Safety valves are critical components in a myriad of industrial applications, serving as the last line of defense against overpressure scenarios. Their role cannot be overstated as they safeguard against catastrophic failures, thereby protecting both human lives and equipment. The market today is flooded with various types of safety valves, each with a specialized function and application. Understanding the intricacies of these devices is vital for professionals in fields such as chemical processing, oil and gas, and pharmaceuticals.
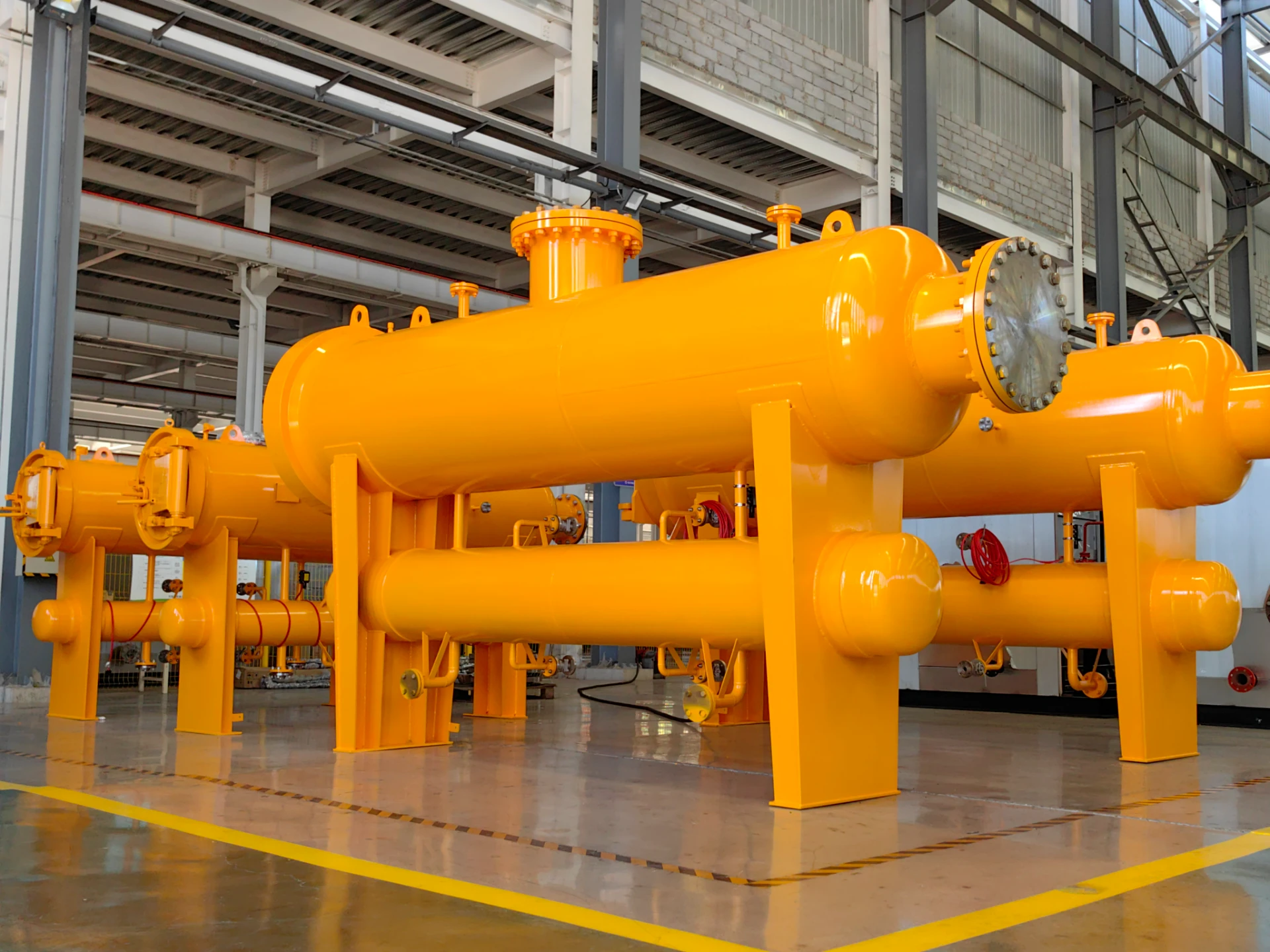
The essence of a safety valve is to automatically release a substance—liquid, gas, or steam—once pressure or temperature exceeds preset limits. This function is pivotal in maintaining the integrity of pressurized systems. For example, in chemical plants, where operating conditions must remain within stringent parameters, safety valves are indispensable in preventing chemical releases and ensuring safe operational environments.
Expertise in the selection, installation, and maintenance of safety valves can lead to significant operational efficiencies. Selecting the right valve involves understanding the specific application requirements. For instance, spring-loaded safety valves are commonly used in steam applications due to their rapid response capabilities. However, pilot-operated valves might be preferred in scenarios where minimal emissions are crucial.
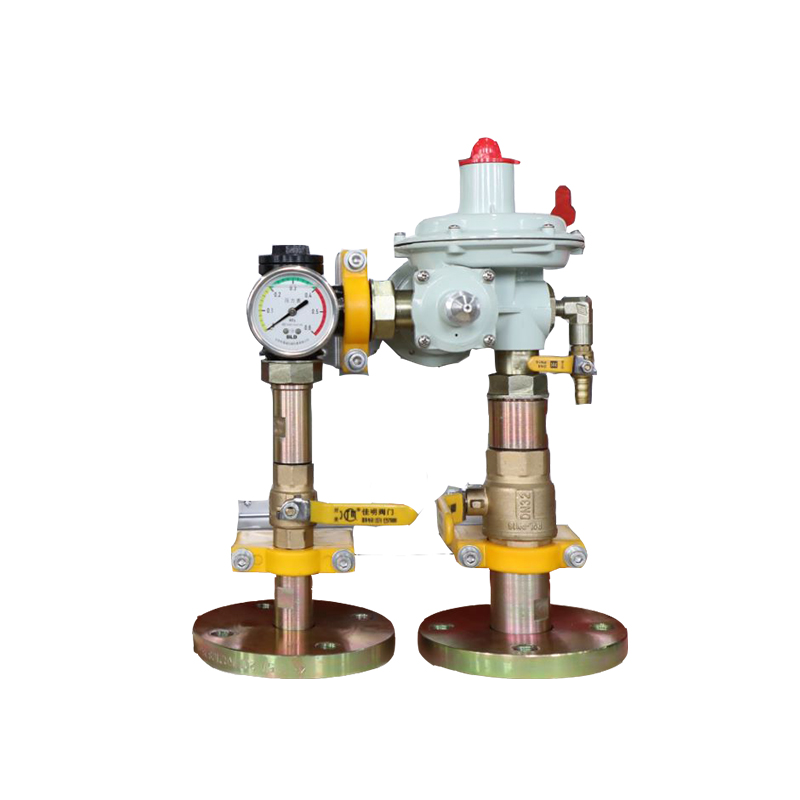
Installation expertise involves ensuring that the valves are properly integrated into the system to operate effectively. It’s crucial to account for installation position, orientation, and environmental factors that could affect valve performance. Improper installation can lead to valve malfunction, thereby posing substantial risks.
Moreover, regular maintenance is necessary to ensure that safety valves function as intended. This includes periodic testing and calibration, which are critical to verify that the set pressure is within the defined threshold. A neglected valve can become a ticking time bomb, potentially resulting in operational downtime or even disastrous events.
safety valve
In terms of authoritativeness, organizations such as the American Society of Mechanical Engineers (ASME) and the International Standards Organization (ISO) set the standards for safety valve performance and specifications. Adhering to these guidelines not only ensures compliance but also enhances the reliability and trustworthiness of the installed valves. Professionals should stay updated with the latest revisions of these standards to ensure the continuing efficacy of their safety systems.
The trustworthiness of a safety valve also lies in its manufacturer. Opting for products from reputable and certified manufacturers ensures a level of quality and reliability. These manufacturers often provide warranties and comprehensive support services that are indispensable in high-stakes industries.
Real-world experience further enhances the understanding of safety valve operations. An industry professional once encountered a situation where a malfunctioning safety valve in a refinery nearly caused a severe incident. A thorough root-cause analysis revealed that improper maintenance procedures were implemented. This case underscores the critical need for both robust maintenance protocols and continuous staff training to mitigate potential risks.
In conclusion, the criticality of safety valves in industrial applications cannot be understated.
Their role in maintaining safety and operational integrity is paramount. Mastery of valve selection, installation, and maintenance, combined with adherence to industry standards, ensures these devices perform optimally. Dependence on reputable manufacturers further adds a layer of reliability. As industry demands evolve, staying informed and prepared with the latest technologies and methodologies remains essential for any professional engaged with safety valves.