The significance of a gas valve in both residential and industrial settings cannot be overstated. This critical component is pivotal in managing the flow and pressure of gas, ensuring safety and efficiency in gas-powered systems. Whether it’s the burner in your kitchen or an industrial furnace, gas valves play a crucial role in various applications, and selecting the right type is imperative.

Understanding gas valves begin with recognizing their key functions and types. Primarily, gas valves are used to start, stop, or throttle the flow of gas. The most common types of gas valves include ball valves, butterfly valves, globe valves, plug valves, and gate valves. Each type serves specific purposes and is chosen based on factors such as the nature of the gas, pressure requirements, and operational environment.
Ball valves are renowned for their durability and long-lasting performance. They use a spherical disc to control gas flow, providing a reliable option for shut-off applications. Their main advantage lies in their ability to open and close rapidly, making them suitable for emergency applications where quick disruption of gas flow is required.
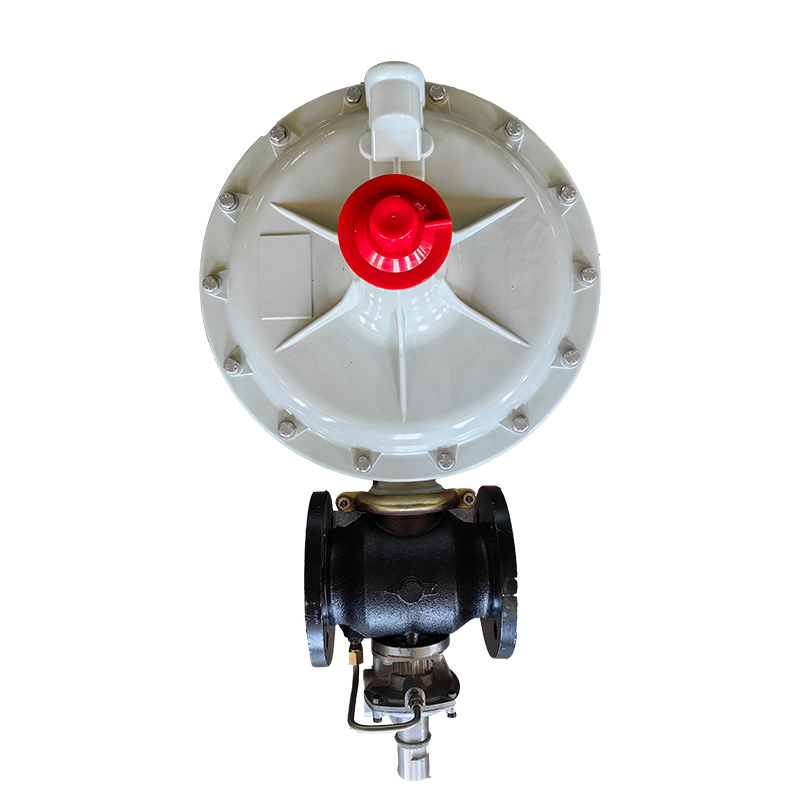
Butterfly valves are another prevalent type, known for their cost-effectiveness and ease of operation. They consist of a rotating disc for controlling flow and are ideal for applications where space is a constraint. Their lightweight and compact design make them an attractive option for many industries.
Globe valves, on the other hand, are typically used in throttling applications. Their design allows for precise flow regulation, which is critical in applications requiring specific flow rates. Although they present a higher pressure drop compared to other valves due to their tortuous path, their ability to finely control gas flow makes them indispensable in chemical and oil industries.
gas valve
In industrial settings, the choice of a gas valve must also account for the type of gas being used. Valves must be compatible with the gas to prevent corrosion and degradation. For instance, oxygen gas valves are often made from materials that minimize the risk of sparks, such as brass or stainless steel, to prevent fire hazards.
Furthermore, gas valves must be selected considering their operational environment. High-pressure settings necessitate valves designed to withstand extreme conditions and pressures. In such scenarios, valves must be constructed from high-strength materials that prevent leaks and ensure durability.
Installing gas valves requires a high degree of expertise and adherence to safety standards. Proper installation ensures optimal performance and mitigates the risk of gas leaks. This process includes the correct choice of valve size, material, and pressure rating suitable for the specific applications. Moreover, regular maintenance is essential to retain the valve’s functionality, including periodic inspections and cleaning to prevent blockage and wear over time.
Trustworthiness in gas valve products is significantly enhanced by obtaining them from reputable manufacturers known for quality and reliability. Renowned manufacturers provide certifications that comply with industry standards, such as ISO and ASME, offering additional assurance of product safety and performance.
In conclusion, understanding the nuances of gas valves, from types and materials to installation and maintenance, enhances the safety, efficiency, and longevity of gas systems. Selecting the right valve involves careful consideration of the environment, pressure requirements, and gas compatibility. Reliable manufacturers, continuous education about valve technology advancements, and stringent adherence to safety protocols ensure that these components perform optimally, safeguarding both user and infrastructure. As technologies evolve, keeping abreast with the latest developments and innovations in gas valve technology will secure the steadfast operation of gas-powered systems well into the future.