Pneumatic control valves are integral components in the realm of process automation, serving as the heart of numerous industrial systems ranging from manufacturing to energy production. Their reliability and precision are critical for maintaining optimal system performance, making them indispensable tools for engineers and technicians committed to efficiency and safety.
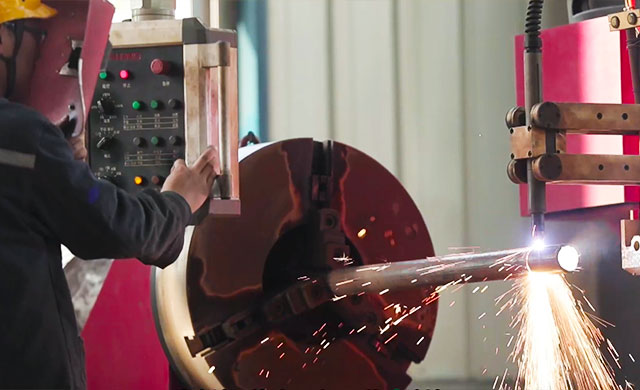
Experience in working with pneumatic control valves highlights the significance of understanding the subtle dynamics of airflow and pressure regulation. These valves function by converting compressed air into motion — either linear or rotary — to regulate the flow of various media, such as gas, steam, or liquid. The primary advantage here is their ability to provide precise control and fast response, a crucial factor in processes requiring stringent parameters for quality assurance.
From an expertise standpoint, pneumatic control valves offer diverse options tailored to specific operational needs. Butterfly valves, for instance, provide excellent on-off functionality and are perfect for low-pressure applications. Globe valves, in contrast, excel at regulating flow and maintaining a steady state, beneficial in nuanced process environments where precision is paramount. Choosing the right type of valve involves a thorough analysis of factors such as temperature, pressure, flow rate, and the nature of the media—a task best performed by seasoned engineers who understand the intricate workings of these systems.
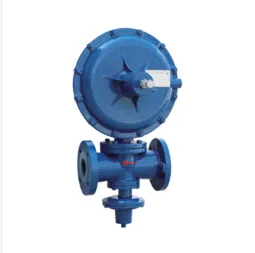
Authoritativeness in this field arises from the adoption of cutting-edge technologies and adherence to international standards. Manufacturers who align with organizations such as the International Society of Automation (ISA) or the American Society of Mechanical Engineers (ASME) assure clients of their commitment to quality. These standards often dictate the design, testing, and maintenance protocols for pneumatic control valves, ensuring they meet rigorous safety and operational criteria. By working closely with industry leaders, businesses can enhance their credibility and foster customer trust.
pneumatic control valve
Trustworthiness is built over years of delivering consistent performance and maintaining transparency with clients. Documenting case studies and real-world applications where pneumatic control valves have enhanced performance provides a testament to their reliability.
Technical support and after-sales service also play pivotal roles. A trusted provider will offer comprehensive service-level agreements (SLAs) covering routine maintenance, emergency repairs, and even custom calibration, thus minimizing downtime and maximizing productivity.
Understanding the interplay between product functionality and process demands is essential for maximizing the benefits of pneumatic control valves. Training sessions and workshops, often organized by manufacturers or industry bodies, furnish engineers with invaluable insights into the latest innovations and operational techniques. These educational endeavors are crucial for staying abreast of technological advancements that can enhance process efficiency and safety.
In conclusion, pneumatic control valves are more than mere components; they are pivotal to the success of industrial operations across the globe. Their adaptability and effectiveness lie in the hands of skilled professionals who leverage their expertise to ensure seamless integration and operation. As industries strive for greater efficiency and sustainability, the role of these valves will only continue to grow, underscoring their importance as a cornerstone of modern engineering solutions.