High pressure regulators play a crucial role in various industrial applications, guaranteeing that systems operate optimally and safely. Whether applied in gas distribution, chemical processing, or aerospace engineering, choosing the right high pressure regulator is indispensable for maintaining workflow efficiency and protecting sensitive equipment. This comprehensive guide will delve into the intricacies of high pressure regulators, offering insights from industry experts to guide both novices and seasoned professionals.
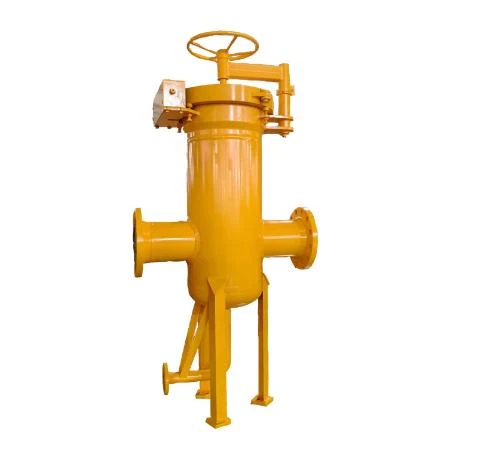
Industries across the globe rely on precision in pressure control, and as such, high pressure regulators are designed to meet these stringent requirements. These devices are not merely valves but sophisticated instruments engineered to manage the flow and maintain the safety standards necessary in high-pressure applications. They exemplify advanced technology integration, ensuring stability in operations where the margin for error is minimal.
Real-world experiences highlight the essential characteristics that define effective high pressure regulators. For instance, in a chemical plant where reactive substances are housed, any pressure imbalance could lead to catastrophic results. Hence, high pressure regulators must exhibit robust construction and precision engineering to withstand extreme conditions. Stainless steel is a frequently chosen material due to its resilience against corrosion and capability to withstand high temperatures and pressures.
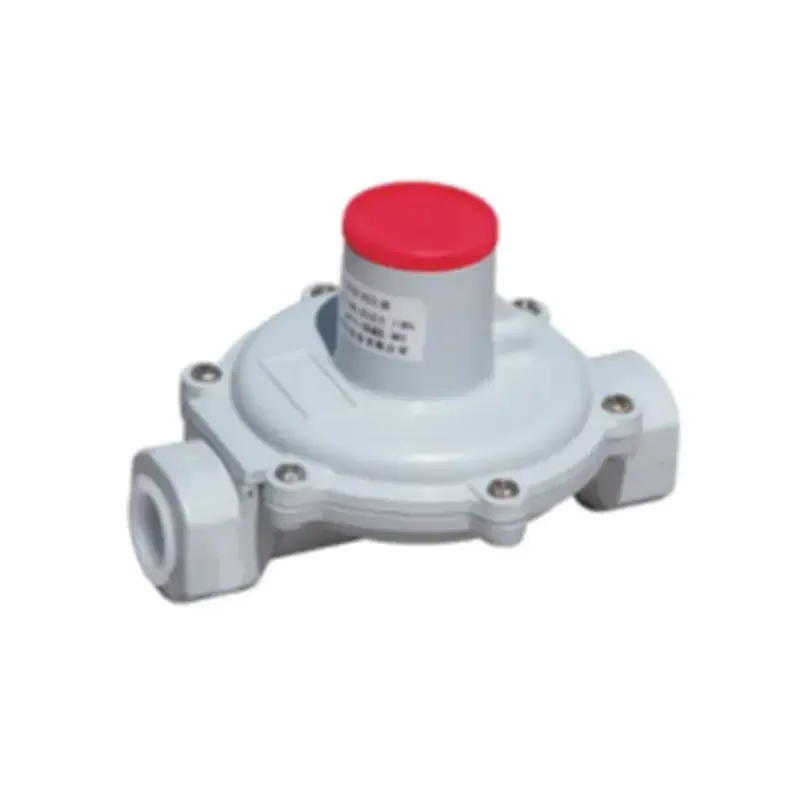
Experts in the field emphasize a deep understanding of flow dynamics and material compatibility. It is not merely about deploying a regulator that handles high pressure; it's about deploying one that harmonizes with the specific requirements of your system. This includes understanding the components within the system, such as pipes, end connectors, and where stress points may occur.
The authority of manufacturers is also paramount when selecting high pressure regulators. Brands with decades of innovation and production excellence regularly undergo rigorous testing and hold various certifications that attest to their legitimacy and trustworthiness. Regulatory certifications such as ISO 9001 for quality management systems or ASME standards ensure that these components have been scrutinized to meet industry mandates.
high pressure regulators
Installations, maintenance, and regular inspections are equally critical to maintaining pressure regulator performance. Technicians trained in the nuances of high pressure systems offer invaluable expertise. They not only install these regulators but also calibrate them regularly to adapt to changes in operation or system upgrades. Such diligence in maintenance prolongs the lifespans of these devices considerably.
Cases abound where improper application or poor quality high pressure regulators have led to significant operational hazards. Thus, investing in a high-quality pressure regulator yields savings by preventing downtime and reducing maintenance costs.
Expert advice strongly suggests integrating digital monitoring solutions with pressure regulators. These systems provide real-time data analytics, preemptively detecting potential malfunctions and ensuring rapid response times.
Trust in high pressure regulators is built upon performance repeatability and stability under duress. The relationship between technology, human expertise, and rigorous quality control measures cultivate this trust. When operations rely on these small but mighty regulators, choosing products supported by authoritative knowledge and proven industry standards becomes indispensable.
In conclusion, understanding the complex world of high pressure regulators equips industries to make informed decisions that prioritize safety, operational excellence, and economic efficiency. With proper integration, regular maintenance, and access to expert insights, these devices continue to play an integral role in ensuring industrial endeavors remain under control, both figuratively and literally.