For professionals in the gas industry or individuals who handle gases regularly, the significance of a reliable gas regulator cannot be overstated. A gas regulator is a vital component used to manage pressure levels from high-pressure gas cylinders to a suitable level for various applications. Having the right gas regulator ensures efficiency, safety, and cost-effectiveness, making it an indispensable tool for anyone dealing with gases.
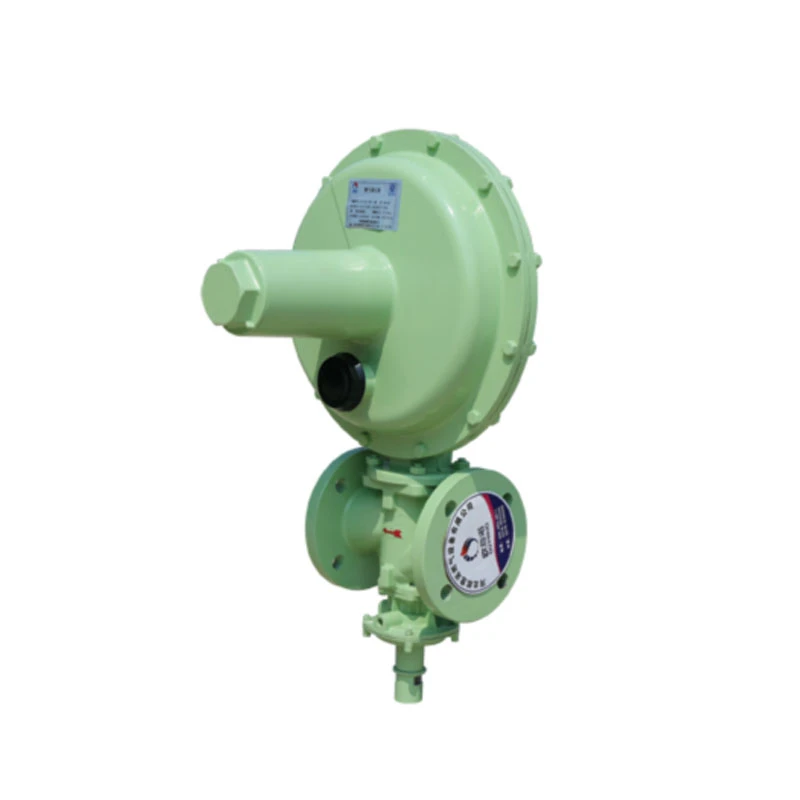
Expertise underscores the crucial role gas regulators play in myriad applications, from medical to industrial and culinary uses. In industries such as welding, fabrication, and biochemical laboratories, precise pressure control is fundamental. An ideal gas regulator is designed to handle the specific characteristics of different gases, such as oxygen, acetylene, or hydrogen, each demanding unique handling protocols. Industry veterans understand that a misstep in selecting the correct regulator could lead to significant safety hazards or compromised project outcomes. Thus, familiarity with the technical specifications such as flow capacity, inlet and outlet pressure, and material compatibility is paramount.
Authoritativeness lies in understanding the manufacturers and types of gas regulators suitable for specific tasks. Leaders such as Harris, Fisher, and Victor have established themselves over decades as providers of top-tier gas regulation solutions. Their products feature advanced technology that assures users of both safety and efficiency. For instance, two-stage regulators, known for maintaining consistent flow despite fluctuating inlet pressure, are preferable in scenarios requiring unwavering precision—an essential trait for laboratory settings.
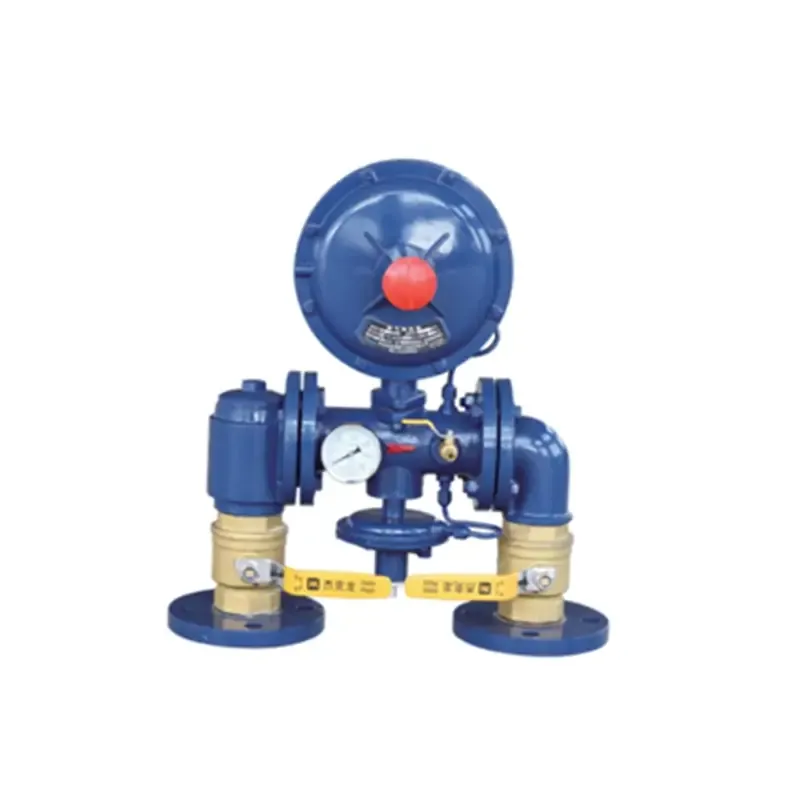
Furthermore, trustworthiness is a crucial factor when selecting a gas regulator. It involves not only the brand reputation but also compliance with industry standards and certifications, which is a testament to the product's reliability and safety. Standards such as those set by the Compressed Gas Association (CGA) and the Occupational Safety and Health Administration (OSHA) highlight the guidelines that ensure both effective performance and safety. Users should ensure their chosen gas regulator meets or exceeds these standards to bypass potential hazards and operational downfalls.
gas regulator
Experience is invaluable when it comes to selecting the right gas regulator. Experienced users consistently emphasize the importance of understanding the operating environment to ensure the regulator’s materials can withstand potential corrosive interactions with specific gases. For example, regulators made from brass are ideal for low to medium corrosive gases, whereas stainless steel regulators might be necessary for highly corrosive or toxic gases. Learning from others who have a wealth of knowledge about these tools typically results in fewer operational issues and a smoother work process.
The precision engineered into the design of gas regulators significantly affects their longevity and adaptability in various conditions. Features such as pressure relief devices,
gauges, and durable diaphragms enhance both the safety and usability of the regulator. With continuous advancements in technology and materials, modern regulators are becoming more compact while maintaining essential service parameters, offering users considerable versatility and ease of use.
In conclusion, the importance of choosing an appropriate gas regulator cannot be understated for those whose work or projects involve gases. The right selection not only assures safety and precision but also reinforces efficiency and reliability across diverse applications. As technology continues to evolve, staying informed about the latest developments and leveraging professional resources will empower users to make informed decisions that prioritize safety, expertise, and performance. Understanding and applying these principles ensures that users maximize both their investment and operational outcomes.