Pressure regulating valves, known as صمام تنظيم in Arabic, play a crucial role in various industrial and domestic applications, ensuring the smooth operation and safety of fluid systems. Proper understanding and utilization of these valves can significantly impact efficiency and operational costs, making high-quality information essential for both seasoned professionals and newcomers to the field.
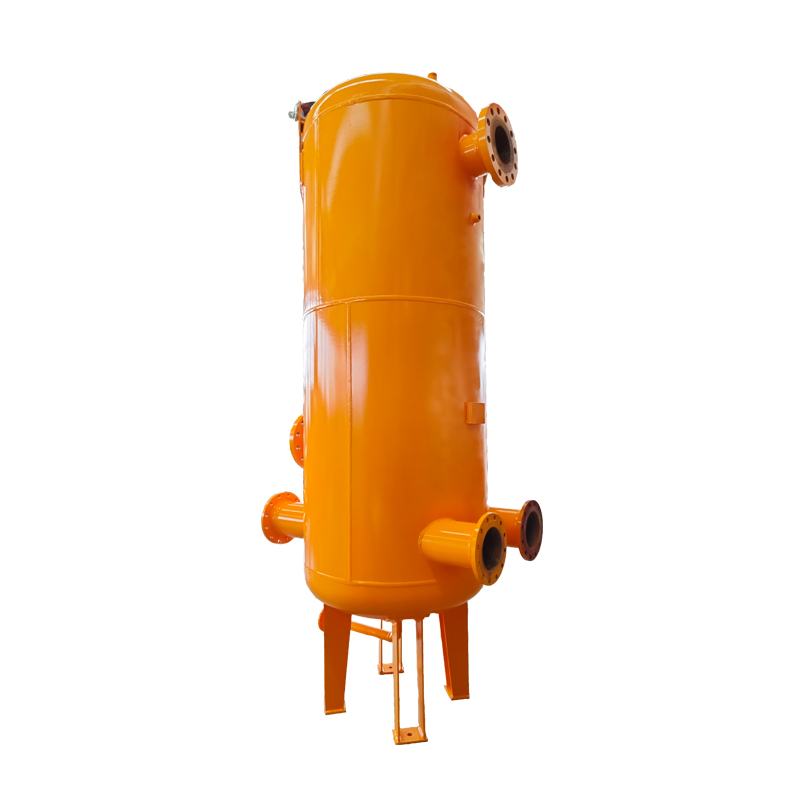
Pressure regulating valves are designed to maintain a constant output pressure irrespective of changes in input pressure and flow conditions. This constancy is vital in applications ranging from water supply systems, where precise pressure control can prevent pipe burst or leaks, to complex chemical processes where exact pressure levels are required for safety and quality control.
One of the standout advantages of these valves is their ability to improve process efficiency. By maintaining a stable pressure, they allow systems to operate more consistently, which can lead to energy savings. For example, in steam systems, correctly adjusting the pressure can reduce the flash steam, saving energy and improving overall system performance. Understanding the specific requirements of the system and selecting a valve that can handle the required flow rate and pressure is critical.
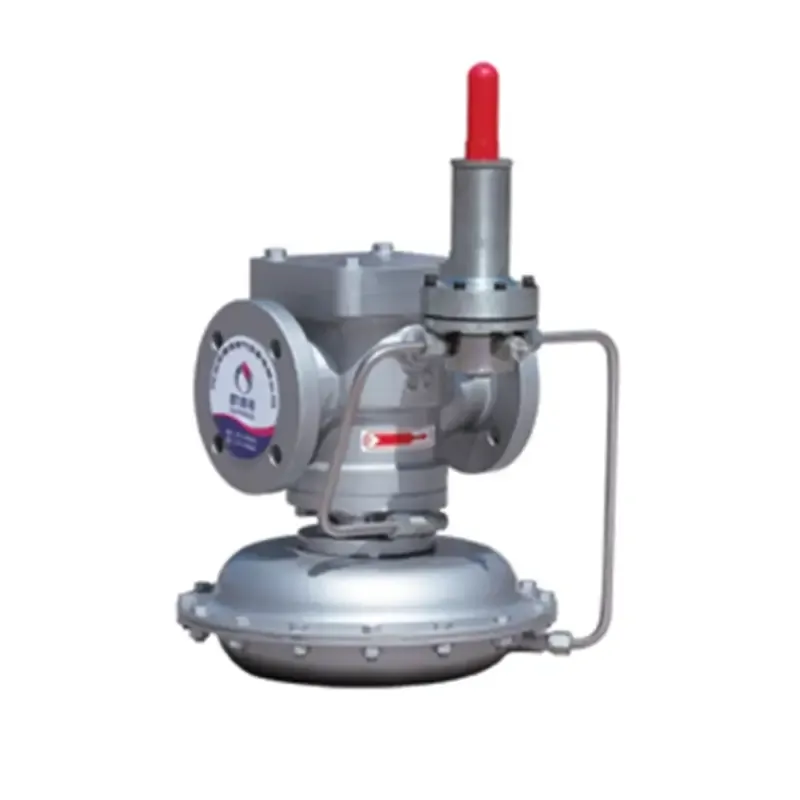
In terms of expertise, selecting the right pressure regulating valve involves understanding the specific needs of the application. Valves come in various types, including direct-acting, pilot-operated, and electrically actuated models. Each type has its advantages and suitability for different situations. Direct-acting valves, for instance, are more suitable for low-flow applications, offering simplicity and reliability. In contrast, pilot-operated valves are designed for higher flows and are often used in larger, more complex systems.
Authoritativeness in this field comes from thorough knowledge and adherence to industry standards. Reputable manufacturers adhere to rigorous testing and certification processes to ensure their valves meet or exceed international standards. For end-users, well-documented performance data and compliance with standards such as ASME, API, or ISO can enhance trust and aid in making informed purchasing decisions.
regulating valve
An often overlooked aspect is the material composition of these valves. Depending on the fluid type, temperature, and pressure, materials can range from stainless steel to specialized alloys. Corrosion resistance, thermal stability, and strength are crucial factors that contribute to the longevity and reliability of a valve. Selecting a valve with the appropriate material can prevent premature failures and costly downtime.
Manufacturers play an essential role in providing expertise and trustworthiness. By offering detailed product specifications, maintenance recommendations, and customization options, they help users optimize their systems. Training and support services can further enhance the user's ability to effectively implement and maintain these valves, ensuring optimal performance over their operational life.
To gain practical insights, one can look at case studies from industries that have successfully implemented pressure regulating valves. In the oil and gas sector, for instance, using advanced pilot-operated valves has led to improved control over extraction processes, significantly reducing environmental risks and maximizing yield. Similarly, in the food and beverage industry, precise pressure control is indispensable for maintaining product quality and safety standards.
In conclusion, the successful implementation of pressure regulating valves hinges on a combination of expertise in valve selection, a thorough understanding of system requirements, and trust in the manufacturer's quality and support. By focusing on these elements, industries can achieve enhanced performance, safety, and cost-effectiveness in their operations. This makes pressure regulating valves an indispensable component in any system that requires precise pressure control.