Gas safety relief valves are crucial components in numerous industrial and residential systems, serving a pivotal role in preserving safety and efficiency. These devices are engineered to protect pressurized systems from the potential hazards posed by overpressure, which could lead to equipment failure, environmental harm, or even catastrophic explosions. As someone with in-depth experience and expertise in this niche, let us delve into the significance, workings, and selection criteria of gas safety relief valves, ensuring you make informed decisions regarding their implementation.
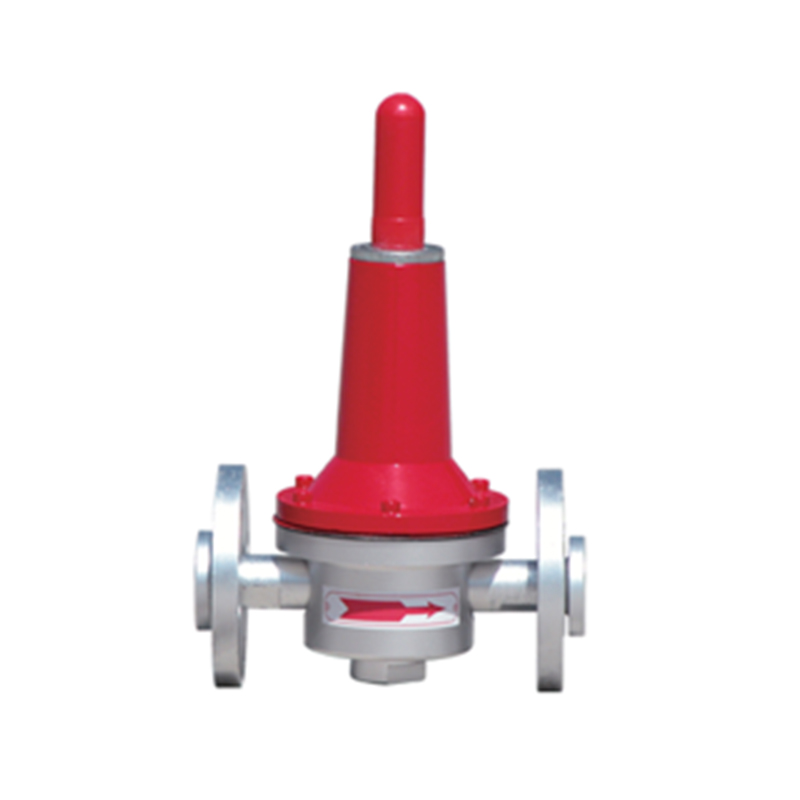
Gas safety relief valves operate on a simple yet highly effective principle they provide a controlled pathway for excess pressure to escape, thereby preventing pressure buildup that might compromise system integrity. This escape pathway is typically achieved by a spring-loaded or pilot-operated mechanism that opens when the internal pressure reaches a predetermined set-point. Once the pressure normalizes, the valve reseats, maintaining system pressure at safe levels. The precision and reliability of these valves are paramount, as any malfunction can pose significant risks.
When selecting a gas safety relief valve, a myriad array of factors must be considered to ensure optimum performance and safety. One of the primary considerations is the set pressure, which must be accurately aligned with the operational parameters of the system. A valve designed with an improper set pressure can cause either premature activation or delayed response, both of which can lead to safety hazards or operational inefficiencies. It's imperative for the selected valve to have certifications from recognized standards organizations such as the American Society of Mechanical Engineers (ASME), which guarantees compliance with stringent safety regulations.
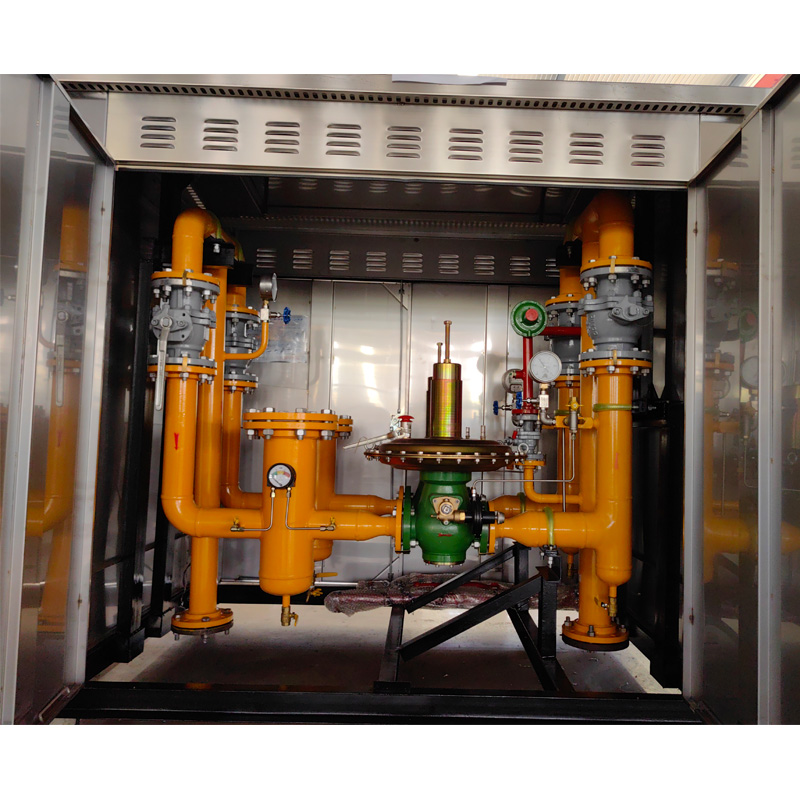
Additionally,
the material of construction is a critical determinant in the durability and reliability of the valve. Common materials include stainless steel, brass, and various high-performance alloys, each offering distinct advantages depending on the application's chemical compatibility and temperature requirements. For high-corrosion environments, stainless steel or specialized alloys may be preferable. Furthermore, the valve's orifice size and flow capacity should match the system's requirements for effective pressure relief under peak conditions.
gas safety relief valve
Regular maintenance and testing of gas safety relief valves are integral to sustaining their functionality over time. As part of a preventative maintenance program, valves should be periodically inspected for signs of wear, corrosion, or blockage. Routine testing, which might involve bench testing or inline testing methods, ensures that the valve activates at the designated set pressure and reseats correctly. Engaging with qualified technicians for maintenance can help in detecting potential issues before they escalate into failures.
The expertise and authoritative knowledge surrounding gas safety relief valves underscore their critical role in safeguarding systems. These components not only protect equipment and environments but also provide peace of mind by ensuring compliance with regulatory standards and mitigating the risks associated with pressurized gases. Drawing on expert guidance and trustworthy sources when selecting and maintaining these valves is essential to achieving long-term safety and operational efficiency.
For businesses and individuals alike, the benefits of a well-chosen and properly maintained gas safety relief valve extend beyond mere compliance. They represent a commitment to safety, reliability, and operational excellence, reinforcing trust with stakeholders and preventing the costly consequences of system failures. In an environment where safety standards and technological advancements continue to evolve, staying informed and vigilant about gas safety relief valve technology can make all the difference in securing a safe and efficient future.