Navigating the intricate world of gas pressure vessels requires a blend of deep expertise and unwavering commitment to safety and innovation. These vessels, indispensable across various industries, including chemical manufacturing, oil and gas, and even food processing, are fundamental in storing and transporting gases under pressure. The construction and maintenance of these vessels necessitate not only engineering prowess but also a stringent adherence to international safety standards. This article seeks to provide an in-depth exploration of gas pressure vessels, from their types and materials used to the meticulous design and operation processes involved, thereby establishing a comprehensive understanding for industry professionals.
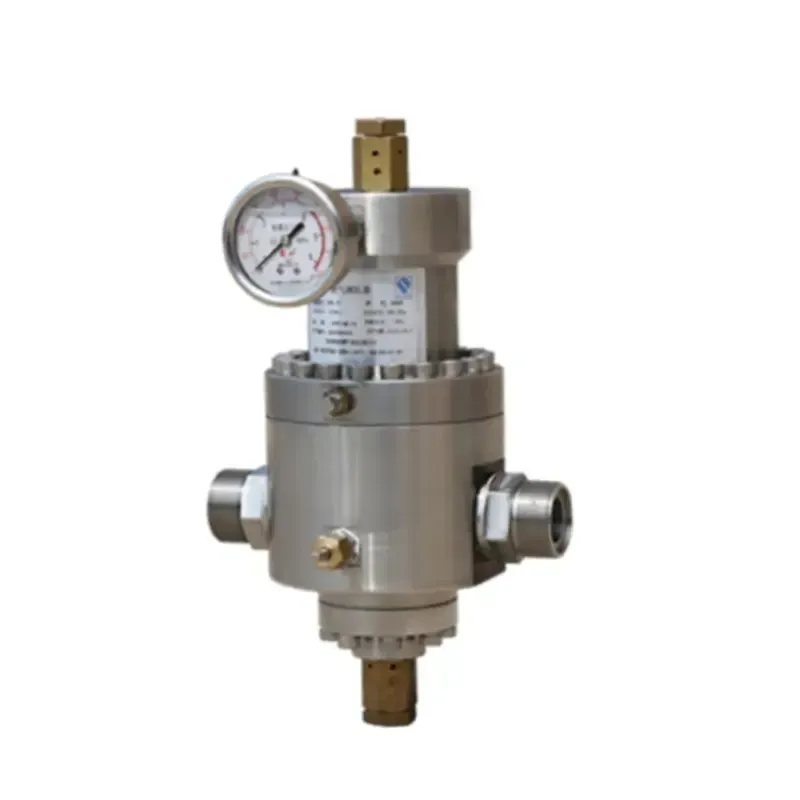
Gas pressure vessels are categorized primarily based on their construction and intended application. Among the most common types are the cylindrical pressure vessels, which are favored for their ease of manufacturing and uniform stress distribution. Spherical vessels, albeit more expensive, offer superior strength, making them ideal for high-pressure applications. The choice between these types often hinges on an intricate balance of cost, space, and pressure requirements, factors which professionals must judiciously evaluate.
Material selection for gas pressure vessels plays a pivotal role in their performance and longevity. Steel, particularly stainless steel and carbon steel, is a popular choice due to its robustness and resistance to pressure-induced stress and corrosion. In environments where chemical reactions pose a significant risk, the use of composite materials and advanced alloys becomes necessary. Each of these materials has distinct properties that must be matched to the vessel’s operational demands to prevent structural failure and ensure safety.
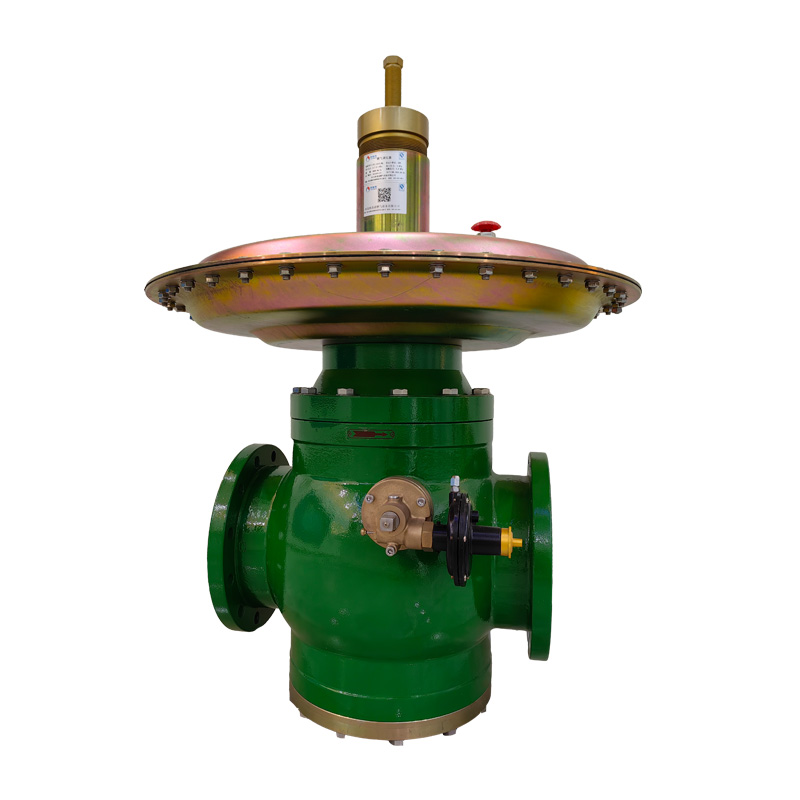
The design phase of a gas pressure vessel is arguably the most critical stage, demanding precision engineering and compliance with codes like the ASME Boiler and Pressure Vessel Code. This involves complex calculations to determine wall thickness, shape, and size, ensuring that the vessel can withstand the intended pressure without deforming or rupturing. Advanced finite element analysis (FEA) software is often employed to simulate various stress conditions, enabling engineers to validate their designs against potential failure scenarios.
gas pressure vessel
Manufacturing these vessels involves cutting-edge technology and precision engineering. Automated welding techniques, such as TIG (tungsten inert gas) welding, are commonly used to ensure robust joints that can withstand high-pressure conditions. Post-manufacture, non-destructive testing (NDT) methods, including ultrasonic testing and radiography, are crucial to ascertain the structural integrity of the vessels. These rigorous processes attest to the importance of expertise and reliability in the field.
Operation and maintenance of gas pressure vessels demand a strict regime to mitigate risks associated with pressure and hazardous materials. Regular inspections are mandated to check for signs of corrosion or fatigue, which could compromise safety. Additionally, the training of operators to handle these vessels safely and efficiently is paramount, underscoring the importance of a culture of safety and continuous education in industrial settings.
The authoritative presence of regulatory bodies further assures the safety and effectiveness of gas pressure vessels. Compliance with international standards such as ISO and adherence to national regulations fortify the credibility of manufacturers and users alike. This regulatory framework not only drives the industry towards innovation and safety but also reinforces public trust in these essential industrial components.
In conclusion, the realm of gas pressure vessels is a testament to the confluence of engineering excellence, meticulous operational standards, and regulatory compliance. For professionals in this field, possessing a comprehensive understanding of the types, materials, design protocols, and safety measures associated with these vessels elevates both their expertise and their organization’s image. It also serves as a continual reminder of the industry’s overarching commitment to safety, reliability, and technological advancement. As the demand for efficient gas storage solutions rises, the journey of innovation in gas pressure vessel technology will undoubtedly continue, driven by dedicated professionals committed to upholding the highest standards of experience, expertise, authority, and trust.