In the complex realm of industrial processing, ensuring the purity and efficiency of gases is paramount for optimal operations. A gas coalescer plays a quintessential role in refining gas streams, effectively removing contaminants that could impede performance, safety, and equipment longevity. As industries continue to evolve with more stringent environmental and safety regulations, understanding the intricacies of gas coalescers from an expert viewpoint can significantly enhance operation outcomes.
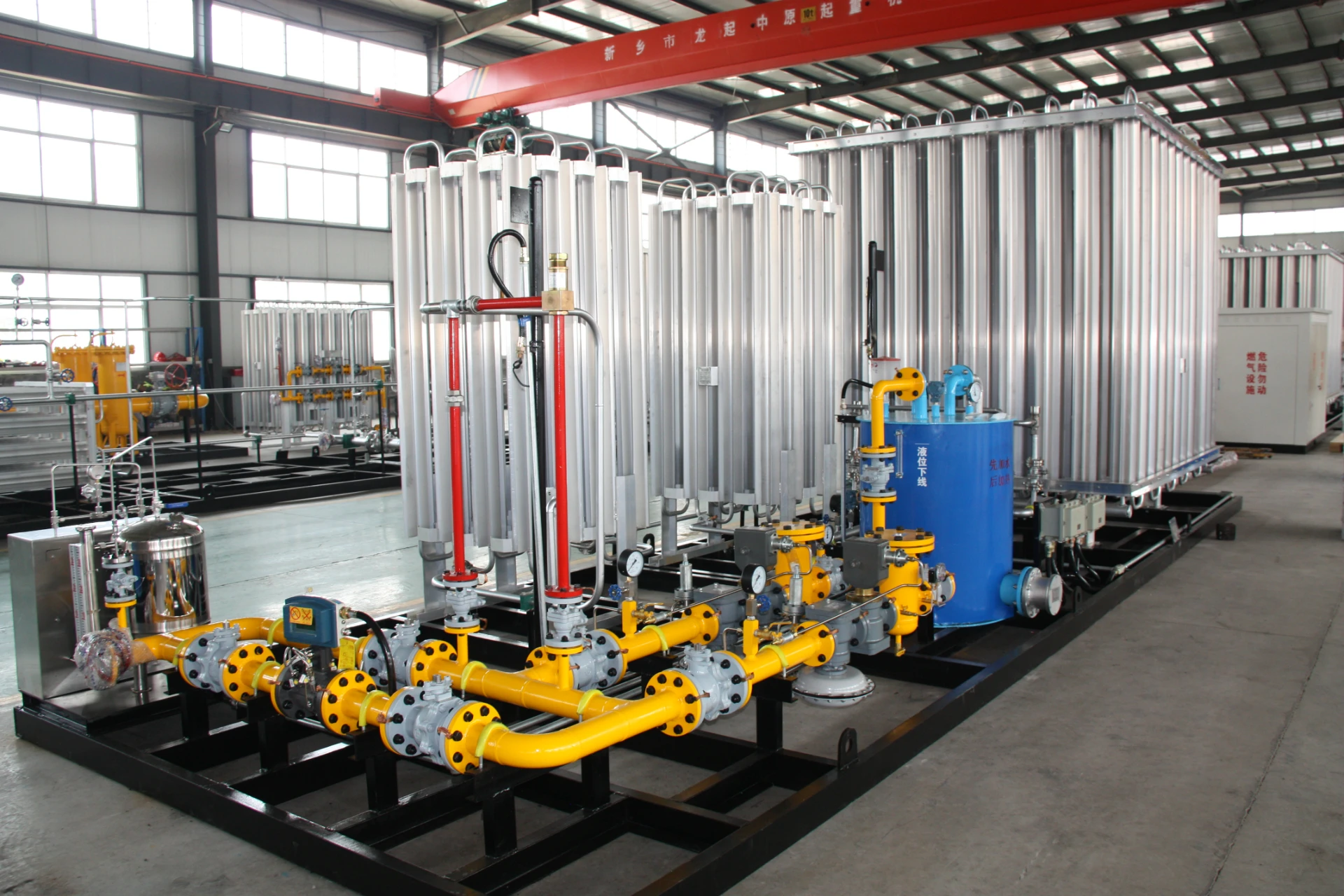
Gas coalescers are sophisticated filtration systems designed to capture and eliminate liquid and solid particulates from gas streams. Their operation is anchored on coalescence – a process where smaller droplets merge to form larger ones, facilitating easier removal. By employing specialized filter media, these devices ensure that even the most diminutive particles are agglomerated and extracted, delivering a purer gas output.
Expertise in the functionality of gas coalescers reveals that their design varies widely depending on the specific application and operational demands. For instance, in natural gas processing, gas coalescers are critical for extracting moisture and hydrocarbon liquids, which if left unchecked, could lead to corrosion, reduced calorific value, and compromised product specification. Similarly,
in chemical plants, these coalescers prevent contamination of catalysts and ensure process integrity.
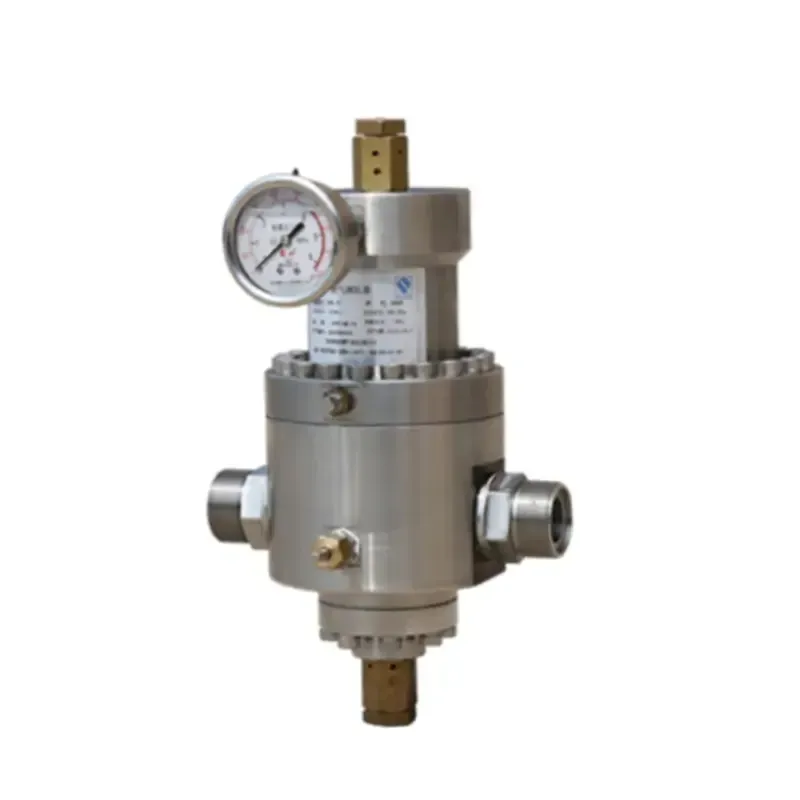
The efficiency of a gas coalescer is primarily determined by its filter media. Advanced materials such as pleated fibreglass or sintered metal offer a balance of high surface area and durability, essential for high-volume gas streams. Such advancements have positioned gas coalescers as vital components in sectors ranging from petrochemical to food and beverage, where they guarantee compliance with environmental and safety standards while optimizing operational economics.
gas coalescer
From an authoritative stance, the deployment of gas coalescers must consider factors such as pressure drop, flow capacity, and maintenance requirements. It’s imperative that the coalescer is adequately sized and engineered to withstand the operational pressures and temperatures unique to its environment. Industry professionals advocate for comprehensive analytical and performance testing during the selection process to mitigate risks associated with improper specification – a common pitfall that can lead to inefficient filtration, increased operating costs, and equipment failure.
Moreover, real-world experience highlights that routine maintenance of gas coalescers is crucial for sustained performance. This includes regular inspection for clogging, cleaning of filter elements, and timely replacement to prevent operational downtimes. Companies investing in predictive maintenance technologies have witnessed notable reductions in unscheduled outages, showcasing the tangible benefits of leveraging modern data analytics in these systems.
With trustworthiness being a critical factor, operators emphasize sourcing gas coalescers from reputable manufacturers known for stringent quality control and robust after-sales support. Such partnerships assure that operations remain compliant with evolving legislative mandates and industry benchmarks, thereby instilling confidence amongst stakeholders and investors.
In conclusion, gas coalescers are indispensable in the pursuit of clean and efficient industrial processes. Their ability to refine gas streams not only enhances operational efficiency but also ensures compliance with the highest levels of environmental stewardship and safety protocols. As technological advancements continue to redefine the capabilities of these systems, embracing an approach that combines deep expertise, authoritative selection, and trustworthy maintenance practices will remain instrumental in exploiting their full potential.