Gas heat exchangers are integral components in various industrial processes, known for their efficiency and reliability in transferring heat from one medium to another. Designed to handle gaseous substances, these heat exchangers play a pivotal role in systems ranging from HVAC units to large-scale power plants.
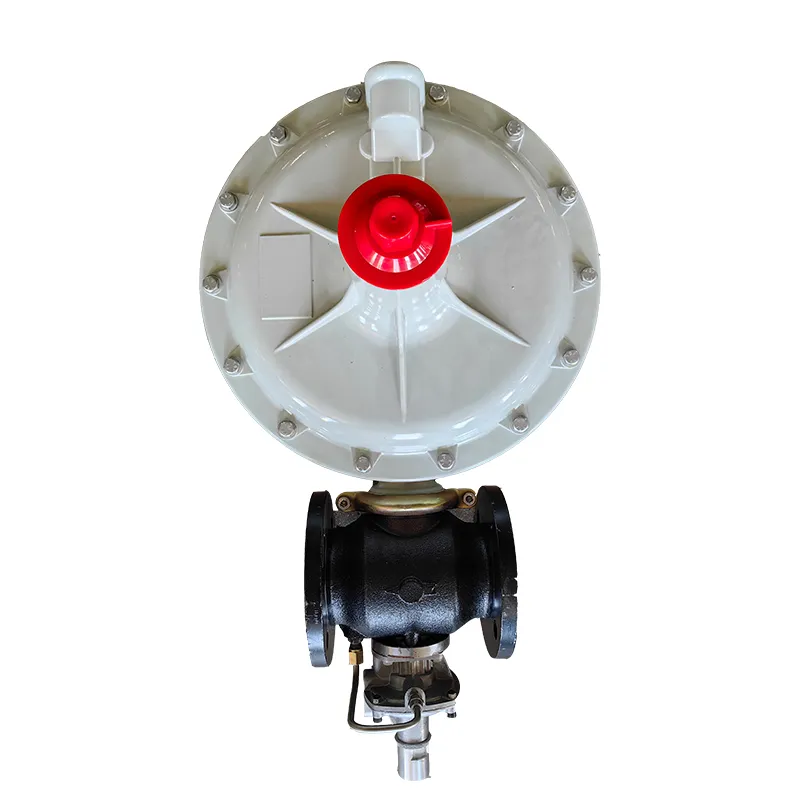
Experience has demonstrated that selecting the right gas heat exchanger can significantly impact system efficiency and longevity. Industrial settings, such as chemical plants or refineries, often require heat exchangers that can withstand corrosive environments and high temperatures.
It's crucial to consider the material construction of the heat exchanger. For gas heat exchangers, materials like stainless steel or Inconel, an alloy known for its exceptional resistance to oxidation and corrosion, are preferred for their durability and ability to maintain performance under extreme conditions.
In the pursuit of expertise, engineers and technicians frequently conduct performance evaluations of gas heat exchangers. A critical aspect of these evaluations involves assessing the exchanger's thermal efficiency, which dictates how effectively it can transfer heat relative to the energy consumed. Computational fluid dynamics (CFD) models are often used in the design phase to simulate thermal exchange and identify opportunities for optimization before fabrication. Additionally, pressure drop is a consideration of utmost importance; a design that minimizes pressure loss can lead to substantial energy savings, making it a critical point of focus both in initial design and operational phases.
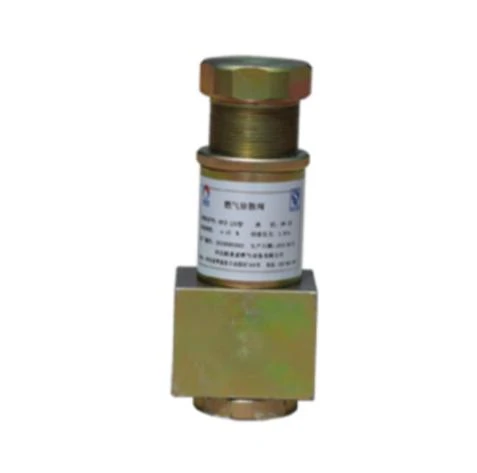
From an authoritativeness perspective, industry standards, such as those set by the Tubular Exchanger Manufacturers Association (TEMA) or the American Society of Mechanical Engineers (ASME), govern the design and operation of gas heat exchangers. Adhering to these standards doesn’t just ensure safe and reliable operation but also boosts the exchanger's credibility and acceptability across different markets worldwide. Certification by credible bodies provides assurance that the product has been rigorously tested and meets the high expectations of performance and safety.
Trustworthiness is often built through ongoing maintenance and performance monitoring. Routine inspections and maintenance schedules are imperative to early identification of wear or potential failure points, such as fouling or scaling. Featuring devices capable of real-time monitoring and diagnostics enhances trust, as operators can receive alerts and initiate timely interventions, preventing costly downtimes. The integration of IoT devices and sophisticated monitoring systems provides live insights into the operational parameters of gas heat exchangers, offering a data-driven approach to maintenance and optimization.
gas heat exchanger
In the realm of emerging technologies, advancements in materials science and heat transfer techniques are paving the way for next-generation gas heat exchangers. Innovations such as microchannel heat exchangers have started to gain traction due to their compact size and high heat transfer coefficients, making them ideal for applications with space constraints or where high efficiency is mandatory. Additionally, additive manufacturing (3D printing) is making significant strides in producing custom components with intricate geometries that enhance thermal performance and reduce manufacturing time.
Utilizing a gas heat exchanger system effectively requires a comprehensive understanding of the specific application needs. For HVAC systems, where energy efficiency and environmental impact are paramount, it’s advisable to select exchangers that use environmentally friendly materials and refrigerants. Conversely, in industrial applications involving high-temperature processes, focus shifts toward ensuring robust thermal management and safety standards are met.
Engagement with experienced professionals in the field can provide invaluable insights into optimizing the lifecycle and efficiency of gas heat exchangers. Collaboration between manufacturers, engineers, and end-users facilitates the sharing of best practices and innovations, ensuring that the latest developments are leveraged for improved system performance.
In summary, the pivotal role of gas heat exchangers within industrial and commercial settings cannot be overstated. Each aspect, from material selection and design optimization to compliance with industry standards and ongoing monitoring, contributes to the effectiveness and reliability of these systems. As technology evolves, staying informed about the latest advancements and maintaining a committed approach to efficient thermal management will ensure that gas heat exchangers continue to meet the growing demands of modern applications, bolstering their status as essential components in efficient energy management.