Whether you're dealing with a small domestic boiler or an industrial-sized heating system, ensuring the safety and reliability of gas systems is paramount. One crucial component in this safety matrix is the gas safety relief valve. As a cornerstone of gas safety engineering, this valve plays a vital role that requires profound understanding, proper maintenance, and regular checks.
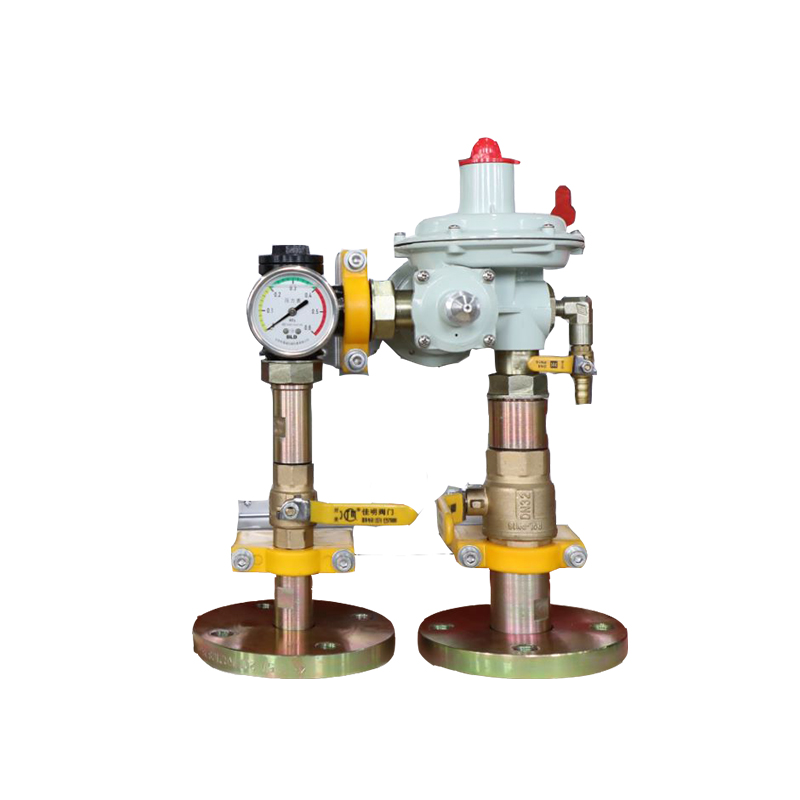
Drawing from years of experience in mechanical engineering and industries reliant on gas systems, I emphasize that the gas safety relief valve is not merely a component but a guardian of operation integrity. The relief valve acts as a fail-safe mechanism designed to release excess pressure from a system, thereby preventing potential overpressure scenarios that could lead to catastrophic failures. Imagine an orchestra conductor preventing a symphony from spiraling into chaos; a safety relief valve functions similarly, ensuring harmonious operations within a system’s pressure limits.
A well-selected safety relief valve must match the specific operational parameters of your system. This selection process involves understanding factors such as pressure and temperature ratings, material compatibility, and flow capacity. Expertise in thermodynamics and fluid mechanics is crucial since these valves must operate precisely under predefined conditions to avert risks. An inappropriate valve choice can result in either performance inefficiency or a safety hazard, both of which could lead to costly downtimes or, worse, accidents.
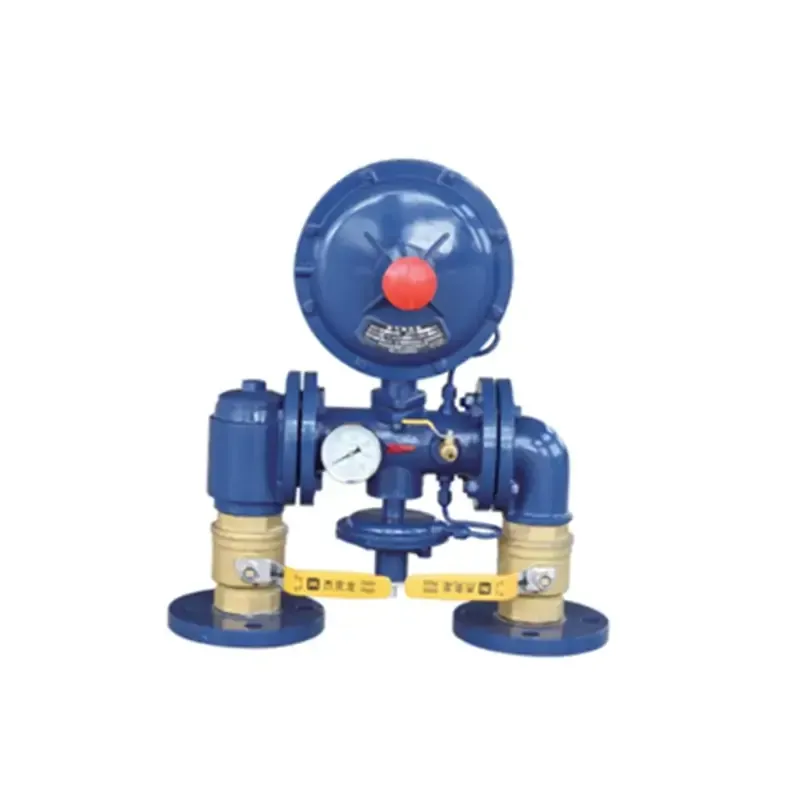
From my expertise, one noticeable trend is manufacturers' increasing use of high-grade materials and innovative coatings in valve production to enhance durability and resistance to harsh environmental conditions. These advancements underscore the necessity of choosing valves from reputable manufacturers that comply with stringent industry standards such as API, ASME, and ISO certifications. These standards are not just bureaucratic boxes to tick; they are assurances of quality, reliability, and safety.
Hands-on experience in the field has shown me that installation and maintenance are as critical as the valve's quality. A valve must be installed correctly, with attention to the orientation and position that ensures optimal operation. Regular inspections are non-negotiable; they help in identifying wear and tear or corrosion that, if left unchecked, might compromise the valve's efficiency.
gas safety relief valve
Moreover, operators must remain vigilant and educated about their systems. Training in the specific dynamics of gas safety relief valves can empower operators to make informed decisions, reducing reliance solely on external experts. This builds trust within the team and assures continuous, sound operation of gas systems.
Building on authoritativeness, integrating IoT technologies with gas safety relief valves has proved transformative. From remote pressure monitoring via sensors to advanced data analytics predicting wear patterns, technology ensures proactive maintenance and highlights irregularities before they escalate into problems. Companies that leverage such technology not only safeguard their operations but also enhance their reputation as industry leaders committed to state-of-the-art safety standards.
Trustworthiness extends beyond the operations to customer perceptions. Businesses must be transparent about their safety protocols and actively communicate the measures they take to prevent incidents. This transparency fosters trust and can be a decisive factor for clients searching for partners who prioritize safety as much as performance.
Finally, let us remember that while a gas safety relief valve is a hero in pressured environments, it works in concert with other components of a gas safety system. It is the harmony of these parts – burners, pipelines, and regulators – that defines the safety of gas-powered operations.
In conclusion, the gas safety relief valve is more than just a part. It embodies a critical blend of expertise, reliability, and industry commitment. Through strategic selection, regular maintenance, technological integration, and transparent practices, it remains a vital protector of safety, efficiency, and trust in the ever-evolving landscape of gas system operations.