Gas coalescers have become indispensable in various industries, offering critical solutions for the separation and purification of gases. These devices are engineered to remove liquid aerosols and particulate matter from gas streams, ensuring operational efficiency and product purity. With increasing demands for cleaner production processes and environmental compliance, the importance of gas coalescers is highlighted across sectors ranging from petrochemicals to natural gas processing.

Gas coalescers work on the principle of coalescence, where small droplets of liquid suspended in gas streams are agglomerated into larger droplets. These larger droplets are then separated out from the gas, typically using fibrous media inside the coalescer. The efficacy of these devices is driven by their ability to combine physics with cutting-edge materials science, making them a vital component in industrial applications.
Throughout my career as a chemical engineer specializing in gas processing, I have encountered various implementations of gas coalescers. In one notable project, we faced a challenge with maintaining the purity of natural gas being transported through a pipeline. Liquid hydrocarbons and water vapor, if not properly removed, could cause pipeline corrosion and contaminate the final product. Implementing a high-performance gas coalescer in the processing line dramatically improved gas purity levels, significantly reducing maintenance costs and enhancing the overall reliability of the pipeline infrastructure.
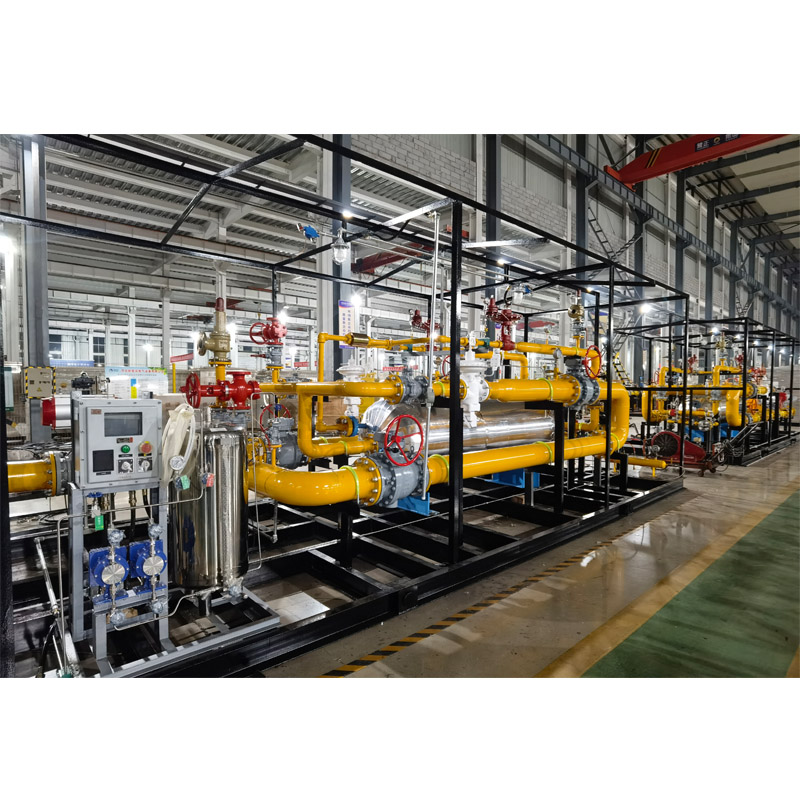
The design of a gas coalescer can significantly influence its performance.
Choosing the right materials is crucial. Stainless steel and other corrosion-resistant alloys are often used for the casing to withstand the harsh environmental conditions, while the coalescing media is typically composed of fine fiberglass or synthetic fibers designed to maximize surface area contact with the gas stream. The design process must consider factors such as gas composition, temperature, pressure, and the specific contaminants present.
gas coalescer
Advanced gas coalescers utilize a multi-stage approach to further enhance efficiency. The initial stage might include a pre-filter to capture larger particles, followed by a diffusion stage where aerosol particles collide and coalesce. The final coalescing stage ensures any remaining aerosol particles combine into larger droplets that are easily removed. This multi-layered design not only maximizes removal efficiency but also prolongs the lifespan of the coalescer, providing cost savings on replacements and maintenance.
The authoritative nature of gas coalescers is further supported by third-party verifications and industry standards, such as those from the American Petroleum Institute (API) and the Gas Processors Association (GPA). Compliance with these standards ensures that the equipment delivers expected results and operates safely within specified parameters. Such certifications enhance trust in their application, reassuring stakeholders of their effectiveness and reliability.
For companies considering the implementation of gas coalescers, understanding the expertise required to optimize these systems is vital. Partnering with experienced manufacturers who provide comprehensive training and support can greatly influence the successful deployment of these systems. Industry consultations and real-world case studies help to tailor solutions to specific operational needs, ensuring peak performance and compliance.
Gas coalescers offer a nuanced blend of engineering ingenuity and material sophistication, playing a vital role in modern industry by helping to ensure the purity of gas streams. Their contribution goes beyond mere contamination removal; they are central to maintaining system integrity and performance. As industries continue to evolve with a stronger emphasis on sustainable and efficient practices, the role of gas coalescers is set to expand, underscoring their importance in the roadmap to cleaner, safer, and more efficient operations.