Gasification equipment stands at the forefront of modern energy transformation technologies. This advanced machinery offers a sustainable avenue to convert carbonaceous materials like coal, biomass, or even waste into syngas — a versatile fuel that is both cleaner and more efficient than its predecessors. As industries increasingly turn towards greener alternatives to traditional fossil fuels, the role of gasification equipment is becoming ever more critical.
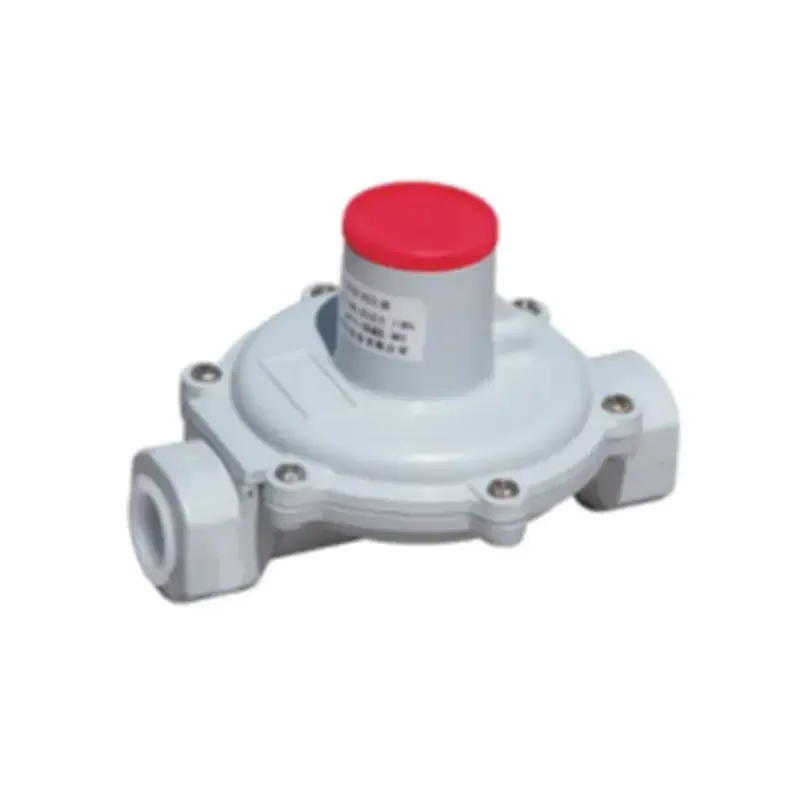
Proficiency in understanding and operating gasification equipment is not merely advantageous; it is essential for industries aiming to enhance their energy solutions. At its core, gasification is a thermochemical process that transforms organic or fossil-based carbonaceous materials under controlled heat and environment. The equipment designed for this process must achieve a delicate balance of temperature, pressure, and chemical reaction dynamics to ensure optimal efficiency and output.
Individuals and businesses interested in integrating gasification technology should prioritize equipment that demonstrates technical superiority and dependability. Companies that manufacture these units, such as GE Energy and Siemens, have invested heavily in research and development to ensure their products are both cutting-edge and reliable. These firms offer equipment with sophisticated features like real-time monitoring systems and adaptive control technologies, which automatically adjust operating conditions to maximize syngas yield and minimize environmental impact.
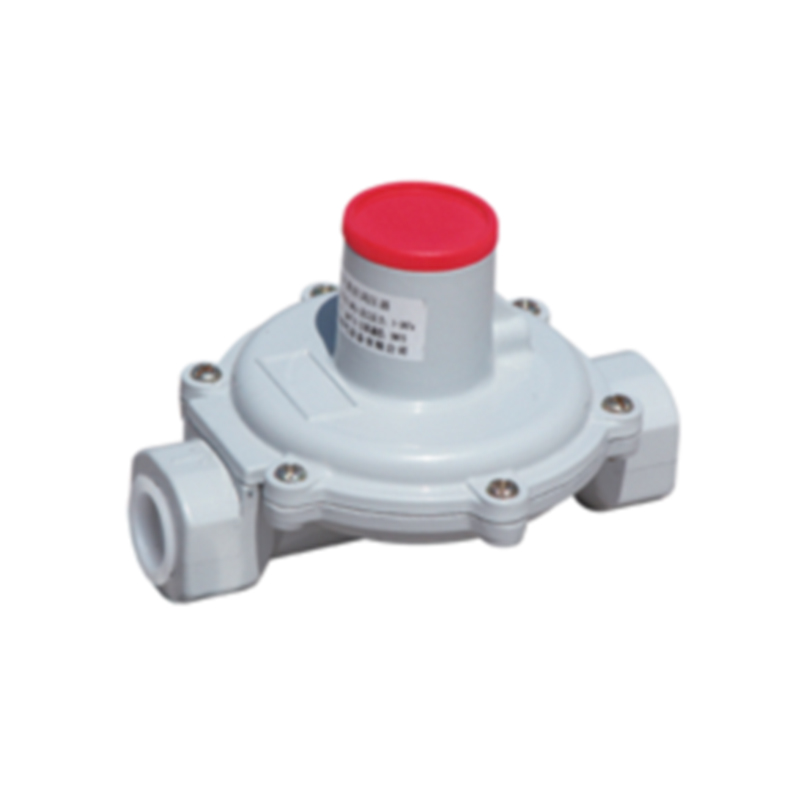
Credibility is an indispensable factor when selecting gasification equipment suppliers. Opting for a manufacturer with an established reputation can significantly reduce the risks associated with equipment performance and long-term reliability. Additionally, thorough evaluation of customer reviews and case studies can provide crucial insights into the practical application and performance of specific models over time. This customer feedback often reveals key aspects of usability and maintenance that may not be immediately apparent from product specifications alone.
gasification equipment
From a professional perspective, mastery over the technical aspects of gasification equipment necessitates a comprehensive training program for operators. This includes an in-depth understanding of feedstock variability, reaction kinetics, and the thermodynamics involved in the gasification process. Operators should undergo rigorous training sessions that cover routine operations, troubleshooting, and safety protocols to ensure the safe and efficient running of the equipment.
Moreover, expert-rich resources such as technical journals and industry forums can significantly contribute to one's expertise. Engaging in communities where professionals discuss latest advancements, share experiences, and provide peer feedback can also foster advanced knowledge and understanding of gasification processes and innovations.
It is important to highlight the environmental and economic benefits associated with gasification equipment. One compelling advantage is the reduced greenhouse gas emissions compared to conventional combustion methods. Since the process primarily occurs in an oxygen-limited environment, gasification produces syngas with a higher hydrogen-to-carbon monoxide ratio, leading to cleaner combustion. Economically, gasification provides a method for waste-to-energy conversion, lowering the cost of energy production by utilizing otherwise discarded materials as valuable feedstock.
In summary, the integration of gasification equipment is not just a technological upgrade but a strategic move towards sustainable and efficient energy management. Through careful selection of equipment, thorough training of operators, and reliance on credible sources and expert communities, businesses can harness the full potential of gasification technology. As this sector advances, those who adapt early will position themselves as leaders in the transition toward a sustainable, energy-efficient future.