In the realm of industrial engineering and manufacturing, gas pressure vessels are indispensable components, pivotal in various applications ranging from energy sectors to chemical processing. These vessels, designed to contain gases at significantly higher pressures than ambient conditions, play a crucial role in ensuring the safe and efficient storage and transportation of gases. Their design, construction, and maintenance directly influence their performance and longevity, making expertise and authoritativeness in this field paramount.
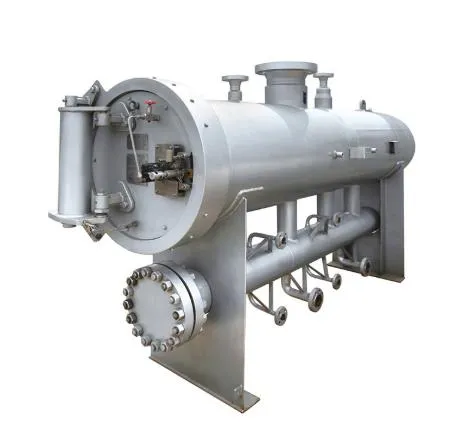
Experience in handling gas pressure vessels reveals that their complexity extends far beyond mere containment. The engineering expertise required to design these vessels involves understanding the nuanced interactions between material properties, vessel geometry, and operational conditions. Typically made from high-strength steel alloys or composites, these materials must withstand extreme pressures and potential temperature fluctuations without compromising integrity. Engineers adept in this specialization emphasize the criticality of proper material selection and precise manufacturing techniques to mitigate risks such as stress corrosion cracking or material fatigue.
The authoritative literature on gas pressure vessels stipulates adherence to stringent international standards, such as the ASME Boiler and Pressure Vessel Code. This code provides comprehensive guidelines on design, fabrication, inspection, and testing procedures. Engineers and manufacturers are encouraged to adopt these standards diligently to ensure maximum safety and reliability. The expertise invested in understanding these codes is not just academic; it is the cornerstone of trust between manufacturers, regulatory bodies, and end-users.
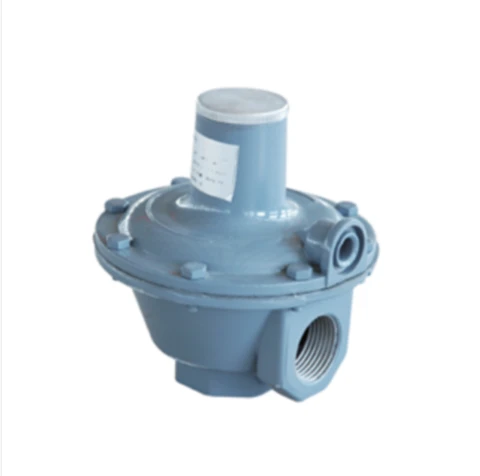
Trustworthiness in the context of gas pressure vessels is a non-negotiable element. Stakeholders, from plant operators to insurance companies, demand unequivocal assurance that these vessels will perform under expected conditions without failure. This trust is built on transparent manufacturing processes, rigorous testing protocols, and comprehensive maintenance schedules.
Proven track records from reputable manufacturers instill confidence in buyers who require vessels for critical operations. A notable example is the routine deployment of non-destructive testing methods, such as ultrasonic testing and radiographic inspections, which ensure continued vessel integrity after prolonged use.
gas pressure vessel
For those seeking to procure or use gas pressure vessels, engaging with manufacturers and professionals who exhibit these four pillars—experience, expertise, authoritativeness, and trustworthiness—ensures that the vessels not only meet operational demands but also adhere to the highest safety standards. Consequently, choosing the right partner for manufacturing or maintaining these vessels is as crucial as the engineering behind them. It is this commitment to excellence that separates standard compliance from exceptional operational reliability.
Businesses aiming to utilize these vessels effectively should also implement continuous training and education programs. This fosters a culture of safety and awareness, enabling staff to identify and respond to potential issues proactively. Through simulation-based training and workshops, operational teams can experience real-world scenarios, enhancing their capability to manage and mitigate risks associated with high-pressure environments.
In conclusion, the domain of gas pressure vessels is a testament to the intricate balance between cutting-edge technology and meticulous craftsmanship. It is through the lens of experience, supported by specialized expertise, that these vessels continue to serve as vital assets in multiple industries. Professionals equipped with authoritative knowledge and a track record of trustworthy practices are indispensable to advancing the stability and progress of gas pressure applications globally.