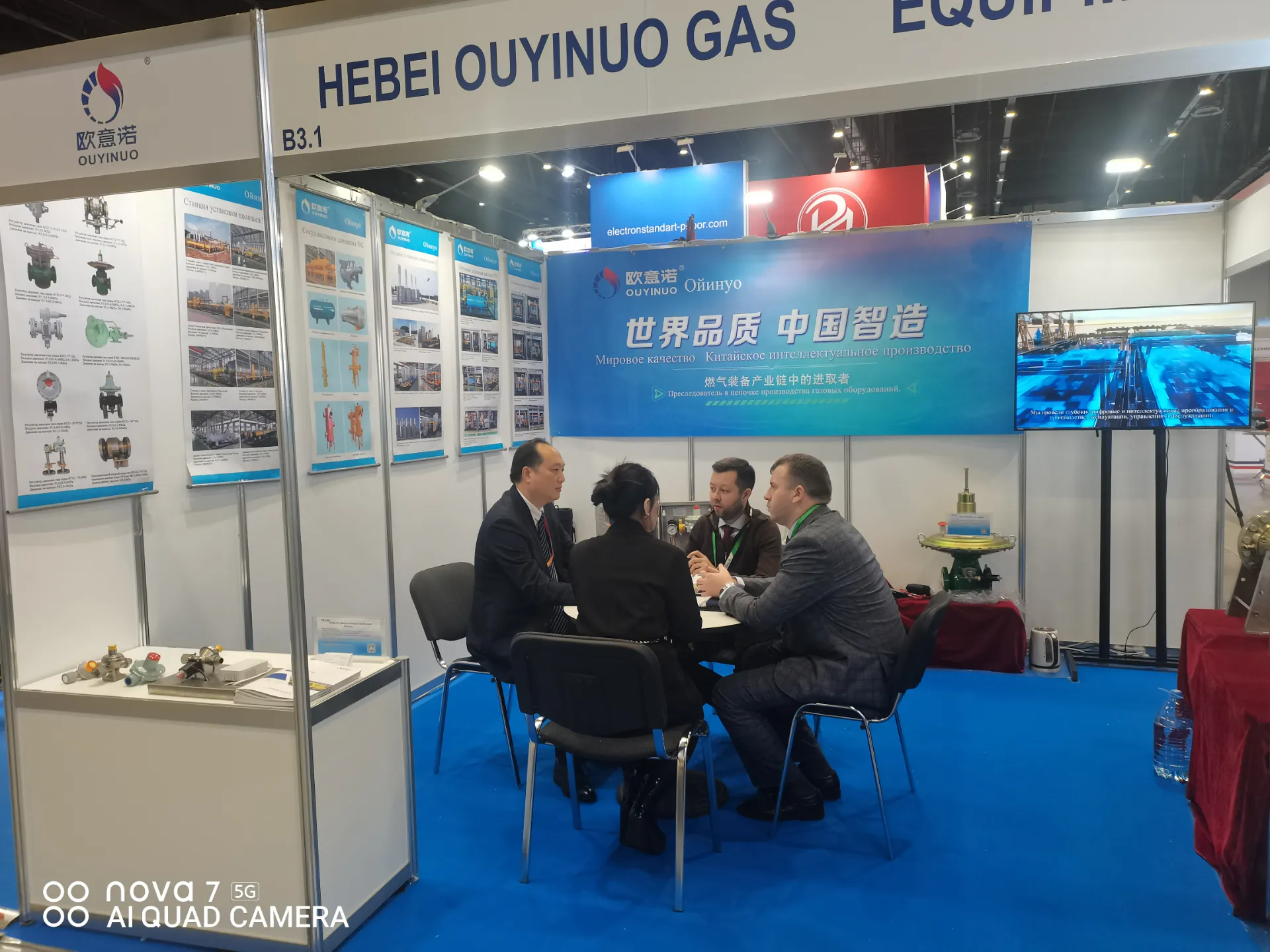
Advanced Expertise in Design and Mechanism
A typical filter separator comprises various intricate parts, including filter elements, a pressurized vessel, and coalescing components, each contributing to its overall functionality. The operation begins when contaminated gas enters the vessel, encountering a series of filter elements that capture large particulate matter with precision. Following this process, the coalescing section efficiently removes smaller droplets and finer particles using advanced surface area techniques and specialized filtration media.
Importantly, the design of a filter separator is pivotal to its effectiveness. Depending on particular industrial needs, engineers may recommend horizontal or vertical configurations, each offering distinct advantages. Horizontal models are optimal for installations with space constraints, whereas vertical systems can handle greater volumes, promising extended service life and reliability.
Authoritative Insights into Selection Criteria
Selecting the right filter separator involves a robust understanding of your specific operational requirements. Critical factors to consider include the nature and pressure of the gas stream, the temperature of the operating environment, and the specific contaminants present. A high-pressure, high-contaminant setting,
for instance, would necessitate a separator with enhanced filtration capabilities and durability.
Furthermore, manufacturers' technical specifications should be studied meticulously, ensuring compliance with relevant industrial standards and certifications. Consultations with filtration experts and reviewing past performance data of potential choices can furnish invaluable insights, aiding in making informed, authoritative decisions.
filter separator
Trust Informed Practices for Maintenance and Performance
Trust is earned through consistent performance and reliability. Consequently, adopting a proactive maintenance routine is crucial for sustaining the performance of filter separators. Regular inspections, timely replacement of worn or clogged elements, and periodic audits of system performance can significantly extend the lifespan of these devices.
Moreover, leveraging technologically advanced monitoring systems can offer real-time analytics on filter performance, aiding prompt troubleshooting and facilitating actionable insights. Engaging with reputable suppliers known for their customer support and technical assistance further reinforces the trustworthiness of your filtration solutions.
Emphasizing Safety and Economic Efficiency
The deployment of filter separators confers considerable safety benefits, crucial in environments handling volatile gases or hazardous materials. By preventing contaminant accumulation, these devices significantly reduce the risk of corrosive damage, flammable conditions, and unexpected equipment failures, safeguarding human capital and assets.
On an economic front, investing in high-quality filter separators yields substantial returns. Optimized flow processes and reduced downtime translate to cost savings, efficiency gains, and enhanced production output. The ability to protect downstream equipment further underscores the compelling value proposition of integrating premium filtration systems.
Innovation in the Filtration Landscape
The evolution of filter separators is characterized by ongoing innovations that enhance operational efficacy and environmental stewardship. Emerging models incorporate advanced materials and smart technologies, capable of adapting to fluctuating operational demands and minimizing environmental impacts.
To conclude, filter separators are indispensable for modern, sustainable industrial operations. By emphasizing their proper selection, maintenance, and innovation adoption, businesses can significantly enhance both their productivity and safety measures. Embrace these trusted tools, underpinned by expertise and experience, as integral components of your operational strategy.