In the realm of industrial and domestic applications, the heat exchanger emerges as an unsung hero, playing a crucial role in thermal management. From ensuring that your air conditioning units run efficiently to enabling complex industrial processes, these marvels of engineering maintain the delicate balance of temperature regulation.
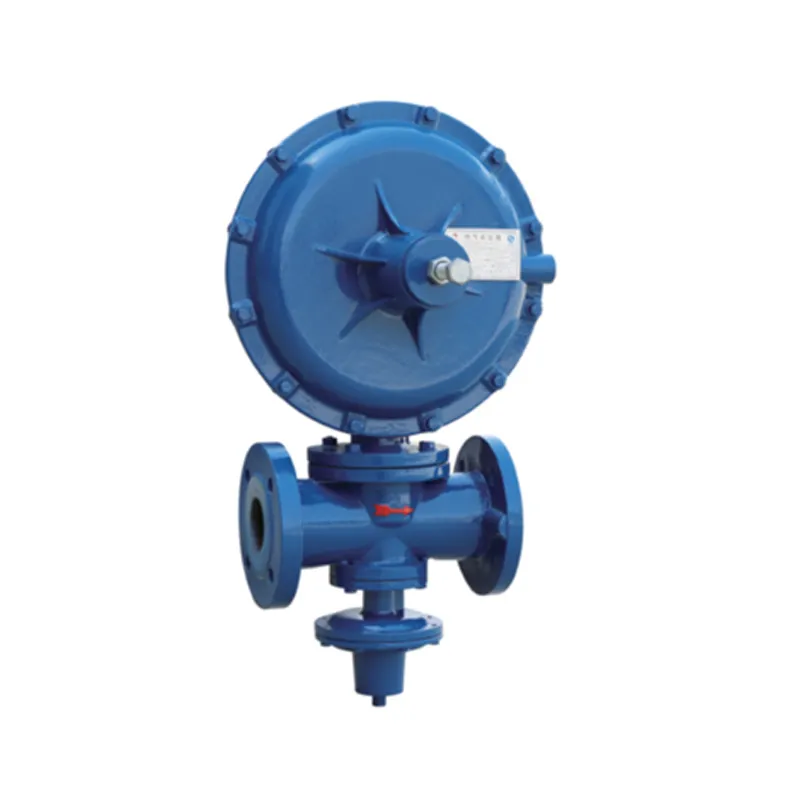
Heat exchangers work on a simple yet ingenious principle transferring heat from one medium to another without the two coming into direct contact. This concept allows them to support various systems, from cooling refrigerants in HVAC systems to recovering waste heat in power plants. Take, for instance, the shell and tube heat exchangers, a design that has stood the test of time due to its durability and efficacy. It comprises a series of tubes, one set housed within another, which facilitates effective heat transfer between fluids.
For those seeking to maximize efficiency and minimize environmental impact, plate heat exchangers present a compelling option. Their compact design and increased surface area allow for better heat transfer, requiring less energy than traditional systems. This design is an asset in industries where space and energy efficiency are paramount, such as in the food processing and chemical industries.
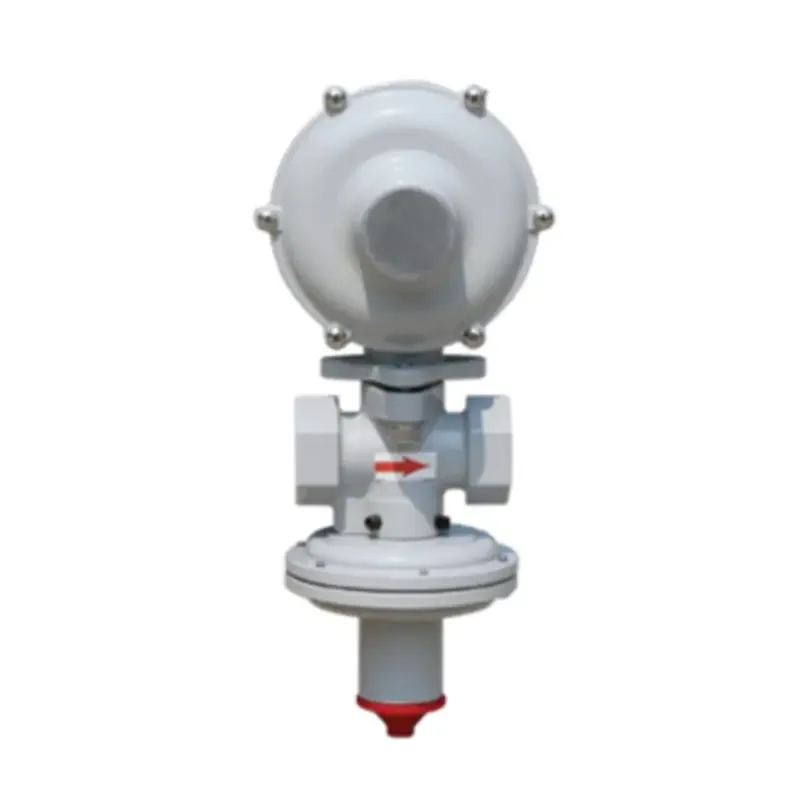
Selecting the right heat exchanger involves nuanced expertise. Material compatibility is paramount, ensuring that the device can withstand the corrosive nature of the fluids it handles. Engineers must consider factors such as thermal conductivity, cost, and long-term durability. Stainless steel and titanium, for example, provide excellent resistance against corrosion while ensuring efficient thermal conductivity—qualities that underscore the trustworthiness of these materials in severe environments.
heat exchanger
Another critical consideration is maintenance. A well-maintained heat exchanger can dramatically extend its lifespan and efficiency. Routine checks for fouling, which can impede heat transfer, are vital. This might involve regular cleaning and inspection to ensure optimal performance and prevent unscheduled downtimes.
The technological advancement in heat exchangers is also noteworthy. Innovations like microchannel technology and the development of more resilient composites demonstrate an industry moving towards smarter, more sustainable solutions. These advancements not only enhance the expertise behind their manufacturing but also instill confidence in consumers regarding their reliability and efficiency.
When assessing the credibility and trustworthiness of heat exchangers, the certifications they hold play a significant role. Adherence to international standards like ASME and ISO not only reflects a commitment to quality but also ensures that the product can be trusted to perform under specified conditions. Moreover, manufacturers with a long-standing reputation for excellence provide an added layer of assurance regarding product quality.
In conclusion, a heat exchanger's significance transcends its mere functionality. It embodies a sophisticated integration of experience, expertise, and innovation—attributes vital for fulfilling the growing demands for energy efficiency and environmental sustainability. Engaging with reputable manufacturers and prioritizing regular maintenance will ensure these systems operate at peak performance, thus delivering reliable and efficient solutions to meet modern challenges.