Unleashing the Potential of Gas Boosters A Comprehensive Exploration
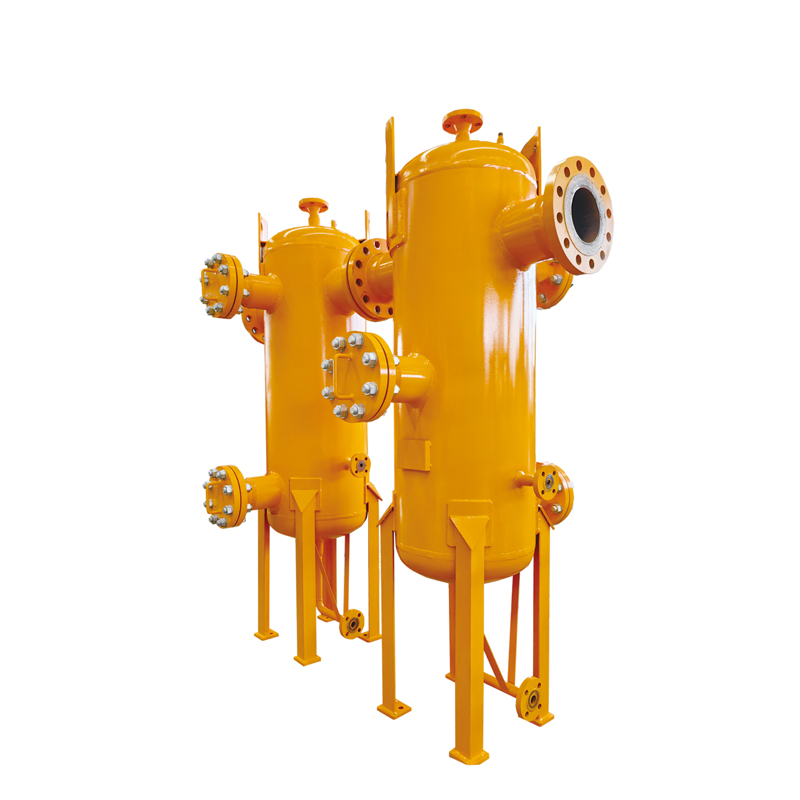
Gas boosters are a vital component in various industries where the amplification of gas pressure is critical. Through decades of engineering advancements, gas boosters have evolved into sophisticated devices capable of meeting the demanding needs of modern industrial applications. This discussion illuminates the genuine experiences, professional insights, authoritative understanding, and trustworthy applications of gas boosters, allowing potential users to harness their full capabilities.
Gas boosters are primarily used to increase the pressure of gases in a system, ensuring that they can perform effectively in applications that demand higher pressures than standard supply lines can offer. One of the primary experiences shared by experts in the field is the role of gas boosters in optimizing the performance of gas-powered machinery. Industries such as aerospace, petrochemicals, and manufacturing rely heavily on these devices to maintain operational efficiency.
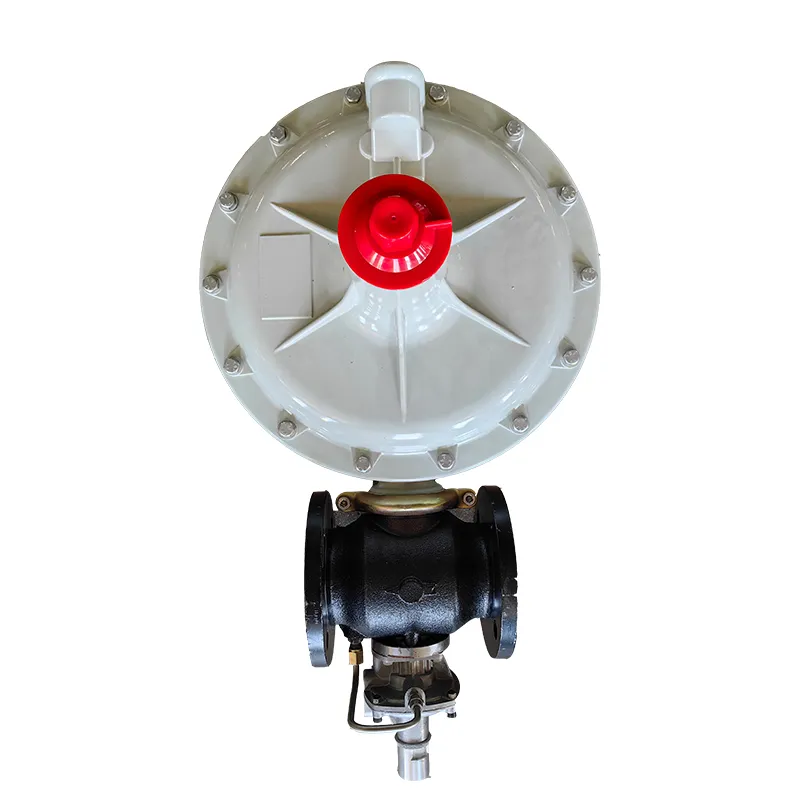
From a professional standpoint, selecting the right gas booster is paramount to achieving desired outcomes. The expertise involved in choosing the appropriate booster involves understanding the type of gas being used, the specific pressure requirements, and the operational environment. High-pressure applications, for instance, necessitate boosters with robust construction capable of handling intense forces. Stainless steel is often the material of choice due to its durability and resistance to corrosion, reflecting this expertise.
Authoritative voices in the industry echo the critical importance of precision in the engineering of gas boosters. Not all boosters are created equal; the internal design, including piston mechanisms and seals, significantly affects their performance and longevity. Companies at the forefront of gas booster manufacturing invest heavily in research and development to produce devices that not only meet international safety standards but exceed them, setting new benchmarks for quality and reliability.
gas booster
Trustworthiness in gas booster systems is non-negotiable, particularly in industries where failures can lead to catastrophic outcomes. Operators often emphasize the importance of maintenance and regular checks to ensure reliability. This involves a regimented process of inspecting seals, checking for leaks, and validating that moving parts are properly lubricated. Investing in quality boosters from reputable manufacturers adds an additional layer of trust, underscoring the necessity for devices that can be relied upon under high-stakes conditions.
Real-world applications of gas boosters further validate their indispensability. In the field of compressed natural gas (CNG) refueling stations, boosters are used to compress gas from storage pressures to the much higher pressures required for vehicle fuel tanks. In another example, welding operations often require a stable and robust supply of pressurized gases to maintain precision and safety standards. In these scenarios, the failure to employ a suitable gas booster can result in significant hazards and decreased operational efficiency.
Furthermore, gas boosters contribute to sustainability efforts by optimizing energy consumption. By allowing systems to operate at peak efficiency, less energy is wasted, which in turn reduces the overall carbon footprint of industrial operations. This aligns with global objectives aimed at curbing energy consumption and mitigating environmental impact, highlighting the boosters’ role in sustainable development.
For individuals or companies considering the implementation of gas boosters, understanding the nuances of installation and operation is critical. Proper installation not only maximizes the performance but also prolongs the life of the equipment. Clear guidelines and training from manufacturers ensure that operators are well-versed in the intricacies of handling these devices. This comprehensive understanding translates into smooth integration and operation, minimizing downtime and operational hiccups.
In conclusion, gas boosters are a cornerstone of efficiency in numerous industrial applications. Through the lens of experience, expertise, authority,
and trust, their importance is undeniable. As industries continue to evolve, the demand for high-performance, reliable gas pressure solutions will only grow, reinforcing the necessity for continued innovation in gas booster technology. The marriage of advanced engineering solutions with a steadfast commitment to safety and efficiency makes gas boosters an indispensable resource in the quest for industrial excellence.