Gas heat exchangers are integral components in numerous industrial processes and household applications, often acting as the backbone of modern heating systems. These devices are engineered to transfer heat between two or more fluids and are pivotal in enhancing energy efficiency and reducing operational costs. With a market inundated with various models, it's crucial to delve into the nuances of gas heat exchangers by examining their design, functionality, and application.
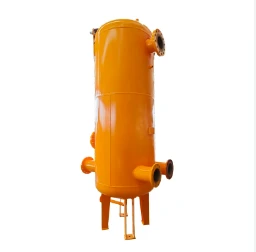
A gas heat exchanger operates on a seemingly simple principle – transferring heat from one medium to another without the two coming into direct contact. This mechanism is usually executed through solid partition walls or plates, which allow heat transference while maintaining the separation of gases or fluids involved. The sophistication of these systems lies in their design, which can vary from basic to intricate structures. Some of the primary types include shell and tube heat exchangers, plate heat exchangers, and air-cooled heat exchangers.
Shell and tube heat exchangers are perhaps the most commonly used, characterized by their robust design that accommodates high temperatures and pressures, making them ideal for industrial applications. Conversely, plate heat exchangers are known for their compact design and high heat transfer efficiency, suitable for both industrial and residential use. Air-cooled exchangers, on the other hand, eliminate the need for cooling water by dispersing heat into the surrounding air, thus serving environments where water resources are limited.
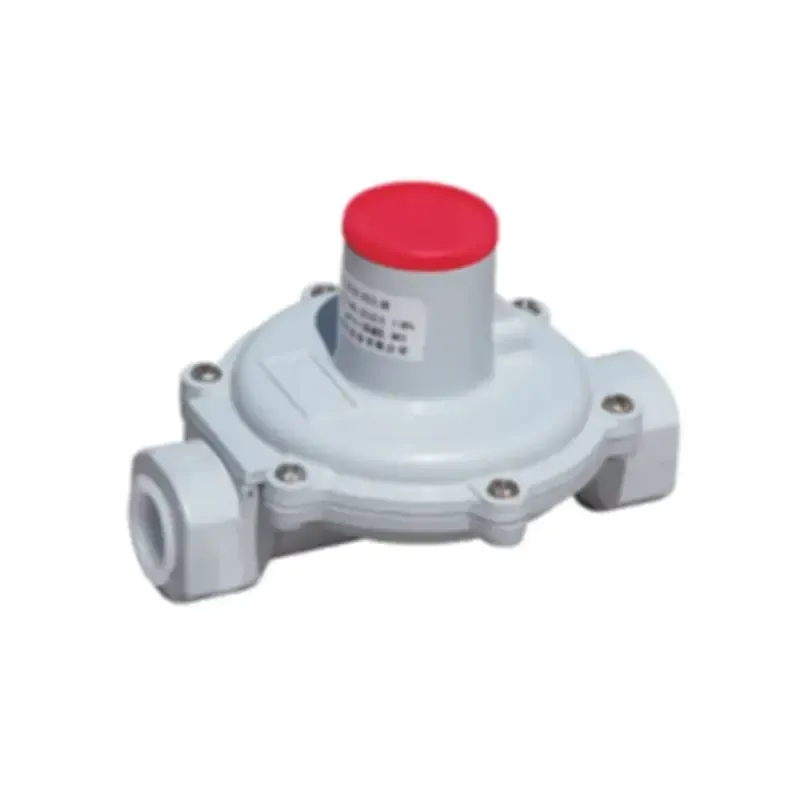
The expertise in choosing the appropriate gas heat exchanger is paramount. Professionals should consider factors like heat transfer efficiency, compatibility with existing systems, ease of maintenance, and cost. For instance, systems requiring frequent maintenance shutdowns could benefit from plate heat exchangers, known for their easy access and cleaning features. Conversely, industries dealing with corrosive environments might prefer shell and tube versions made from materials like stainless steel or corrosion-resistant alloys.
gas heat exchanger
An authoritative understanding of gas heat exchangers also demands familiarity with regulatory standards and industry certifications, ensuring that the selected products are compliant and safe for use. These regulations often dictate the material type,
design specifications, and operational limits. Adopting products that adhere to certifications from recognized standards organizations not only guarantees safety but also enhances performance reliability, thereby bolstering consumer trust.
From an experience standpoint, proper installation and routine maintenance cannot be overemphasized. Misalignment or improper assembly can reduce the efficiency of heat exchangers, leading to increased energy consumption and operational costs. Regular inspections and cleaning schedules can prolong the life of these systems, significantly reducing the likelihood of unexpected downtimes. Professionals should advocate for using advanced diagnostic tools to monitor performance and detect issues early.
Trustworthiness in the realm of gas heat exchangers is built on transparent information dissemination and customer education. Manufacturers and suppliers enhancing engagement through detailed product documentation, customer testimonials, and case studies can significantly boost consumer confidence. Additionally, offering training sessions and workshops not only educates but also empowers users to make informed decisions regarding their heating solutions.
In conclusion, the realm of gas heat exchangers combines engineering prowess with practical utility, making it indispensable in both industrial and domestic arenas. Understanding their types, functions, and nuances can lead to more informed choices that enhance energy efficiency while minimizing costs. By aligning expertise in product selection with regulatory understanding and customer-centric approaches, stakeholders can ensure they meet and exceed expectations in both performance and reliability.