Gas coalescers are essential components in many industrial applications, performing the critical function of separating gas from liquid in process streams. Their significance spans across various sectors, including natural gas refining, petrochemical processing, and power generation. Understanding the intricacies of how gas coalescers work, and selecting the right one for your application, requires expertise and reliable sources of information.
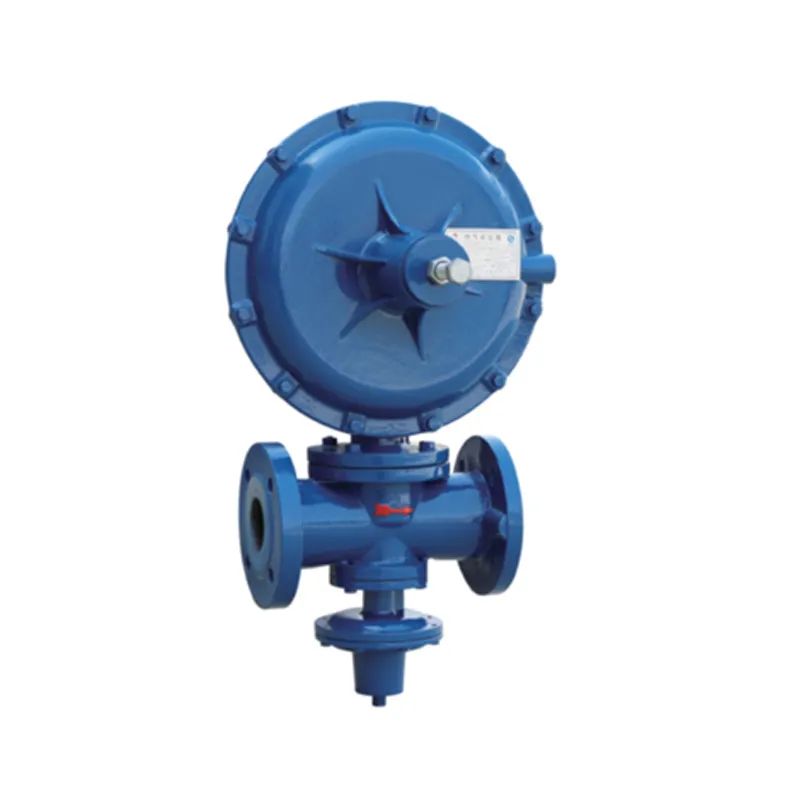
Gas coalescers operate by filtering fine liquid droplets from a gas stream, ensuring that the gas output is free from moisture and other impurities. Typically, these devices utilize a specialized filter medium designed to trap and coalesce small liquid particles into larger droplets, which then fall to the bottom of the coalescer for removal.
Experience proves that investing in a high-quality gas coalescer can significantly enhance operational efficiency. For instance, in the natural gas industry, a well-maintained coalescer can prevent compressor damage and pipeline corrosion, both of which are costly issues. Additionally, cleaner gas results in improved combustion efficiency, reducing pollutants and meeting stringent environmental regulations.
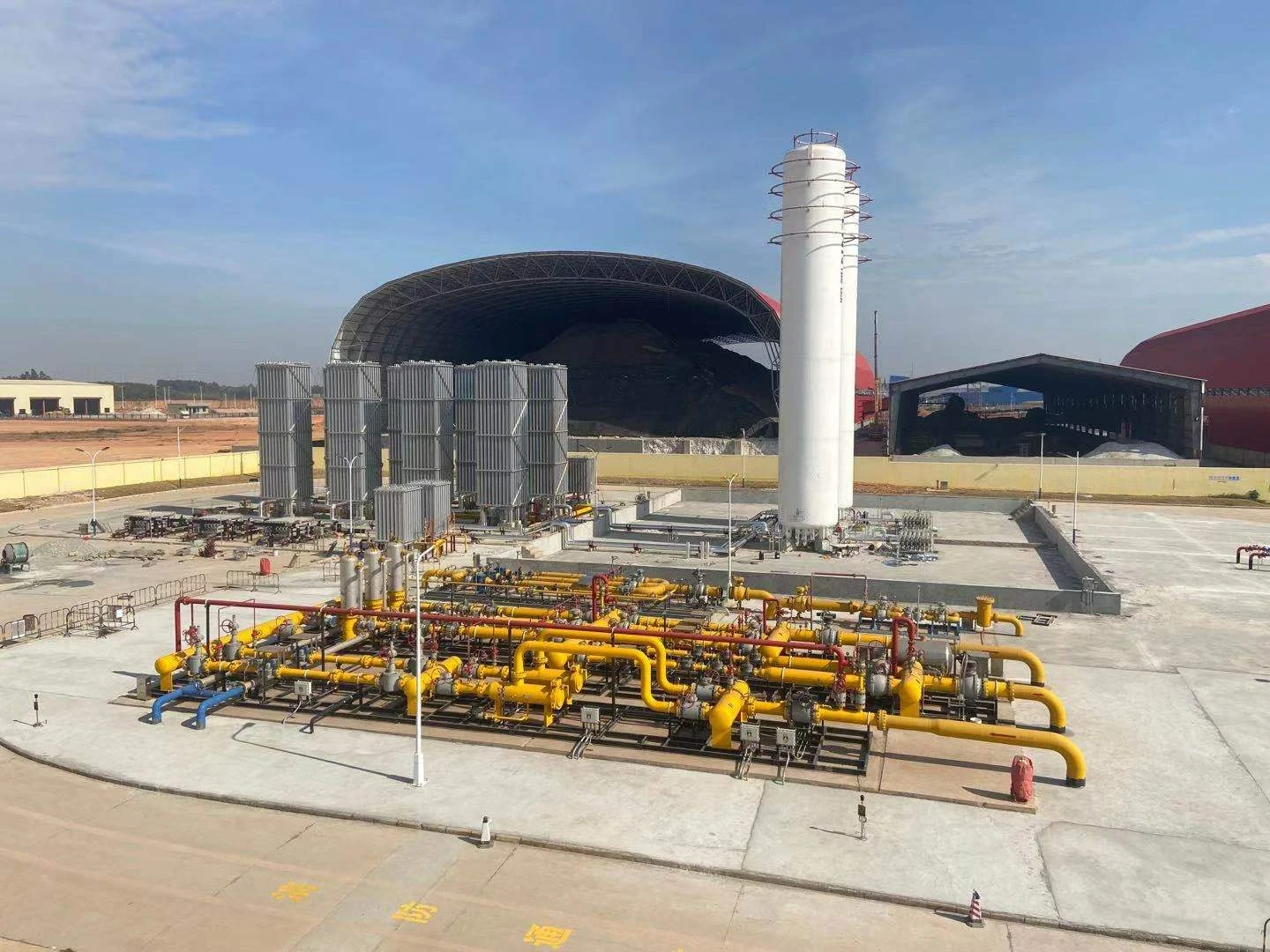
From a professional standpoint, selecting a gas coalescer must account for the specific parameters of the operating environment. Factors such as operating pressure, temperature, gas composition, and flow rate are critical in determining the appropriate coalescer design. Expertise in evaluating these parameters ensures optimal performance and longevity of the equipment.
Manufacturers who specialize in gas handling equipment often issue detailed guidelines on selecting and maintaining coalescers. Their recommendations usually include selection criteria based on the droplet size distribution, flow velocity, and the expected life cycle attributed to the coalescer's material construction. Engaging with these guidelines demonstrates a commitment to professional standards and operational excellence.
gas coalescer
Authoritativeness in the realm of gas coalescers is supported by technological advancements and industry research. Many leading companies invest heavily in R&D to develop new materials and designs that improve the effectiveness of gas coalescers. Innovative technologies, such as advanced synthetic micro-fibers and enhanced surface coatings, exemplify the cutting-edge progress driving coalescer efficiency and durability.
Trustworthiness, particularly from a supplier or manufacturer's perspective, is built through consistent product performance and support. Reliable coalescer suppliers offer comprehensive service packages that include not just the provision of high-quality coalescers, but also thorough installation guidance, regular maintenance check-ups, and technical support. Such end-to-end services build a foundation of trust, ensuring that customers have the confidence that their equipment will perform as required under various conditions.
Practical experiences collected from field operations underscore the importance of routine maintenance and inspection in sustaining the effectiveness of gas coalescers. Regularly checking for blockages, monitoring pressure differentials across the coalescer, and ensuring the integrity of seals and housings prevent unexpected downtimes and maintain process efficiency.
In conclusion, gas coalescers are indispensable in providing clean, dry gas across numerous industrial settings. Their impact on operational efficiency and environmental compliance underscores the need for careful selection and diligent maintenance. Grounded in experience, professional expertise, and authoritative insights, a well-chosen gas coalescer ensures reliability and longevity, upholding industry standards and fostering trustworthiness among its users.