Heat exchangers are essential components in a vast array of industries, including automotive, chemical processing, power generation, HVAC, and more. Their primary function is to transfer heat efficiently from one medium to another, facilitating processes such as heating or cooling. With the ever-increasing demand for energy efficiency and sustainability, the role of heat exchangers has never been more critical.
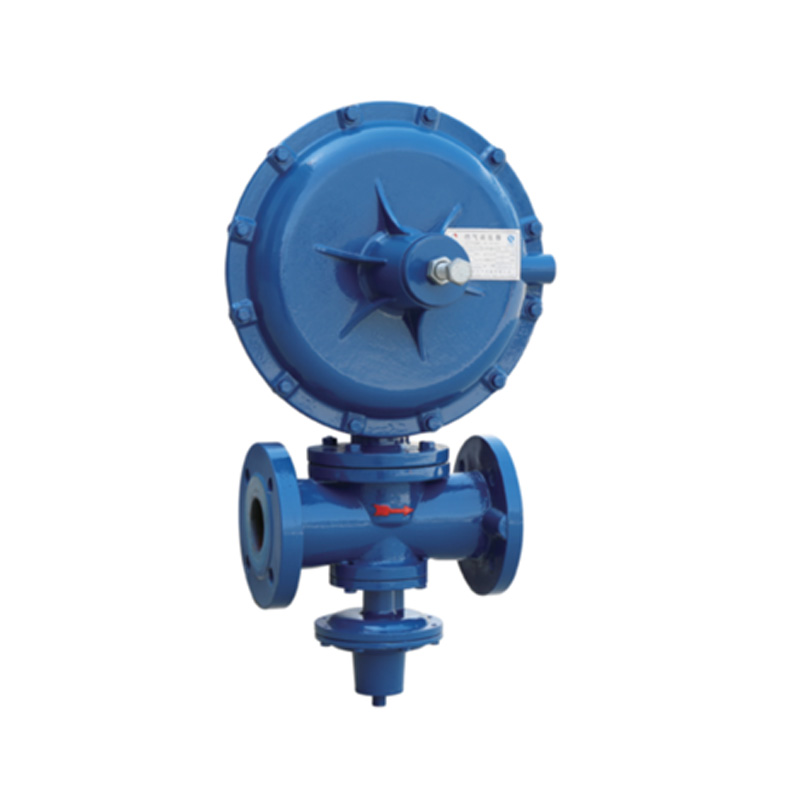
One of the most innovative advancements in the realm of heat exchangers is the development of microchannel technology. These exchangers are designed with parallel microchannels that enhance thermal performance while significantly reducing material weight and volume. This technology is particularly beneficial in automotive and HVAC systems where space and energy efficiency are paramount.
Through decades of evolution, different types of heat exchangers have been optimized for specific industry needs. Among the most common are shell and tube, plate,
and air-cooled exchangers. Each type caters to distinctive operational conditions, involving factors like pressure levels, temperature variances, and fluid types.
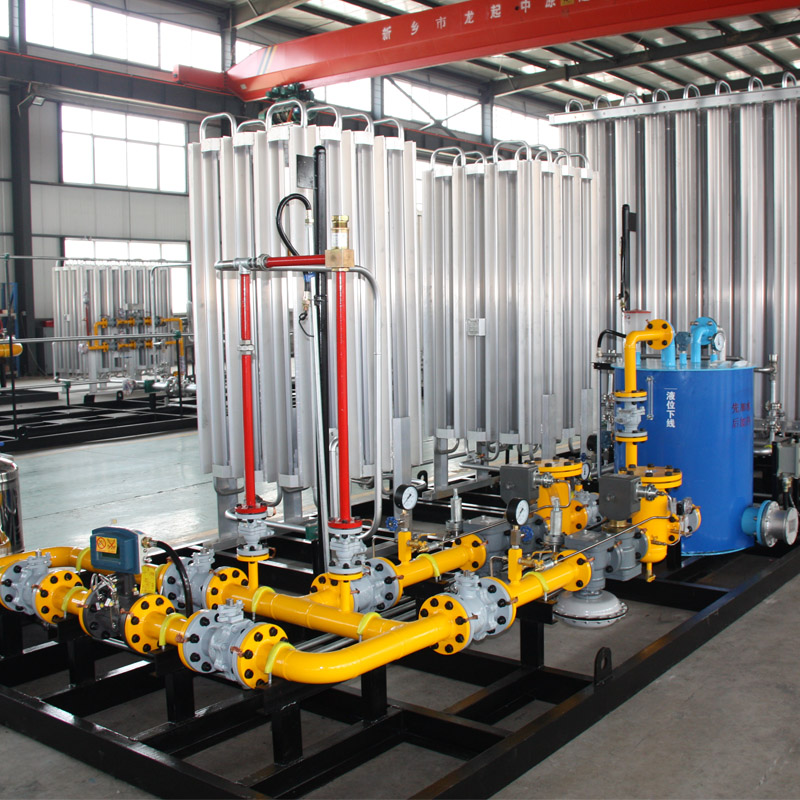
1. Shell and Tube Heat Exchangers
These devices dominate the industry due to their versatility and robust design. Constructed with a series of tubes, they enable efficient heat transfer between fluids at different temperatures and pressures. Known for their durability, shell and tube exchangers are utilized in high-pressure applications such as oil refineries and chemical processes. However, they require regular maintenance to prevent fouling and ensure optimal performance.
2. Plate Heat Exchangers
Recognized for their compact size and ability to handle varying temperature ranges, plate heat exchangers consist of multiple thin, slightly separated plates. They excel in applications involving lower pressures, such as food processing and pharmaceutical production. Their ease of dismantling and cleaning makes them ideal for industries that require strict hygiene standards.
3. Air-Cooled Heat Exchangers
These units are quintessential in industries where water conservation is a priority. By employing atmospheric air as a cooling medium, they eliminate the need for water resources. Their environmental benefits are particularly advantageous in regions with limited water availability. Despite their dependence on air temperature, advancements in fan technology have improved their efficiency in recent years.
heat exchanger
Energy conservation has become a pivotal focus in the development of modern heat exchangers. Recent innovations prioritize the use of advanced materials like ceramics and composites that withstand extreme conditions while maintaining high thermal conductivity. Additionally, the integration of digital monitoring systems in heat exchangers allows for real-time diagnostics and performance optimization, significantly reducing downtime and maintenance costs.
A critical consideration when selecting a heat exchanger is the fluid dynamics involved in the process. Understanding the viscosity, corrosiveness, and particulates within the fluids enables engineers to choose the appropriate exchanger type and material. Corrosion-resistant materials like stainless steel and titanium are often chosen for their durability in harsh chemical environments.
The expertise required to design and implement heat exchanger systems is substantial. Professionals in thermodynamics and fluid mechanics contribute to pioneering new designs that enhance energy exchange efficiency and reduce emissions. Collaboration between engineers and environmental scientists ensures that modern heat exchanger solutions meet global sustainability standards.
Establishing authority and trust in the market involves transparency and adherence to industry standards. Companies producing heat exchangers must comply with standards such as the American Society of Mechanical Engineers (ASME) and the International Organization for Standardization (ISO) specifications, which guarantee safety and operational efficiency.
To conclude, the landscape of heat exchangers is ever-evolving, driven by technological advancements and the global pursuit of sustainability. From miniaturized designs to eco-friendly materials, these devices are pivotal in addressing today's industrial challenges. The continuous innovation in heat exchanger technology not only enhances energy efficiency but also plays a vital role in minimizing environmental impact, securing their place as a cornerstone in industrial applications worldwide.