Gas valves are quintessential components in various applications, from domestic to industrial settings. These devices control the flow of gas in a system, ensuring safety and efficiency. Whether you're a technician, homeowner, or industry professional, understanding gas valves' intricacies can enhance your operational knowledge and decision-making capabilities.
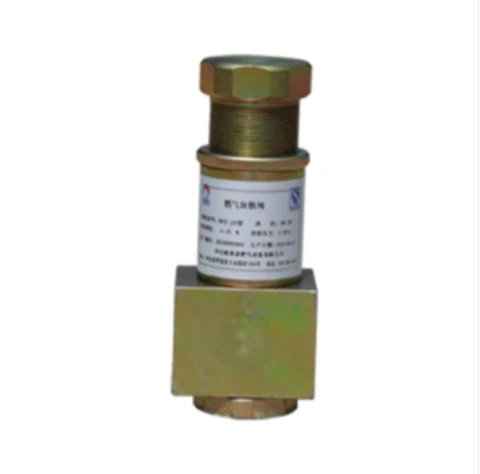
Different types of gas valves serve distinct purposes.
For residential settings, you often encounter ball valves or butterfly valves. Ball valves are appreciated for their excellent sealing properties, achieved through a spherical element. Their durability and reliability make them a preferred choice for natural gas lines in homes. On the other hand, butterfly valves are more suitable for larger pipes and are praised for their quick shut-off capabilities while being lightweight and cost-effective.
Industrial applications often utilize globe valves, gate valves, and control valves. Globe valves, known for their throttling ability, are great for applications requiring tight sealing and flow regulation. Gate valves, however, are ideal for applications where infrequent operation is necessary. These valves are designed to function in either an open or closed position, minimizing pressure loss when fully open. Control valves, equipped with actuators and positioners, are indispensable in automated systems where precise control over flow rate is necessary.
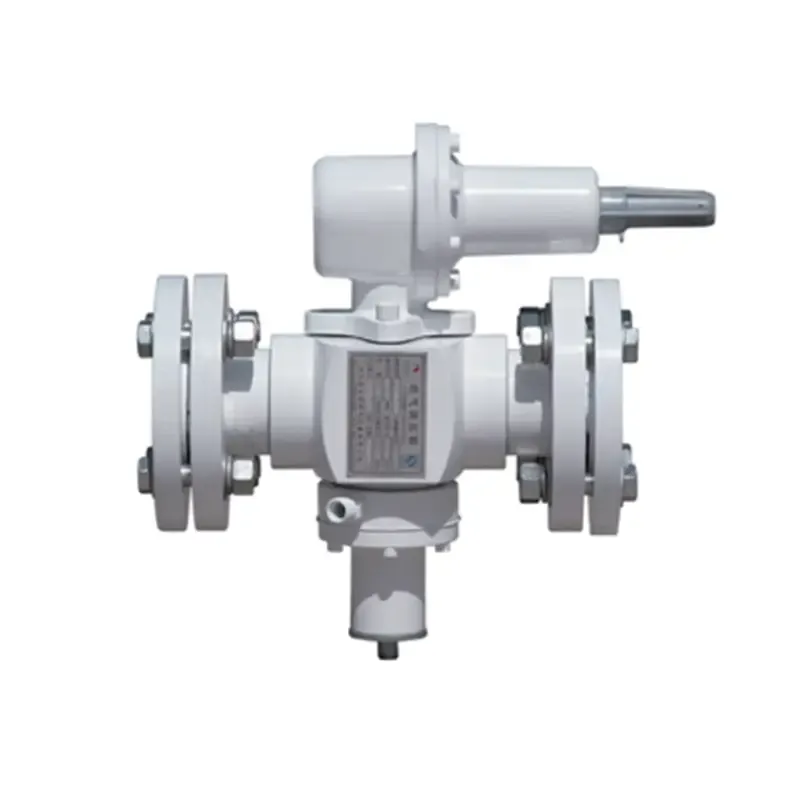
The importance of material selection for gas valves cannot be overstated. Materials like brass, stainless steel, and cast iron are common choices. Brass valves are favored for their corrosion resistance and suitability for low-pressure applications. Stainless steel valves offer superior strength and corrosion resistance, ideal for high-pressure industrial environments or where the gas composition might be reactive. Cast iron valves are less expensive and provide good performance for non-critical systems.
Installation and maintenance significantly affect a gas valve's performance and lifespan. Proper installation requires adherence to the manufacturer's specifications and local safety standards to prevent leaks and ensure efficient operation. Regular maintenance, such as checking for leaks, lubricating moving parts, and ensuring connections remain tight, is crucial for safety and longevity. Furthermore, technicians should be trained to recognize signs of wear or damage, such as corrosion or unusual noises, to preemptively address issues before they escalate.
gas valve
Technological advancements have propelled gas valve capabilities beyond traditional designs. Smart gas valves have emerged, equipped with sensors and connectivity features, allowing for real-time monitoring and control through mobile devices. This innovation not only enhances convenience but also augments safety by enabling immediate response to anomalies or leak detections.
Safety considerations for gas valves are paramount. Properly functioning valves help mitigate risks such as leaks, which can lead to explosive hazards. Using quality valves that meet standards like ANSI or ISO ensures they have been tested for performance and safety under various conditions. Additionally, operators must be aware of the environment where the valve will be used, considering factors like temperature and the chemical nature of the gas.
As industries and technologies evolve, the role of gas valves continues to expand, making them integral for energy efficiency, safety, and operational excellence. Professionals and enthusiasts must stay informed about the latest developments, standards, and best practices to ensure the optimal functioning of these vital components.
In conclusion, gas valves play a crucial role across numerous applications, demanding expertise and diligence in their selection, installation, and maintenance. Whether leveraging the advantages of smart technology or relying on traditional designs, ensuring the right valve is in place can enhance safety, performance, and efficiency, attesting to the valve's authoritative place in modern systems.