The evolution of high-pressure technology has profoundly impacted various industries, from oil and gas to food processing and medical equipment. Among these innovations, the pressure tube stands out for its unparalleled efficiency and versatility. A deep dive into this remarkable product reveals a blend of engineering prowess and practical application that transforms theoretical concepts into real-world solutions.
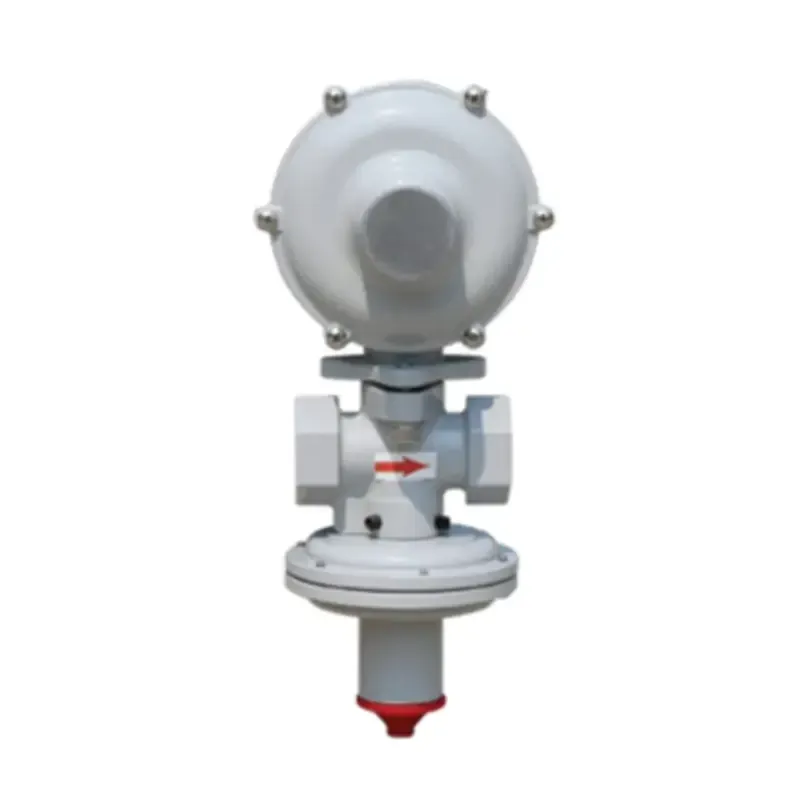
The primary function of a pressure tube is to contain and manage fluids or gases under significant pressure. This capability makes it an essential component across sectors requiring precision and reliability. Industries such as aerospace, automotive, and energy have leveraged pressure tubes to enhance their operational safety, efficiency, and productivity.
In aerospace, for example, pressure tubes are critical in hydraulic systems that control aircraft landing gear, brakes, and flight controls. The extreme conditions faced by these components necessitate a design that prioritizes durability and resilience. Manufacturers often employ materials like stainless steel and titanium, which can withstand high pressures and resist corrosion, thereby extending the lifespan of the systems.
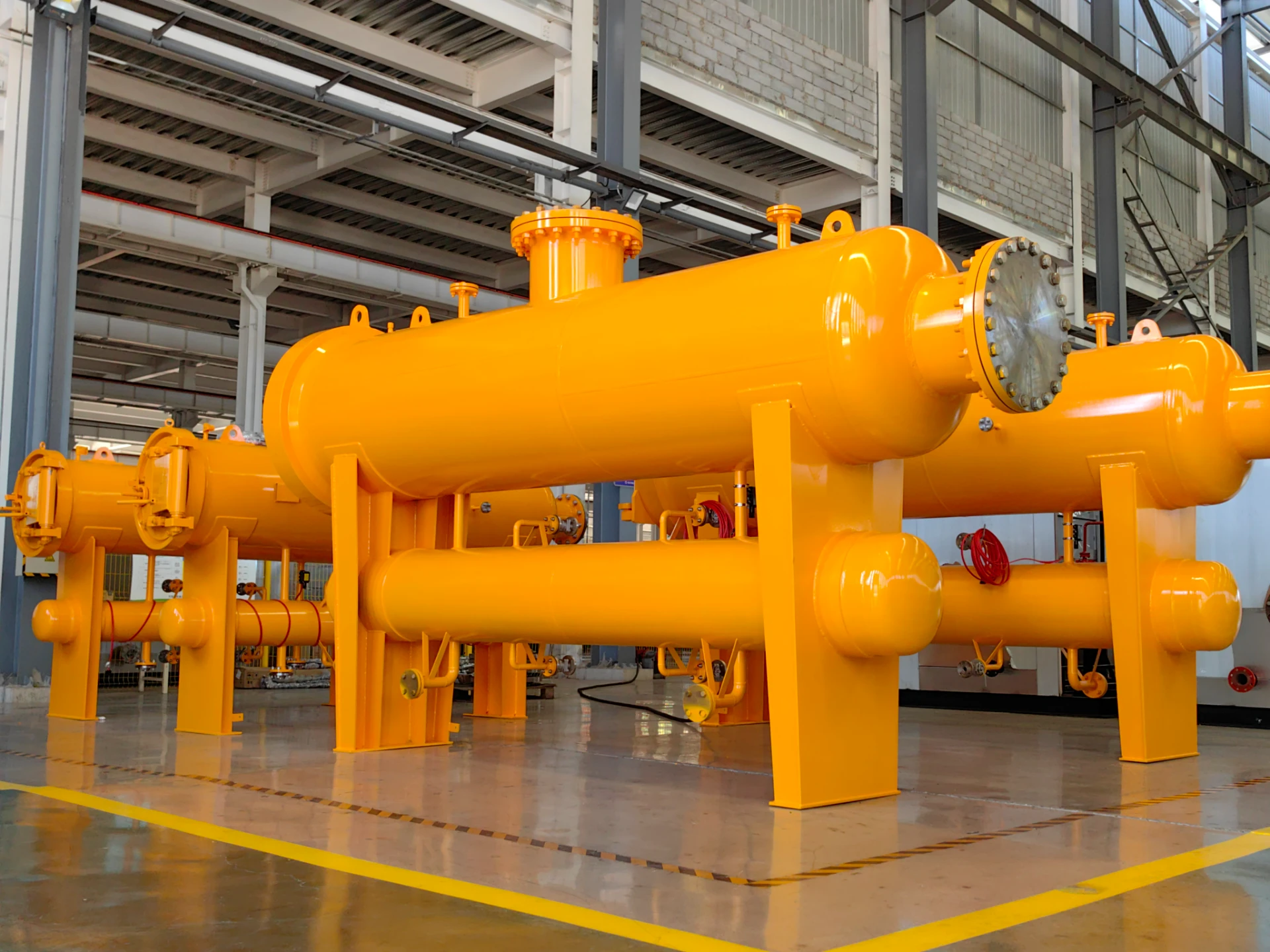
From a technical standpoint, the design of pressure tubes involves meticulous calculations and testing. Engineers consider factors such as stress distribution, fatigue life, and failure modes to optimize tube construction. Often, computational simulations are performed to predict tube behavior under various conditions, which helps refine designs before physical prototypes are developed.
Oil and gas sectors utilize pressure tubes in multiple applications, including wellhead control and downhole drilling tools. Here, the tubes must cope with harsh environments characterized by high pressure and corrosive substances. Advanced coatings and material selection are crucial in these scenarios to prevent catastrophic failures and ensure uninterrupted operations. Companies in this field often collaborate with research institutions to innovate and improve the materials and designs used in pressure tubes, staying ahead of evolving industry demands.
Pressure pipe
In the medical field, the precision and reliability of pressure tubes are harnessed in devices like ventilators and infusion pumps. The ability to accurately control fluid dynamics is critical in life-saving equipment, where even minor malfunctions can have serious consequences. Medical-grade pressure tubes are rigorously tested to meet international standards, assuring healthcare providers of their safety and efficacy.
Trustworthiness in manufacturing is another critical aspect that producers of pressure tubes strive to uphold. Certifications by recognized bodies such as the American Society for Testing and Materials (ASTM) add a layer of assurance for buyers regarding the quality and performance of these tubes. Companies committed to quality not only comply with such standards but often exceed them, further solidifying their reputation in the market.
Developments in nanotechnology and new material sciences continually impact the future of pressure tube technology. Innovations such as self-healing materials and smart sensors embedded in tubes are under exploration, potentially revolutionizing how pressure tubes function and monitor their condition. These advancements promise not only enhanced durability but also intelligent systems capable of predictive maintenance, reducing downtimes and preventing unexpected failures.
A company's expertise in pressure tube production significantly influences its market position. Expertise is established through years of research and development, a deep understanding of client needs, and a robust feedback loop from product performance in the field. Leading firms invest heavily in R&D, continuously refining their products based on the latest technological advancements and industry trends.
In summary, pressure tubes are much more than just components; they are critical to the success and safety of numerous industries worldwide. Their evolution encapsulates the intersection of engineering ingenuity and practical necessity, reflecting a broader commitment to reliability and innovation. As new technologies emerge and demands grow, pressure tubes will undoubtedly play a pivotal role in shaping industries of the future.