Gas safety relief valves are integral components in various industrial applications, providing a critical function that safeguards systems against excessive pressure build-up. Their primary role is to maintain safety by venting gases and preventing potential hazards such as explosions or equipment damage. An in-depth understanding of these valves, their design, functionality, and advantages, along with real-world applications, establishes a comprehensive knowledge base for industry professionals and contributes to their effective utilization.
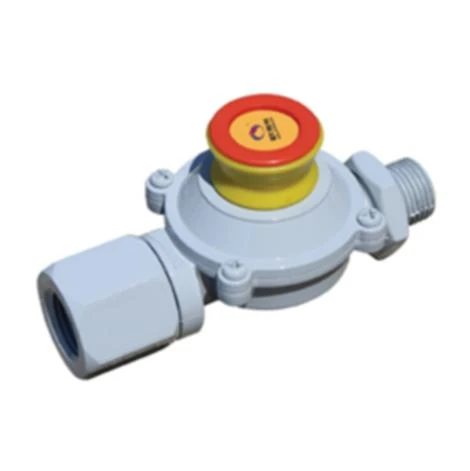
The design of gas safety relief valves is rooted in engineering precision and material excellence. Typically constructed from robust materials such as stainless steel or brass, these valves are engineered to withstand harsh operating environments and resist corrosion. Such resilience ensures long-term reliability even when exposed to chemically aggressive gases or fluctuating temperatures. The design includes a spring-loaded mechanism that responds to pressure changes, allowing the valve to open at a predetermined set pressure, vent the excess gas, and subsequently reseal to maintain system integrity.
In the realm of expertise, selecting the appropriate gas safety relief valve necessitates an understanding of specific system requirements. Factors such as the type of gas,
system pressure, temperature range, and flow capacity are pivotal in determining the most suitable valve type. For instance, a valve designed for a natural gas pipeline will differ significantly from one used in a chemical processing plant due to the variance in governing safety standards and operational conditions.
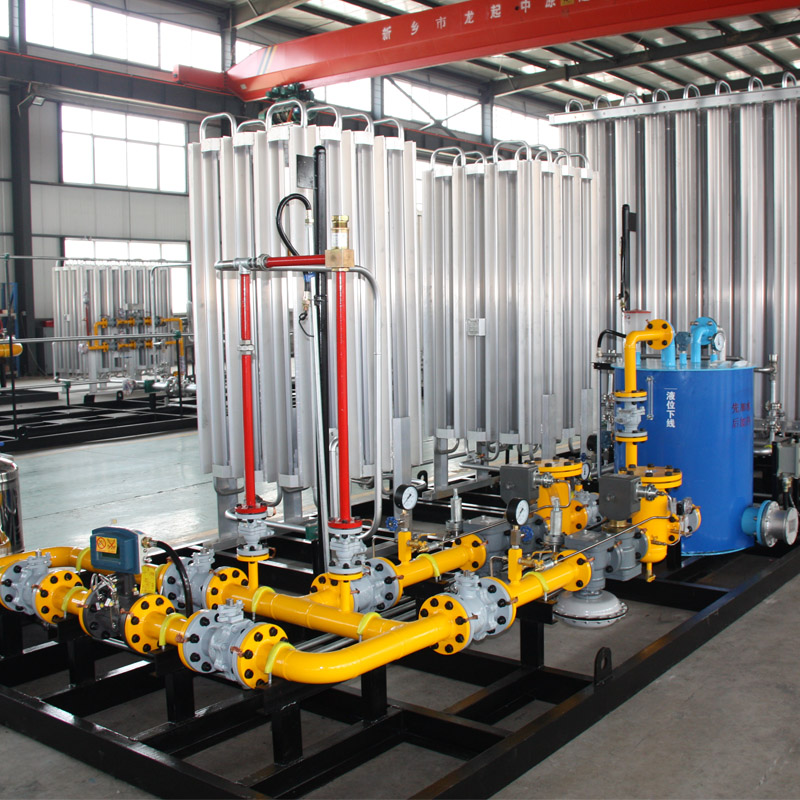
Authoritativeness in the field of gas safety relief valves is reinforced by conforming to internationally recognized standards and specifications. Organizations like the American Society of Mechanical Engineers (ASME) and the International Organization for Standardization (ISO) provide comprehensive guidelines that outline performance criteria, testing methods, and safety requirements. Valves adhering to these standards are subject to rigorous testing, ensuring they deliver optimal performance and reliability.
gas safety relief valve
Real-world experience underscores the importance of regular maintenance and testing as a part of a broader safety strategy. Maintenance protocols often include routine inspections, cleaning of components, calibration of set pressures, and functional testing to preemptively identify potential failures. Industries that prioritize maintenance are more likely to avoid costly downtimes and ensure operational continuity. Moreover, training personnel to effectively manage and operate these valves adds an additional layer of safety and efficacy.
The trustworthiness of gas safety relief valves is also reflected in the transparency and documentation provided by manufacturers. Datasheets that detail performance characteristics, flow curves, and installation instructions are indispensable resources. Additionally, traceability features such as unique serial numbers and manufacturing batch records are essential for quality assurance and post-installation support.
Innovation in valve technology continues to enhance their applications, offering advanced features such as remote monitoring and control capabilities. Integration with digital systems allows operators to receive real-time data on valve performance, enabling predictive maintenance and instantaneous response to changing system conditions. Such advancements not only improve safety margins but also contribute to efficiency and cost-effectiveness in industrial operations.
In conclusion, gas safety relief valves are pivotal in ensuring the safety and efficiency of pressure systems across various industries. Their selection and application require a balance of technical knowledge, adherence to standards, and commitment to maintenance. By leveraging these elements, industries can safeguard their operations, protect their workforce, and maintain compliance with safety regulations. For professionals involved in system design, installation, or maintenance, understanding the intricacies of these valves is essential for enhancing operational safety and reliability.