Regulating valves are critical components in various industrial applications, serving an essential function in controlling the flow and pressure of fluids within a system. These devices ensure process efficiency, safety, and reliability across diverse industries including oil and gas, pharmaceuticals, and water treatment. Understanding their operation, selection criteria, and maintenance is crucial for professionals who wish to optimize system performance and extend equipment life.
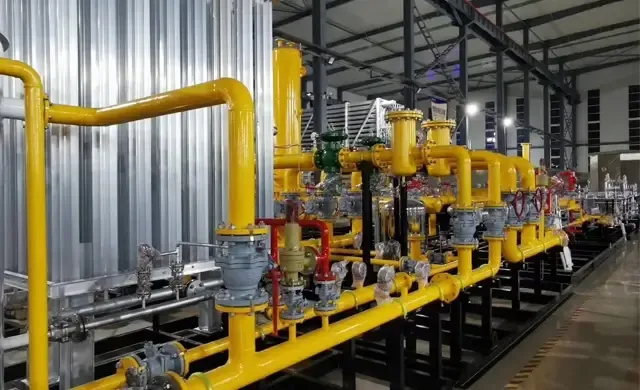
Experience plays a significant role in selecting the appropriate regulating valve for a given application. Industry veterans understand that choosing the wrong valve can lead to inefficiencies and system failures. Factors such as fluid characteristics, temperature, and pressure conditions must be considered. For example, corrosive fluids may require valves made from specialized materials like stainless steel or Teflon-lined options to prevent degradation and ensure longevity.
Professional expertise in regulating valves enhances not just selection but also implementation and maintenance. Technicians and engineers must comprehend valve mechanics, types, and their respective advantages. Common types include globe, butterfly, and ball valves, each suited to different applications. Globe valves, known for precise control, are ideal for throttling services. Butterfly valves, offering quick operation with a small footprint, suit large volume applications. Ball valves provide excellent durability and a tight seal, suitable for high-pressure environments.
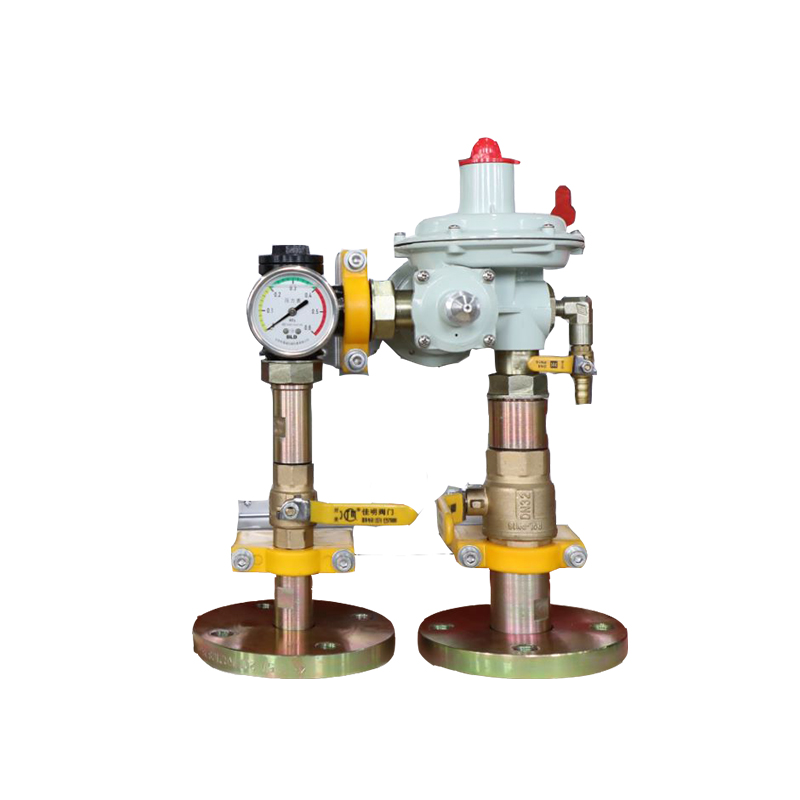
Authoritativeness in the field of regulating valves is supported by knowledge of industry standards and technological advancements. Compliance with standards such as ANSI/ISA, API, and ISO guarantees that valves meet necessary safety and performance benchmarks. Moreover, technological innovations like smart valve technology, which integrates sensors and actuators, offer real-time monitoring and adjustability, enhancing process control and reducing manual intervention.
Trustworthiness in valve management arises from rigorous testing and documentation practices. Organizations should conduct regular performance audits and maintain comprehensive records of valve specifications, operating conditions, and maintenance history. This approach minimizes downtime and supports proactive maintenance strategies, ensuring consistent performance.
regulating valve
Experts also highlight the importance of understanding the flow characteristics defined by the valve's inherent and installed flow curves. Knowing whether a valve possesses linear, equal percentage, or quick opening characteristics guides effective design and optimization of the control system.
Additionally, real-world experience emphasizes the value of flexibility and adaptability in valve operation. Industrial processes often evolve,
requiring valve adjustments or replacements. Selecting modular valves with replaceable components or those that can be easily retrofitted ensures long-term system compatibility and efficiency.
In terms of maintenance, seasoned professionals develop a comprehensive strategy that includes regular performance evaluation, cleaning, and component replacements. Predictive maintenance, supported by modern technologies such as vibration analysis and thermography, helps in identifying potential issues before they lead to system failures.
To summarize, the use of regulating valves is integral to operational efficiency and safety in numerous industrial sectors. A deep understanding of valve types, material properties, flow characteristics, and maintenance strategies lays the foundation for optimal system design and longevity. By leveraging experience, expertise, authoritativeness, and trustworthiness in regulating valve management, industry professionals can significantly enhance operational reliability and efficiency, ultimately driving better outcomes and ensuring compliance with industry standards.