In the intricate world of mechanical systems, the relief valve holds a crucial role, often overshadowed by its more conspicuous counterparts. Yet, the significance of the relief valve cannot be understated, especially in systems where pressure regulation is paramount to both performance and safety.
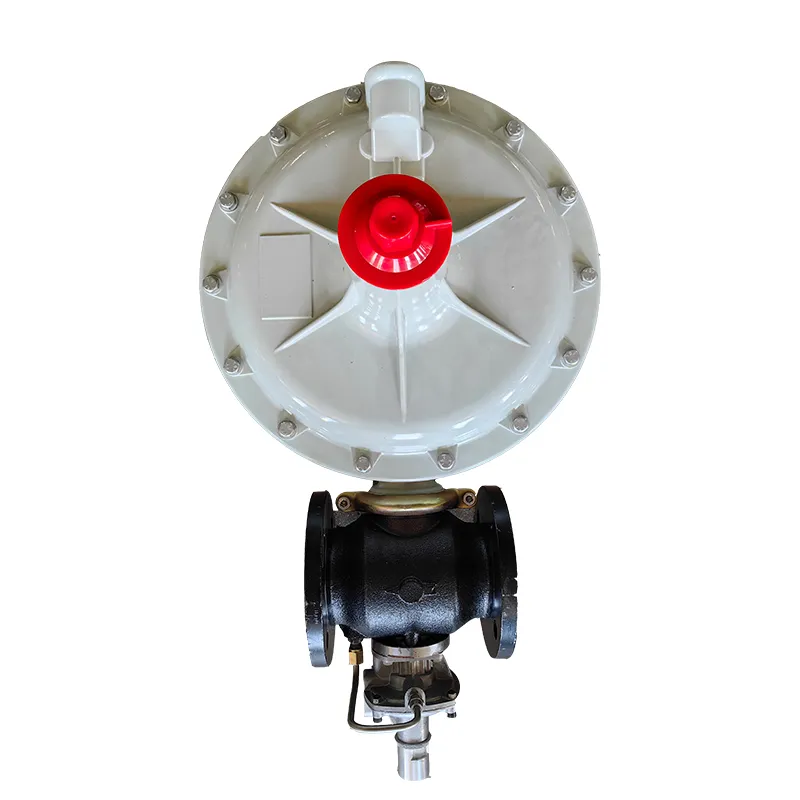
Relief valves, sometimes referred to as safety relief valves, are fundamental components in industries ranging from oil and gas to manufacturing and even in domestic water heating systems. At their core, relief valves are designed to control or limit pressure in a system; they do this by allowing the pressurized fluid to flow from an auxiliary passage out of the system.
Experience in working with relief valves shows that they are indispensable when it comes to system reliability. Imagine a scenario where a valve is improperly calibrated over-pressurization can lead to leaks, equipment failure, or even catastrophic explosions in severe cases. Optimal performance of a relief valve ensures that excess pressure is released safely, protecting both equipment and personnel. In industrial practices, the peace of mind provided by a correctly functioning relief valve contributes significantly to operational efficiency.
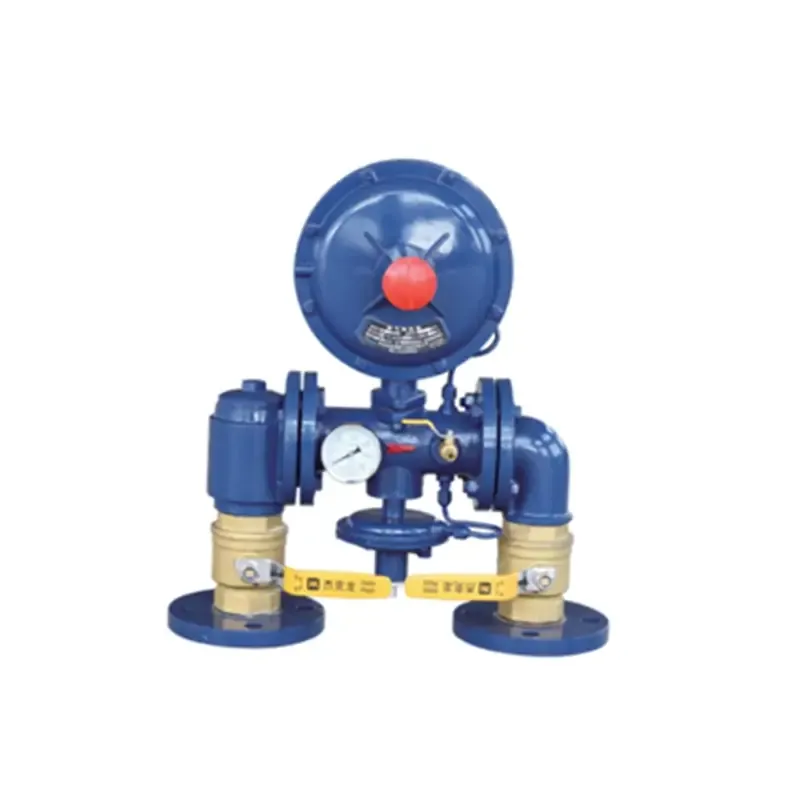
From an expertise perspective, understanding the specific requirements for relief valves based on application is critical. For instance, in chemical processing, the choice of material is crucial due to aggressive fluids or gases. Relief valves in such systems often need to be composed of stainless steel or other corrosion-resistant materials to withstand the harsh environment. Similarly, in steam applications, ensuring that the valve is capable of withstanding high temperatures is vital for the longevity and reliability of the equipment.
Selecting the right type of relief valve also demands authoritative knowledge of industry standards. For example, in the United States, the ASME (American Society of Mechanical Engineers) codes outline stringent parameters for valve operation and pressure ratings. Compliance with these standards is not merely a legal obligation but a testament to the manufacturer’s commitment to safety and quality.
relief valve
In the realm of trustworthiness, the brand reputation of relief valve manufacturers can significantly influence purchasing decisions. Leading manufacturers invest heavily in research and development, focusing on innovation to create valves that perform exceptionally under various conditions. They often provide extensive documentation, including test reports and certifications, further establishing their credibility in the competitive landscape.
Furthermore, maintenance practices play an essential role in the effective functioning of relief valves. Contrary to a set-and-forget approach, regular inspection and testing are integral to ensuring that these valves operate as intended when called upon. Systematic maintenance schedules, possibly including methods like in-situ testing or bench testing, enhance the longevity and dependability of the valves.
Moreover, the advent of digital monitoring technology in recent years marks a transformative phase in relief valve management. IoT (Internet of Things) integration enables real-time monitoring of valve status, ensuring that any deviations from optimal performance parameters are swiftly identified and rectified. This proactive approach not only enhances safety but also minimizes downtime, proving beneficial from a cost-management perspective.
In conclusion, the role of the relief valve in system safety and efficiency is vital. Its ability to prevent over-pressurization protects invaluable machinery and, more importantly,
human lives. As industry standards evolve and technology advances, the emphasis on expertise, authority, and trust in relief valve selection and maintenance will continue to grow. Understanding these factors and leveraging them effectively is essential for any business aiming to optimize its operations and safeguard its workforce and assets.