Choosing the right gas heat exchanger is crucial for industries aiming to maximize efficiency and sustainability. The market offers a variety of options, each with distinct features tailored to specific needs. Diving into the intricacies of gas heat exchangers reveals insights into their operation, benefits, and the factors to consider when selecting one.
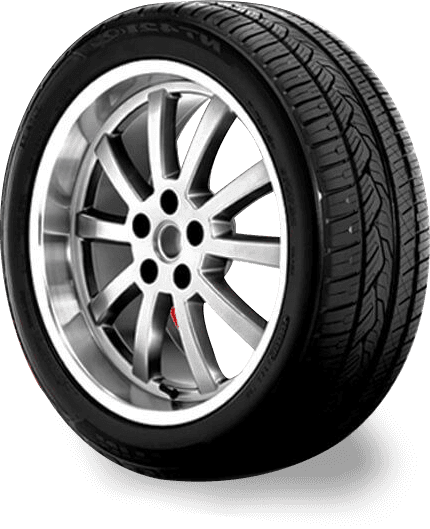
Gas heat exchangers are engineered to transfer heat between two or more fluids without them coming into direct contact. Their application spans various industries, from power generation to chemical processing, each demanding precise thermal regulation to ensure optimal performance. The importance of these devices cannot be understated; they contribute to energy savings, operational efficiency, and overall system longevity.
Experience in the field highlights the need for careful consideration of the thermal properties of the gas in question. For instance, gases with higher thermal conductivity require exchangers designed to handle rapid heat transfer without compromising safety. The choice of materials for the heat exchanger, such as stainless steel or copper, is influenced by the corrosivity and temperature range of the gas being processed. Real-world applications have shown that mismatches between materials and gases can lead to premature equipment failure and unexpected operational costs.
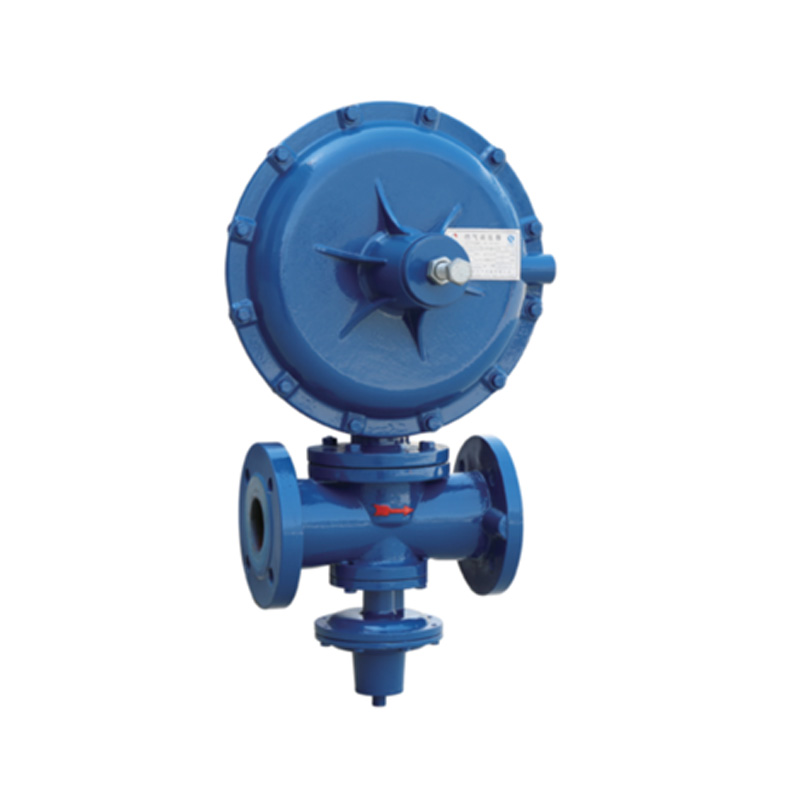
From an expertise standpoint, understanding the different configurations of gas heat exchangers is fundamental. The most common types include shell and tube, plate,
and air-cooled exchangers. Shell and tube exchangers are renowned for their durability and versatility, making them ideal for high-pressure environments. Plate exchangers offer superior heat transfer efficiency and are suitable for space-constrained installations. Air-cooled exchangers, on the other hand, are perfect for applications with limited water resources, providing a sustainable cooling solution.
For professionals advocating for energy efficiency, the discussion extends to the integration of innovative technologies such as finned tubes or enhanced surface designs. These advancements significantly boost the heat transfer rate, reducing energy consumption and environmental impact. Companies investing in state-of-the-art heat exchangers often reap the benefits of reduced operational costs and improved system reliability.
Gas heat exchanger
Authoritativeness in the industry is solidified through adherence to regulatory standards and certifications, such as ASME or TEMA, which ensure safety and performance benchmarks are met. Working with manufacturers that uphold these standards guarantees that the equipment is reliable and capable of meeting industry demands. Additionally, engaging in partnerships with suppliers who provide comprehensive after-sales support and maintenance services enhances the operational lifespan of gas heat exchangers.
Trustworthiness in selecting a gas heat exchanger comes from proven track records and customer testimonials. Conducting thorough research and obtaining references from previously satisfied clients can provide assurance of the equipment's capability and the supplier's reputation. Transparency in specifications and performance data is also a critical factor in building trust, enabling informed decision-making based on factual information.
The future of gas heat exchangers points towards increased customization and integration with smart technologies. As industries push for digital transformation, incorporating IoT sensors and real-time monitoring systems will enable predictive maintenance and process optimization. Such advancements promise not only enhanced system performance but also improved environmental stewardship.
In conclusion, the selection of a gas heat exchanger should be guided by a comprehensive understanding of the specific application requirements and an evaluation of the technical specifications, operational benefits, and compliance standards. By leveraging experience, expertise, authority, and trustworthiness, industries can make informed choices that align with their operational goals, driving efficiency and sustainability in their processes.