Safety relief valves are critical components in various industrial systems, serving as safeguards against excessive pressure build-up and potential equipment failure. Their importance cannot be overstated, as they ensure not only the safety of operations but also the longevity and efficiency of the equipment they protect. As an experienced professional in the field, I've gathered insights and expertise through years of hands-on experience and constant learning. This article aims to share valuable knowledge about safety relief valves that is both authoritative and trustworthy.
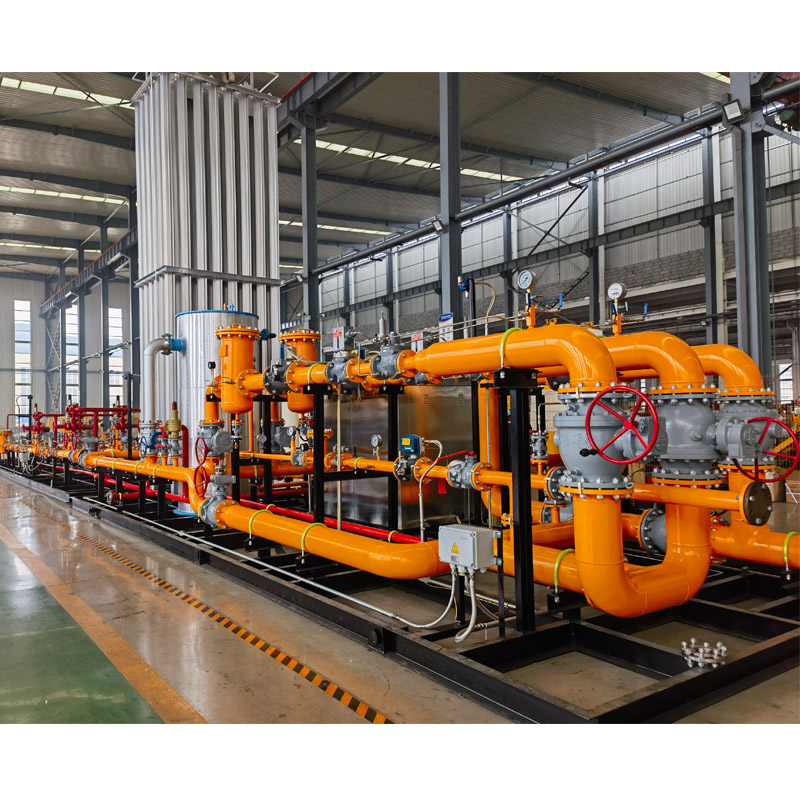
In industrial systems, maintaining optimal pressure levels is crucial. Safety relief valves are engineered to open at predetermined pressure levels, effectively venting excess pressure and preventing catastrophic failures. This functionality positions them as keystones of safety in various applications, ranging from chemical processing plants to steam systems.
Understanding the different types of safety relief valves is essential for selecting the right one for a specific application.
Two primary types include direct spring-loaded and pilot-operated relief valves. Direct spring-loaded valves are the most common, known for their simplicity and reliability. They consist of a spring mechanism that releases pressure once it surpasses a set threshold. Pilot-operated relief valves, on the other hand, offer precise pressure control by using system pressure to enhance the sealing force until it is necessary to release excess pressure.
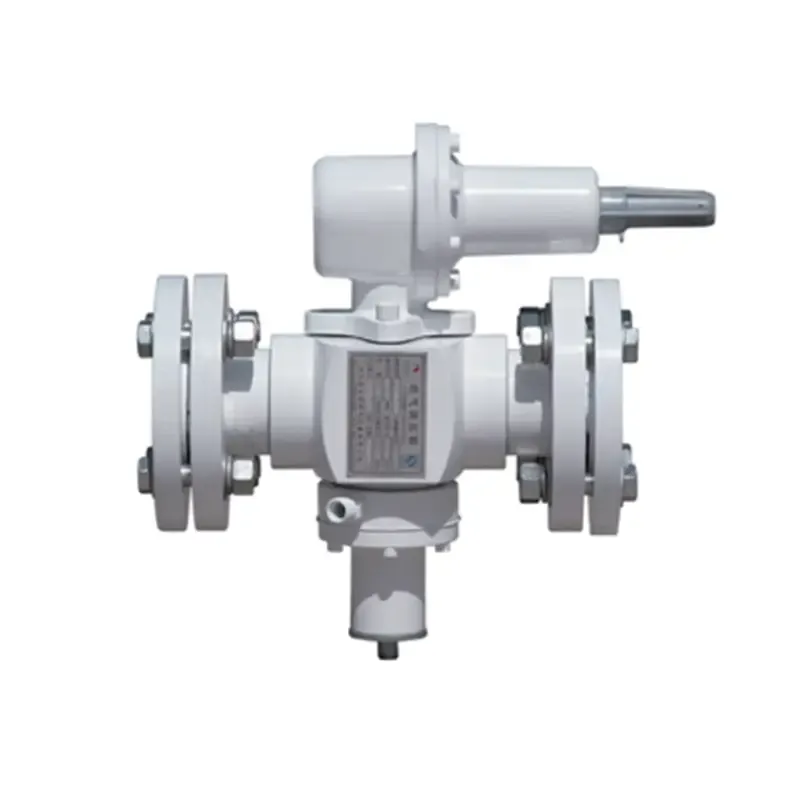
Selecting the appropriate material for a safety relief valve is equally important. The valve must withstand the specific chemical and physical conditions of the system it protects. Common materials include brass, stainless steel, and cast iron. Each material offers distinct advantages brass provides a good balance between cost and corrosion resistance, stainless steel is highly durable and suitable for corrosive environments, and cast iron offers robustness for lower-pressure applications.
safety relief valve
The installation of safety relief valves should adhere to rigorous standards to ensure efficacy and safety. Incorrect installation can compromise the valve's functionality, resulting in potential hazards. It's recommended that valves are installed at the highest point of the system and as close to the protected equipment as possible. Additionally, the discharge from the valve should be routed safely, with minimal back pressure, to a location where it cannot harm personnel or equipment.
Regular maintenance and testing of safety relief valves are imperative to their performance. Industry standards, such as those put forth by the American Society of Mechanical Engineers (ASME), provide guidelines on inspection intervals and procedures. Routine checks for signs of wear, corrosion, or damage are necessary, as well as full operational testing to ensure proper function. Calibration checks should be performed to confirm that the relief settings remain accurate over time.
Trust in the reliability of safety relief valves is built through adherence to quality standards and certifications. Buyers should seek valves that comply with recognized standards, such as ASME, API, or ISO, which ensure that the valves meet stringent safety and performance criteria.
In summary, safety relief valves are integral to the safe operation of industrial systems. Expertise in their selection, installation, and maintenance can prevent dangerous incidents and optimize system performance. By understanding the nuances of these valves and relying on products that meet the highest standards, businesses can enhance both safety and operational reliability.